摘要
传统灌浆套筒制造过程繁琐、原材料成本高且灌浆质量难以保证,限制了中国预制装配式建筑的推广。为促进建筑行业的经济、环保和高效发展,本课题组研发了一种新型钢筋灌浆套筒连接技术,采用了“滚压螺旋肋灌浆套筒”和“类宾汉流体灌浆料”,钢筋与灌浆料、灌浆料与套筒之间形成了更加紧密的机械锁合,显著提高了构件连接后的承载力。该技术具有成本低廉、施工简便、灌浆质量易于保证等优点。为了探究该连接体系下钢筋的最小锚固长度及钢筋对中对接与偏置对接在连接性能上的差异,通过对 34 个接头试件进行单向拉伸试验,分析了试件的破坏模式及各项结构性能指标。研究结果表明:钢筋在套筒内部偏置对接与对中对接在连接性能上差别不大;滚压套筒内的内凸肋显著增强了对灌浆料滑移的阻抗作用,可提供足够的黏结锚固以达到连接性能要求。初步结果显示,在该连接方式下钢筋的最小锚固长度可采用 10 倍钢筋直径,并采用偏置对接方式。
Abstract
The traditional grouting sleeve manufacturing process is hindered by its complexity, high raw material costs, and challenges in ensuring grouting quality, which has restricted the widespread adoption of prefabricated assembly buildings in China. To address these issues and promote economical, environmentally friendly, and efficient development in the construction industry, an innovative steel grouting sleeve connection technology was developed. This new approach employs a “ rolled spiral rib grouting sleeve” in combination with “Bingham-like fluid grout,” which creates a more secure mechanical interlock between the reinforcement bar and grout, as well as between the grout and