摘要
纳米颗粒对镁合金的微观组织细化及力学性能的提升具有十分重要的意义。本文采用半固态搅拌与高能超声分散的方法成功制备出纳米SiC/Mg-9Al复合材料,利用OM、XRD、SEM、TEM等设备对复合材料进行微观组织表征。结果表明:纳米SiC颗粒能够显著的细化Mg-9Al合金微观组织。当纳米颗粒添加量为1.0vol.%时,复合材料晶粒组织细化最为明显,为(71.9±28) μm,相比于基体合金晶粒尺寸减小了约63%。研究表明,纳米颗粒在镁基体中分散机制主要为沿α-Mg的晶界分布及少量的晶内分布。同时,揭示了晶粒细化机制为位于晶界的纳米颗粒能够快速吸附在生长的α-Mg晶粒表面,有效地抑制了溶质元素的扩散,显著降低了枝晶生长速率,使得熔体的成分过冷度增大,降低了结晶潜热的释放,能够激活更多的异质形核位点,从而提高了镁合金的形核率,得到了显著细化的晶粒组织。
Abstract
Nanoparticles are of great importance for the refinement of microstructure and improvement of the mechanical properties of magnesium alloys. In this paper, nano-SiC/Mg-9Al composites were successfully prepared by semi-solid stirring and high-energy ultrasonic dispersion method, and the microstructure was characterized by OM, XRD, SEM and TEM. The results show that the nano-SiC particles can significantly refine the microstructure of Mg-9Al alloy.When nanoparticles are added at 1.0vol.%, the most significant refinement of the composite grain structure is (71.9 ± 28) μm, which is about 63% reduction in grain size compared to the matrix alloy. Moreover, the dispersion mechanism of nanoparticles in the magnesium matrix is mainly along the grain boundary distribution of α-Mg with a small amount of intracrystalline distribution. At the same time, it is revealed that the grain refinement mechanism involves the rapid adsorption of nanoparticles located at the grain boundarieson the surface of the growing α-Mg grains, which effectively inhibits the diffusion of solute elements and significantly reduces the growth rate of dendrites. This leads to an increase in the composition subcooling of the melt, reducing the release of latent heat of crystallisation. As a result, more heterogeneous nucleation sites are activated, which increases the nucleation rate of the magnesium alloy and obtains significant grain refinement.