sleeve. This enhanced interlocking mechanism significantly improves the load-bearing capacity of connected components. The developed technology offers several advantages, including costs reduced, construction processes simplified, and grouting quality assurance improved. To determine the minimum anchorage length of reinforcement bars within this connection system and to compare the connection performance between centered and offset butt joints, unidirectional tensile tests on 34 joint specimens were conducted, and the damage modes and various structural performance indices of the specimens were thoroughly analyzed. The results indicate that the differences in connection performance is minimal between offset and centered butt joints within the sleeve. Additionally, the internal convex ribs within the rolled sleeve significantly enhance grout slip resistance and provide sufficient bond anchorage to meet connection performance requirements. Preliminary findings suggest that the minimum anchorage length of the reinforcement in this proposed connection system can be as short as 10 times the diameter of the reinforcement for offset butt joints.
钢筋灌浆套筒连接作为装配式混凝土结构中节点纵向钢筋连接的主流技术方法,具有传力路径明确、约束外径小、承载力强等诸多优点,但仍存在制造工艺及施工工艺复杂且灌浆质量不易保证等缺点。目前,国内外对于钢筋灌浆套筒连接性能相关研究主要以试验探究、理论公式推导和数值模拟分析为主[1-8],例如:Ling 等[3]通过对 4 种接头施加单向荷载,对试件的黏结强度、破坏模式等进行了分析,结果显示在套筒的约束下,钢筋锚固长度可取 9 倍钢筋直径。 Feng 等[4]通过拉伸和循环载荷试验探究了钢材灌浆套筒接头的抗拉性能,结果表明钢材不对中对接头的抗拉性能影响较大。对于钢筋灌浆套筒连接接头,JGJ 107—2016 《钢筋机械连接技术规程》 [9]给出了其极限抗拉强度相关要求。为解决传统钢筋灌浆套筒连接存在的问题,哈尔滨工业大学课题组自主研发了新型钢筋灌浆套筒连接技术[10-13],具有生产成本低、施工工艺简单、灌浆质量易保证的优点。本文主要通过单向拉伸试验探究在此新型连接体系下钢筋的最小锚固长度及钢筋对中对接与偏置对接在连接性能的差异,为后续进行反复拉压试验及混凝土构件连接的抗震性能研究奠定基础。
1 试验概况
1.1 试件设计
采用螺旋肋灌浆套筒、类宾汉流体灌浆料及 HRB400 钢筋制作了 34 个钢筋沿套筒内壁对接连接试件。试件详细参数见表1,以试件 UT-8-5d-B 为例:UT 表示单向拉伸试验; 8 表示钢筋直径为8 mm; 5d 表示钢筋在套筒内的锚固长度为 5 倍钢筋直径; A 表示钢筋对中对接,B 表示钢筋沿套筒内壁偏置对接,钢筋对接试件连接见图1。
表1试件编号与尺寸参数
Tab.1 The number and size parameters of the specimen
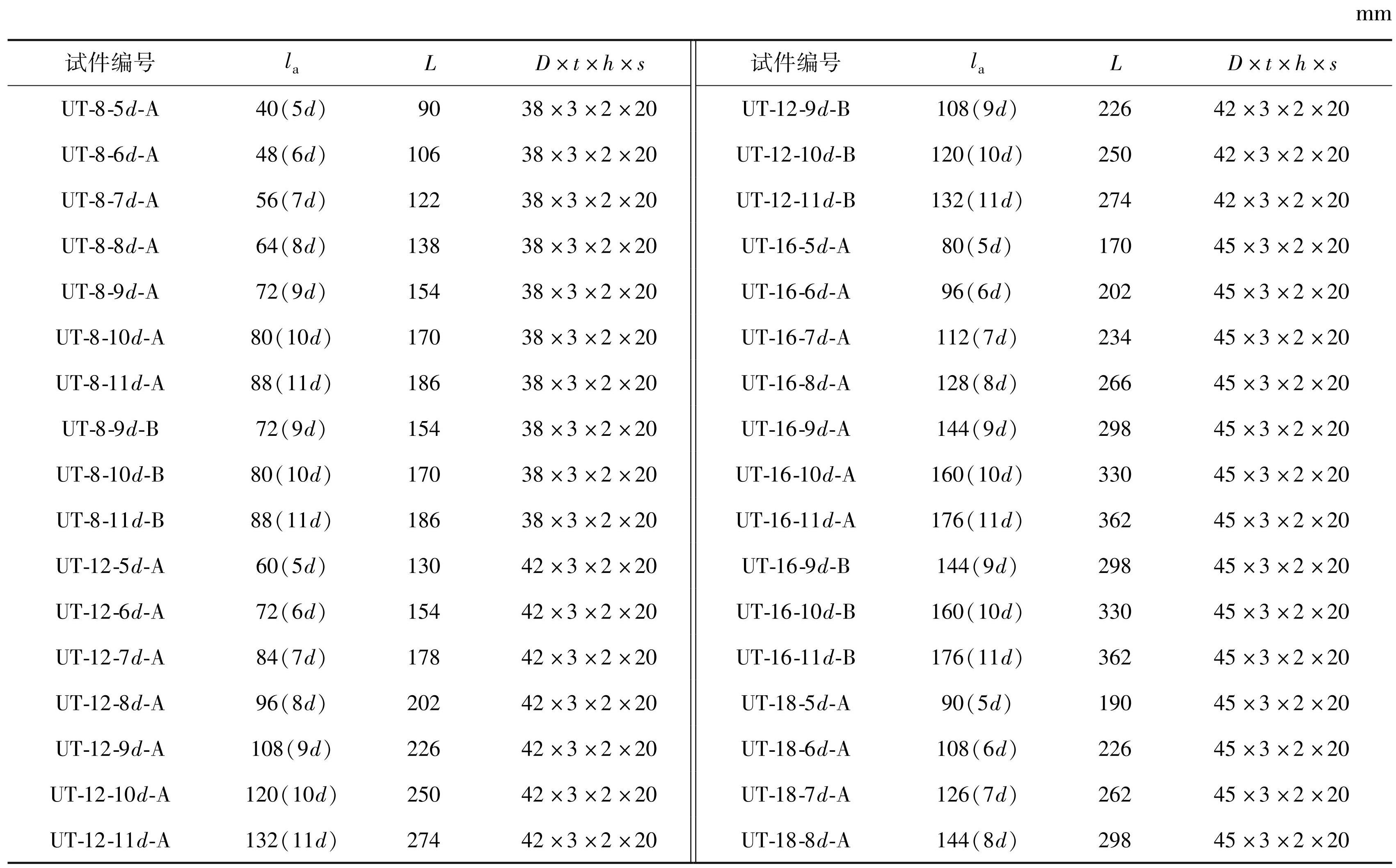
注:l a为锚固长度,L 为套筒长度,D 为套筒外径,t 为套筒壁厚,h 为套筒肋高,s 为套筒肋间距。
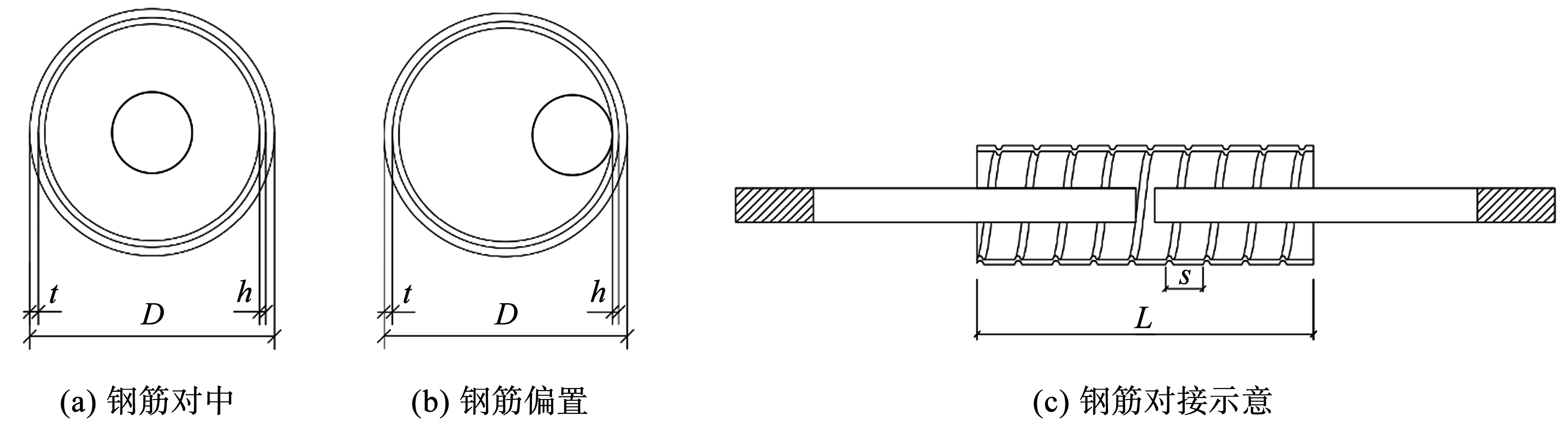
图1钢筋对接试件连接示意
Fig.1Schematic diagram of the cross-section of the steel bar butt joint specimen
1.2 材料性能
1.2.1 螺旋肋钢管
制作灌浆套筒所用原材料为滚压螺旋肋钢管,钢号为 20。参考规范[14],制作 3 组管材纵向弧形拉伸试件进行力学性能拉伸试验,测定的钢管力学性能见表2。
表2螺旋肋钢管力学性能
Tab.2 Material properties of spiral ribbed steel pipes

1.2.2 钢筋
对 8、12、16 和 18 mm 4 种直径的钢筋分别制作 3 根原材进行拉伸试验,钢筋力学性能见表3。
1.2.3 灌浆料
为增强类宾汉流体灌浆料的流动性,对石英砂的粒径级配进行优化,并进行压折试验,28 d 抗折强度试件尺寸为 40 mm × 40 mm × 160 mm,28 d 抗压强度采用抗折试验后的半截试体的中部进行抗压试验测得,受压面积为 40 mm × 40 mm。材料性能见表4。
表3钢筋力学性能
Tab.3 Material properties of reinforcing bars
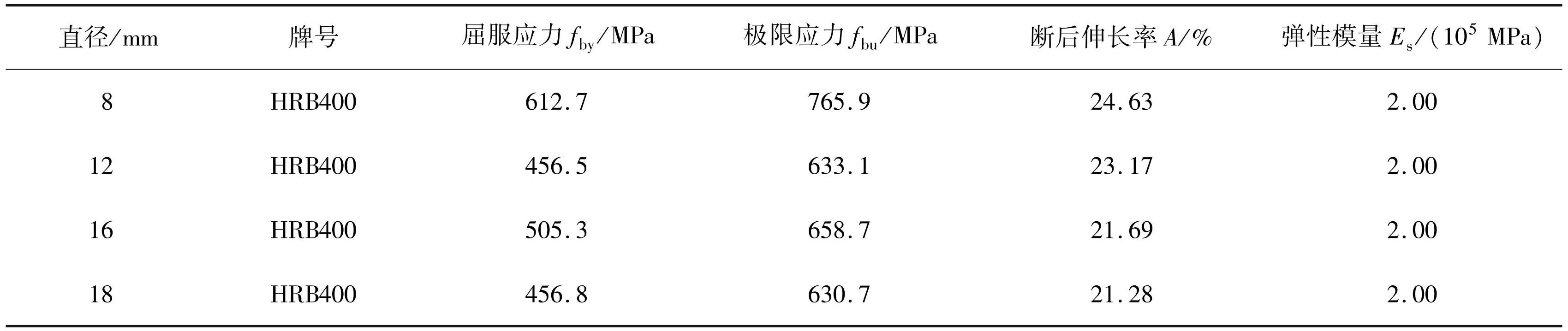
表4灌浆料材料性能
Tab.4 Material properties of grouting material

1.3 加载及量测
1.3.1 应变片布置
第一批单向拉伸试件的应变片共 5 组,套筒两端钢筋处对称布置两组应变片; 套筒表面中部、端部处布置 3 组应变片,每组应变片测量沿套筒纵向及环向的应变。第二批对中对接试件的应变片共 6 组,其中位于套筒两端钢筋处的应变片对称布置; 套筒表面中部对称布置两组、端部及 1 / 4 处分别布置 1 组应变片,每组应变片测量沿套筒纵向及环向的应变。第二批偏置对接试件的应变片共 11 组,其中位于套筒两端钢筋处的应变片对称布置; 套筒表面中部、端部及 1 / 4 处分别布置 3 组应变片,每组应变片测量沿套筒纵向及环向的应变。其中,位于套筒两端钢筋处的应变片用 ZG 表示,套筒表面每组应变片分别用 ZT 和 HT 表示。测点布置见图2。
1.3.2 加载方案
单向拉伸试验采用 1 000 kN 万能试验机,分两次进行加载。第一次加载采用力控制加载,从 0 加载至 0.6f yk再卸载至 0,加载速率为 2 N/(mm 2·s)。当钢筋即将到达屈服阶段时开始二次加载阶段,采用位移控制加载,加载速率为 0. 05 mm / s。当试件发生钢筋拉断、拔出或灌浆料拉断现象时停止试验。
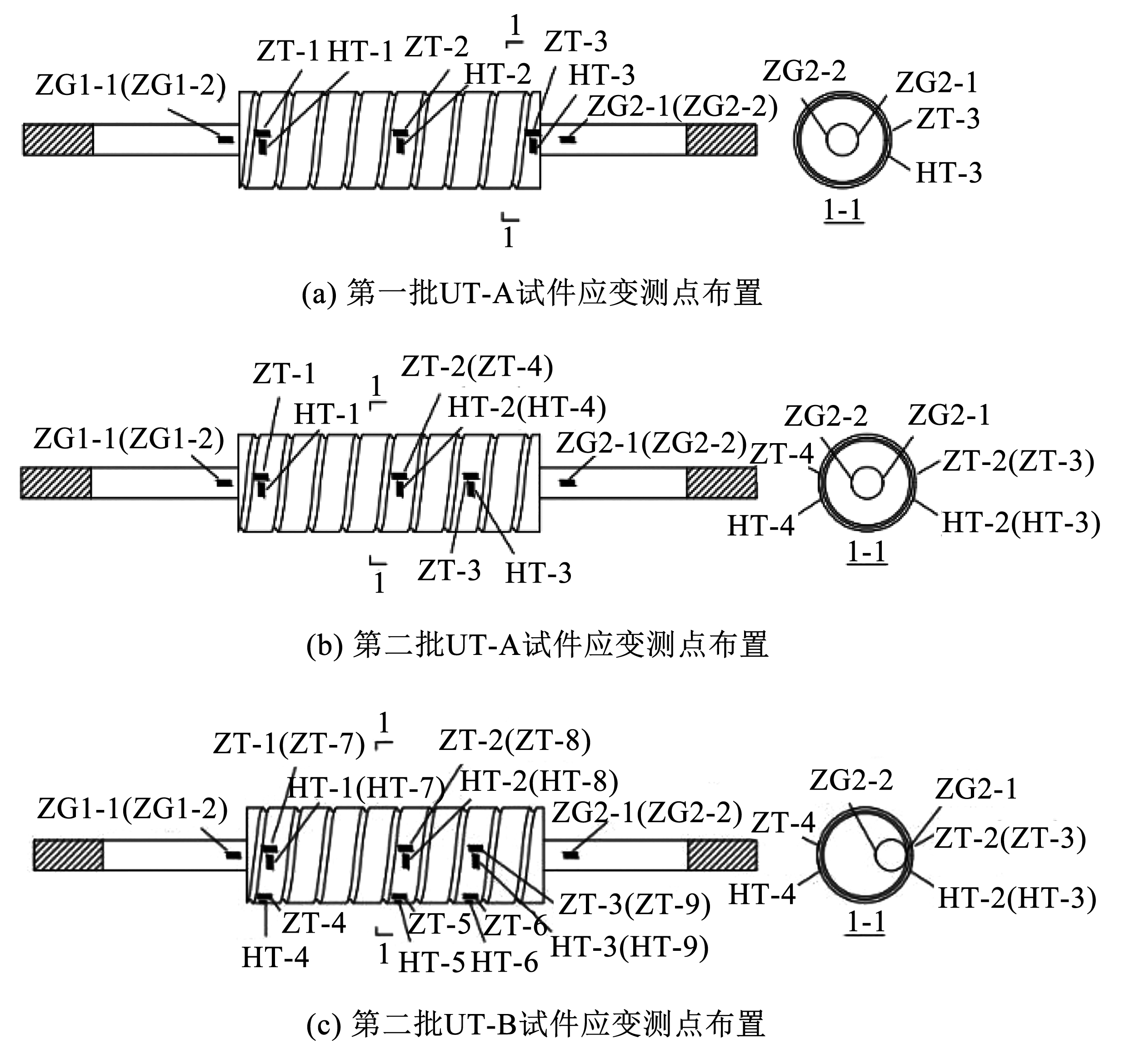
图2单拉试件应变测点布置