Keywords
镁合金具有高比强度、比刚度、优良的铸造性能和电磁屏蔽性能等优点。它们是继钢和铝合金之后发展起来的第三类金属结构材料,被称为“21世纪绿色工程材料”[1-2]。Mg-Al合金因其优异的成形性,良好的铸造性能及力学性能而成为目前镁合金领域应用最为广泛的系列合金之一。铸造是Mg-Al系合金针对复杂材料和部件的大规模生产的主要成形方法[3]。然而,Mg-Al合金在铸造过程中容易产生粗大的、不规则的树状晶,严重影响了铸件的力学性能及使用寿命。因此,如何控制镁合金凝固过程中产生的粗大枝晶,使其获得细小均匀的等轴晶是目前镁合金领域的研究重点[4-5]。
目前,已开发了几种常用的铸态镁合金晶粒细化的方法,如添加合金元素[6]、碳改性[7]、超声振动搅拌熔体[8]、增加冷却速率[9]和添加纳米颗粒(NPs)[10-11]。其中,添加纳米SiC颗粒到镁合金熔体中,不仅能够显著减小合金的晶粒尺寸,而且通过颗粒硬化机制提高了镁基体的力学性能。近些年,有学者研究了添加纳米SiC颗粒的镁合金的凝固行为,并揭示了晶粒细化的一些细节。Nie等[12]成功将0.5vol.% SiC 纳米颗粒加入到AZ91合金中,研究发现加入的纳米颗粒能够沿晶界均匀分布,AZ91合金的平均晶粒尺寸从170 μm降至80 μm,起到了显著细化晶粒的效果。Guo等[11]首次通过3D同步辐射直接观察到,添加NPs后,α-Mg枝晶显著细化,原位同步辐射揭示了其细化机制主要为加入的纳米颗粒能够有效的吸附在生长的晶粒周围,极大的限制了溶质元素的扩散,从而起到了细化晶粒的作用。此外,Li等[13]通过陶瓷纳米颗粒(NPs)诱导生长控制实现了AZ91合金的晶粒显著细化,添加2.0vol.%复合材料晶粒尺寸约为36 μm,相比于基体合金细化66%。因此,添加纳米颗粒在镁合金中,能够实现显著的晶粒细化效果。
针对纳米颗粒可显著细化镁合金的晶粒尺寸的现状,系统阐述纳米颗粒诱导镁合金晶粒细化机制尤为重要。因此,本文选取较为简单的Mg-9Al二元合金结构,采用半固态搅拌及高能超声分散方法,将纳米SiC分散到Mg-9Al合金中,系统研究SiC纳米颗粒对Mg-9Al复合材料微观组织结构的影响及纳米颗粒在基体中的分布形态,并阐述纳米颗粒诱导基体合金晶粒细化机理。
1 实验
1.1 复合材料制备过程
Mg-9Al合金是将商业纯镁(>99.95wt.%)和纯铝(>99.95wt.%)放入低碳钢坩埚中,加热到720℃熔化而制备的。熔炼全程通入CO2/SF6(体积比为40∶1)的气体进行保护,从而为了避免合金氧化。待合金熔化后,均匀化5 min,熔体从720℃冷却至580℃(略低于理论液相线温度588℃)。将铝箔包裹的SiC纳米颗粒加入半固态熔体中,采用不锈钢桨机械搅拌10 min增强纳米颗粒的分散。SiC纳米颗粒的体积分数选定为0.5%、1.0% 和1.5%。搅拌完成后,将合金熔体加热至约700℃,将高能超声装置(20 kHz,2 kW)浸入熔体中约20 mm,进行15 min的高能超声以增强NPs在合金熔体中的均匀分散。超声处理后,将熔液加热至720℃,并倒入预热温度为350℃的圆柱形永久模具(Φ30 mm×100 mm,壁厚10 mm)中。为了进行对比,未进行半固态搅拌与超声处理的情况下,制备了未添加纳米SiC颗粒的Mg-9Al合金。
1.2 微观组织测试