Fig.2Layout of measurement points of strain of unidirectional tensile specimen
2 试验结果
此次单向拉伸试验的试验结果主要包括试件破坏模式及破坏现象、连接性能关键指标、连接荷载-位移曲线以及螺旋肋套筒表面纵向、环向应变分布规律。
2.1 破坏模式和结构性能指标
试件共出现了 3 种破坏模式: 钢筋被拉断(图3)、钢筋拔出(图4)和灌浆料断裂滑移(图5)。其中,钢筋拔出破坏和灌浆料断裂滑移破坏以荷载进入下降段,钢筋或灌浆料被缓慢拔出为破坏标志。
对于钢筋被拉断的试件,随着荷载的增大,钢筋的变形逐渐增大,套筒一端钢筋出现颈缩效应,随着 “砰”的一声钢筋被拉断。对于发生钢筋拔出破坏的试件,随着荷载的增大,钢筋的月牙肋将灌浆料剪碎,钢筋与灌浆料之间的机械咬合力逐渐消失,钢筋随之被拔出。对于发生灌浆料断裂滑移的试件,由于套筒端部灌浆料与套筒之间的黏结性能较弱且灌浆料内部存在空腔,故随着荷载的增大灌浆料被拉断,试件发生破坏。
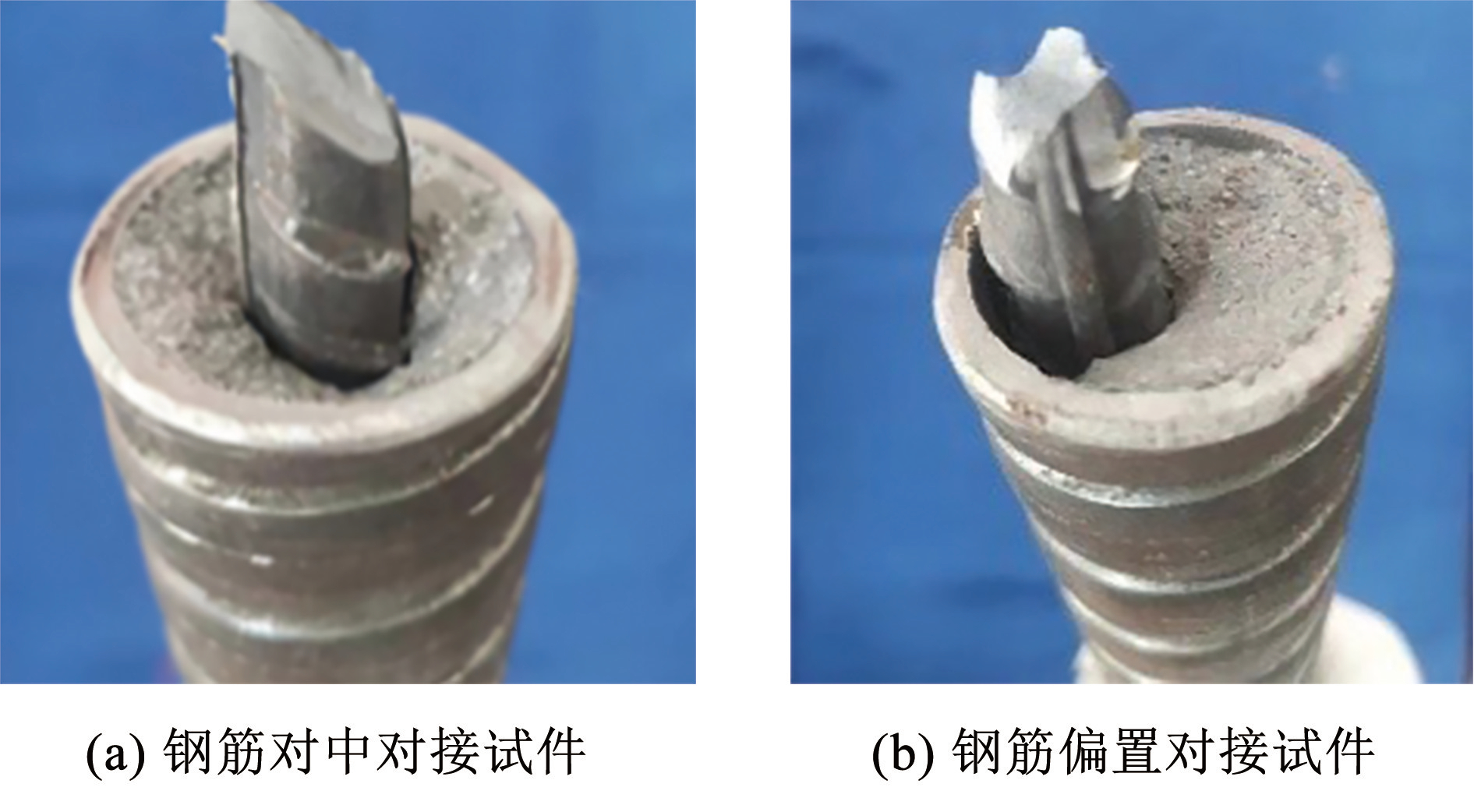
图3钢筋被拉断
Fig.3Fracture failure of steel bar
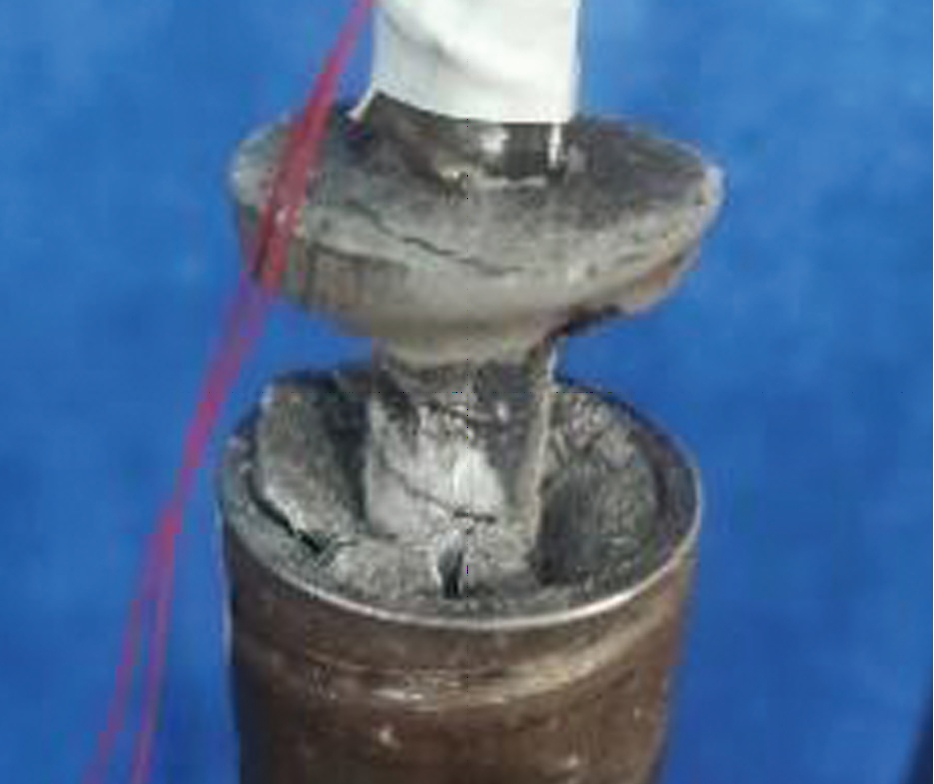
图4钢筋拔出
Fig.4Bond slip failure of steel bar
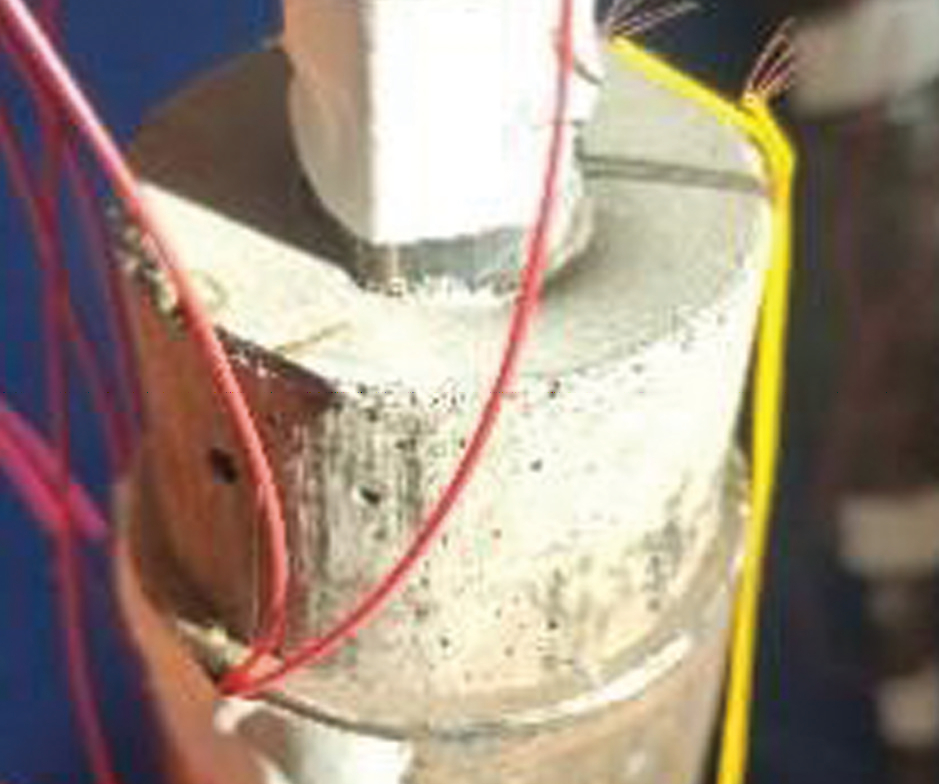
图5灌浆料断裂滑移
Fig.5Slip failure of grouting material
从连接性能看,当钢筋的锚固长度小于 9d 时,试件破坏模式均为钢筋被拔出或灌浆料断裂滑移。由此可以看出,当钢筋的锚固长度不足时,由于钢筋与灌浆料之间的机械咬合力大于套筒与灌浆料之间的机械咬合力,易发生灌浆料断裂滑移破坏。当钢筋的锚固长度为 9d 及以上时,除 UT-8-9d-A/ B 和 UT-8-10 / 11d-A 外,均为钢筋达到极限强度而产生断裂破坏。单拉试件破坏图见表5,连接性能指标见表6。
表5单向拉伸试件破坏图
Tab.5 Failure diagram of uniaxial tensile specimen
表6单向拉伸试件连接性能指标
Tab.6 Key indicators of structural performance of uniaxial tensile specimen
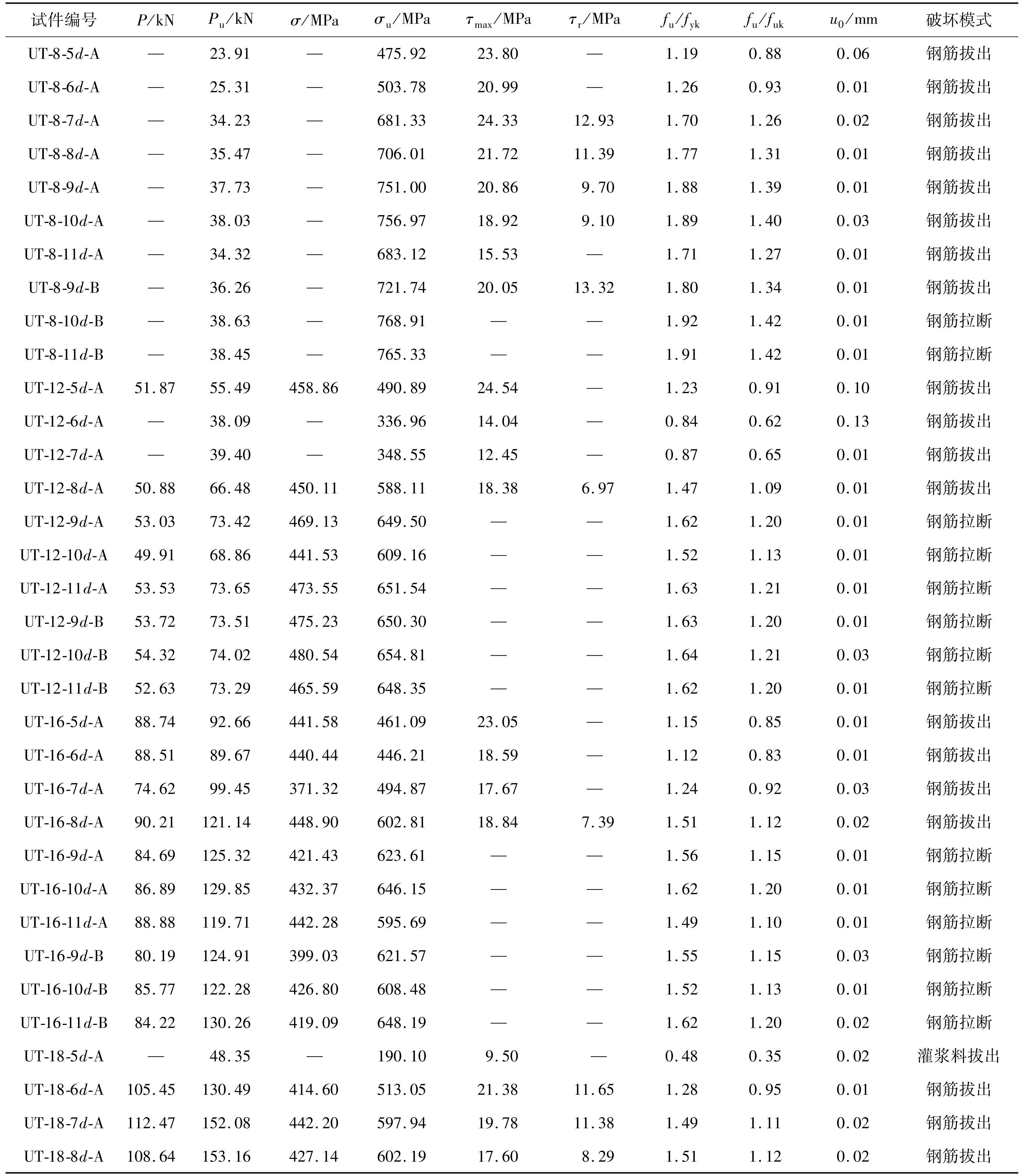
注:P 为接头屈服承载力,Pu为接头极限承载力,σ 为接头屈服应力,σu为接头极限应力,τmax为接头黏结强度,τr为接头残余黏结强度,fu为抗拉强度,u0为接头试件加载至 0.6 倍钢筋屈服强度标准值并卸载后在规定标距内的残余变形。
由表6可知,对于钢筋拔出的试件,当锚固长度小于 9d 时,试件抗拉强度与连接钢筋抗拉强度标准值的比值 f u / f uk在 1.27~1.40 之间,大于 1.15。对于钢筋锚固长度为 9d 及以上钢筋拉断的试件,其抗拉强度与连接钢筋屈服强度标准值的比值 f u / f yk在 1.49~1.92 之间,均大于 1.25。可得出结论,即钢筋锚固长度为 9d 及以上试件满足规范[15] 中接头单拉强度性能要求。
其中极限黏结强度可由式(1)得出,残余黏结强度 τr可将残余荷载 Pr代入式(1)计算得出,其中 Pr取钢筋拔出阶段的荷载最小值。对于钢筋被拉断的试件,由于其极限黏结强度未知,故残余黏结强度无法计算。
(1)
2.2 荷载-位移关系曲线
图6为此次单向拉伸性能试验各试件的荷载-位移曲线(试件编号 A 为对中,B 为偏置),其中横轴为试验机夹头从加载到停止时的相对位移,纵轴为试验机拉力值。根据试件的破坏形式,可将图6各曲线分为钢筋快速拔出、钢筋缓慢拔出及钢筋拉断 3 种曲线形态。对于钢筋快速拔出的试件,由于钢筋在套筒内锚固长度较小,钢筋与灌浆料的机械咬合力不足,随着荷载的增大,灌浆料被钢筋月牙肋剪断失去承载力,直接被拔出。对于钢筋缓慢拔出试件,由于其锚固长度相较于钢筋快速拔出试件较大,钢筋与灌浆料之间的黏结力更大,钢筋的强化阶段较为明显,但随着荷载的增大灌浆料仍被剪碎,钢筋缓慢被拔出。对于钢筋被拉断的试件,其曲线形态与钢筋单向拉伸性能试验曲线基本一致,当钢筋超过强化阶段后被拉断。
从图6可看出,部分试件出现了双屈服平台现象,其原因为在试件的制作过程中,无法保证套筒两侧钢筋锚固长度完全一致,再加上钢筋自身材料性能也具有差异性,故随着荷载的增加一端钢筋先进入屈服阶段,另一部分钢筋再进入屈服阶段。试件的破坏模式几乎都为钢筋拔出或拉断,说明滚压螺旋肋套筒内凸肋可以显著提升钢筋的连接性能,在荷载作用下,套筒内凸肋限制了灌浆料的滑移,从而避免了灌浆料拔出破坏。当直径为 12、16 mm 钢筋的锚固长度大于 8d 时,钢筋在对中连接和偏置连接的情况下均被拉断于灌浆套筒外,符合套筒连接件的理想破坏状态。而直径为 8 mm 的钢筋在对中连接时全部发生拔出破坏,经对比观察发现,8 mm 直径的钢筋多为盘圆经机械调直处理,调直过程中钢筋横肋磨损较大,故导致其黏结性能大大降低。
图6单向拉伸试件荷载-位移曲线
Fig.6Load-displacement curve of uniaxial tensile specimen
2.3 套筒表面环向、纵向应变分布规律
2.3.1 纵向应变
钢筋对中对接试件的套筒表面粘贴了 6 组环向和纵向应变片,对于钢筋偏置对接试件,考虑到钢筋拉力对灌浆套筒的作用力不均匀,在套筒表面偏心方向处多布置了 3 组纵向应变片,具体布置位置见图2(c)。对于对中对接试件,端部应变片为 ZT1,中部应变片为 ZT2、ZT4,1 / 4 处应变片为 ZT3。对于偏置对接试件,端部应变片为 ZT1、ZT4、ZT7,中部应变片为 ZT2、 ZT5、 ZT8,1 / 4 处应变片为 ZT3、 ZT6、 ZT9。
以 10 倍钢筋直径锚固长度为例,图7为 10d 试件荷载-套筒纵向应变关系曲线。由图7可知,对中对接试件的套筒纵向应变以拉应变为主,而对于偏置对接试件的套筒纵向应变由于钢筋拉力的偏心导致同时存在拉应变和压应变。套筒中间部分的纵向应变始终为拉应变,随着荷载的增大而增大且近似呈线性关系。对于套筒 1 / 4 处的纵向应变,钢筋直径为 8 mm 的试件表现为压应变且随着荷载的增大而逐渐增大,钢筋直径为 12 mm 和 16 mm 的试件随着荷载的增大由压应变转变为拉应变。其主要原因为对于钢筋直径为 8 mm 的试件选取的套筒内径选取过大,故导致套筒对钢筋的径向约束能力较差,纵向应变未转变为拉应变试件就发生破坏。套筒端部纵向应变主要为压应变,且各单向拉伸试件纵向应变均与荷载基本呈线性相关。
图710d 试件荷载-套筒纵向应变关系曲线
Fig.7Load-sleeve longitudinal strain relationship curve of 10d test specimen
图8为套筒外部纵向应变沿套筒长度方向的分布曲线。由图8可看出:套筒中部相比两端受力较大,纵向应变为较大的拉应变,且随着拉力的增加而逐渐增加。套筒 1 / 4 和端部的纵向应变因黏结应力逐步减小,套筒端部应变接近于零。当拉力较小时,套筒表面 1 / 4 处纵向应变主要表现为压应变,其中偏置对接试件套筒因偏心受拉作用导致一侧受拉另一侧受压尤为明显,但随着拉力的增大,套筒表面 1 / 4 处转变为拉应变。
2.3.2 环向应变
同样以 10 倍钢筋直径锚固长度为例,图9为荷载-套筒环向应变关系曲线。其中,对于对中对接试件,端部环向应变片为 HT1,中部应变片为 HT2、 HT4,1 / 4 处应变片为 HT3。对于偏置对接试件,端部环向应变片为 HT1、 HT4、 HT7,中部应变片为 HT2、HT5、HT8,1 / 4 处应变片为 HT3、HT6、HT9。
由图9可看出:对于对中对接试件,套筒端部的环向应变主要表现为拉应变。其主要原因为,随着拉力增大,套筒端部灌浆料开始沿径向膨胀,套筒因此发生膨胀变形,进而产生拉应变。套筒 1 / 4 处主要表现为压应变,且随着荷载的增大近似线性增加。套筒中间处环向应变均为压应变,随着荷载的增大而不断增大。对于偏置对接试件,套筒端部环向应变均为拉应变,且随着荷载的增大而增大。套筒1 / 4 处,对于靠近钢筋一侧的环向应变随着荷载的增大且均为拉应变,中间处和远离钢筋侧的套筒环向应变均为压应变,随着荷载的增大而增大且呈线性关系。套筒中部靠近钢筋侧和中间处为压应变,远离钢筋侧为拉应变。
图10为套筒环向应变沿套筒长度方向的分布曲线。由图10可看出:对于对中对接试件,套筒表面环向应变从中部到端部逐渐衰减。套筒端部主要表现为拉应变,套筒中部及 1 / 4 处主要表现为压应变,且随着拉力的增大而增大。对于偏置对接构件,套筒表面环向应变从中部向 1 / 4 处逐渐衰减。套筒中部环向应变也为压应变且随着拉力增大而逐渐增大,套筒端部应变随着拉力的增大逐渐由拉应变转变为压应变。说明随着荷载的增大,套筒沿长度方向中间形变最大,端部最小,套筒环向发生收缩形变,故中间位置处的压应变最大,向两端逐渐衰减。
图8套筒不同位置纵向应变分布
Fig.8Longitudinal strain distribution at different positions of the sleeve
图910d 试件荷载-套筒环向应变关系曲线
Fig.9Load-sleeve circumferential strain relationship curve of 10d test specimen
图10套筒不同位置环向应变分布
Fig.10Circumferential strain distribution at different positions of the sleeve
3 结论
1)锚固长度充足时,钢筋偏置对接和对中对接对连接件都能满足抗拉连接性能。
2)滚压套筒内的内凸肋对阻止灌浆料的滑移具有显著作用,可提供足够的黏结锚固以达到连接性能要求。
3)对于钢筋偏置对接试件,当锚固长度为 9d 以上时的破坏形式均为套筒外部钢筋被拉断。
建议类宾汉流体灌浆料滚压螺旋肋套筒钢筋的最小锚固长度取为 10d,并采用偏置对接方式。