使用电压为40 kV、电流为40 mA的X′Pert PRO型X射线衍射仪(XRD)来鉴定物相,步长为0.02°。通过Quanta200和 Apreo C型扫描电子显微镜(SEM)和能量色散光谱(EDS)对微观组织结构和纳米颗粒分散情况进行分析。使用JEM-2100型透射电子显微镜(TEM)进一步确定陶瓷纳米颗粒(NPs)在熔体内部的分布情况。
2 结果与讨论
2.1 纳米SiC颗粒对Mg-9Al合金微观组织演变的影响
图1为SiC/Mg-9Al复合材料的XRD衍射峰谱图。
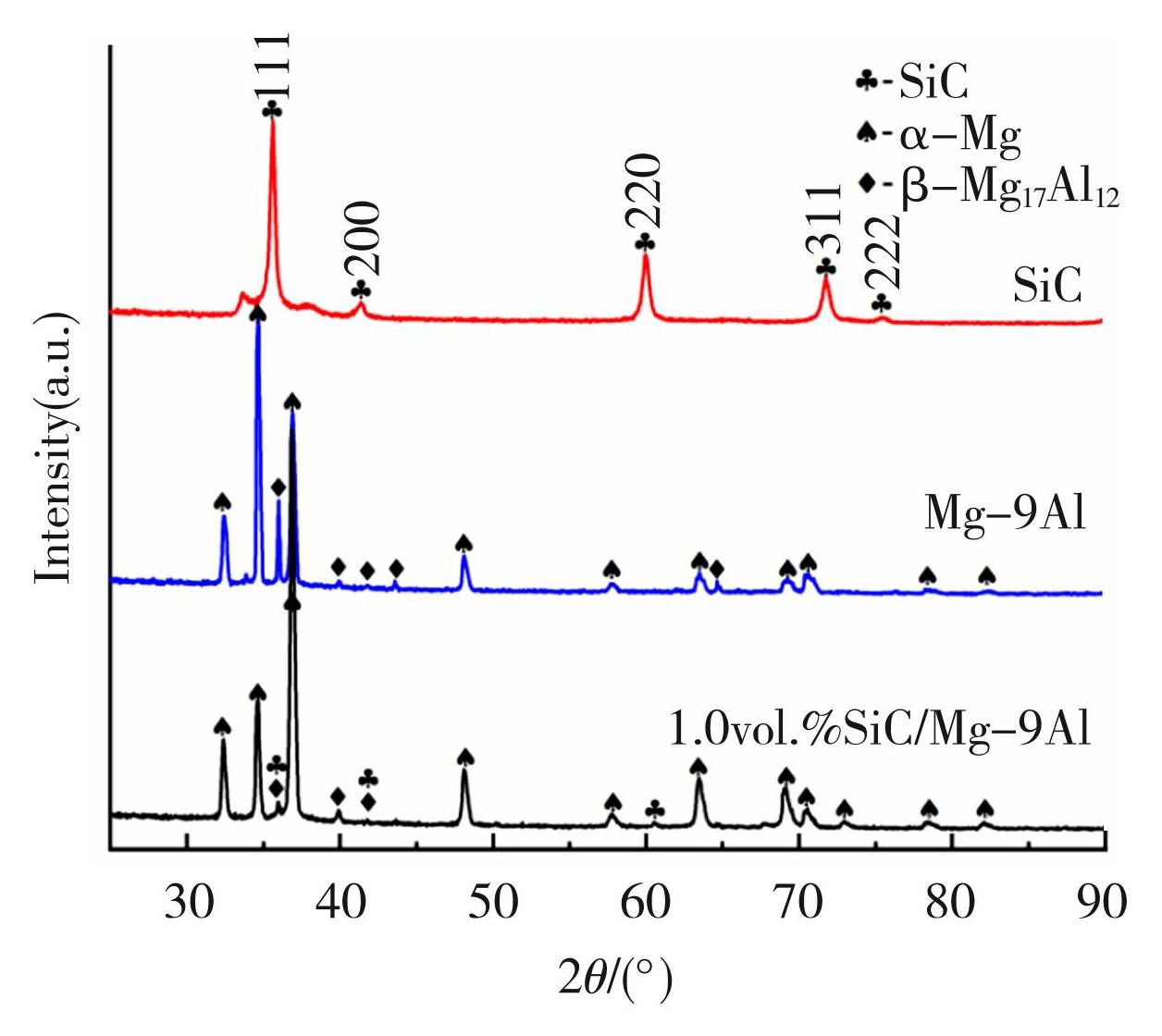
图1SiC、Mg-9Al、1.0vol.%SiC/Mg-9Al复合材料的XRD谱图
Fig.1XRD patterns of SiC, Mg-9Al and 1.0vol.%SiC/Mg-9Al composites
由图1可知,纳米SiC颗粒有5个较强的衍射峰,分别对应于35.5°、41.4°、59.9°、71.5°和75.3°的(111)、(200)、(220)、(311)和(222)面;Mg-9Al基体合金中只存在基体α-Mg和共晶相β-Mg17Al12;通过Jade软件对比1.0vol.%SiC/Mg-9Al复合材料衍射峰发现,除了Mg-9Al合金衍射峰外,还可以看到SiC(111)、(200)和(220)面的衍射峰。由于纳米SiC颗粒添加含量较低,复合材料中纳米SiC颗粒衍射峰强度低于纳米SiC颗粒粉末衍射峰。
图2为不同纳米SiC颗粒添加量下SiC/Mg-9Al复合材料偏振光晶粒组织图。未添加纳米SiC颗粒的基体合金具有较为粗大的枝晶形貌,如图2(a)所示。随着纳米SiC颗粒添加,晶粒尺寸逐渐减小,当纳米SiC颗粒添加量为1.0vol.%时,晶粒尺寸最为细小,呈现等轴晶形貌,如图2(c)所示。但当纳米SiC颗粒添加量为1.5vol.%时,晶粒尺寸相较于添加量为1.0vol.%时变大。
图2不同纳米SiC添加量Mg-9Al复合材料晶粒组织图:(a)基体合金;(b)0.5vol.%;(c)1.0vol.%;(d)1.5vol.%
Fig.2OM micrographs of Mg-9Al composites with different SiC nanoparticles added: (a) matrix alloy; (b) 0.5vol.%; (c) 1.0vol.%; (d) 1.5vol.%
图3为不同纳米SiC颗粒体积分数添加量下Mg-9Al复合材料晶粒尺寸变化曲线。可明显的发现随着纳米SiC颗粒添加量的增多,晶粒尺寸明显细化,当纳米SiC颗粒添加量为1.0vol.%时,晶粒尺寸最为细小,为71.9 μm,相比于未添加纳米SiC颗粒的基体合金,减小了约63%。当纳米SiC颗粒添加量为1.5vol.%时,晶粒尺寸为100.4 μm,晶粒尺寸略有增加,但相比于基体合金晶粒尺寸仍减小了49%,这主要因为当纳米SiC颗粒添加量较多时,由于纳米颗粒具有较大的表面能,颗粒之间产生较强的范德华力,导致颗粒容易发生团聚,造成了镁合金晶粒细化效果的减弱。
根据已有研究,半固态搅拌和超声处理确实有晶粒细化效果,例如薛寒松等[14]在半固态温度区间内进行搅拌,并迅速凝固,从而起到显著的晶粒细化效果。对于超声处理,Balasubramani等[15]是将高能超声棒持续处在半固态区间内,打碎α-Mg枝晶,高能超声棒跟随金属熔体冷却凝固,从而起到显著的晶粒细化效果。但本文浇铸温度在720℃,远高于液相线温度,其二者在液相线温度以上对合金细化效果减弱。因此,通过复合材料晶粒尺寸曲线图可以证明,纳米SiC颗粒对合金晶粒细化起到关键性作用,与文献[12]得出的纳米SiC颗粒能够细化AZ91D晶粒组织现象保持一致。后续将在2.3小节详细阐述纳米SiC颗粒诱导镁合金晶粒细化机理。
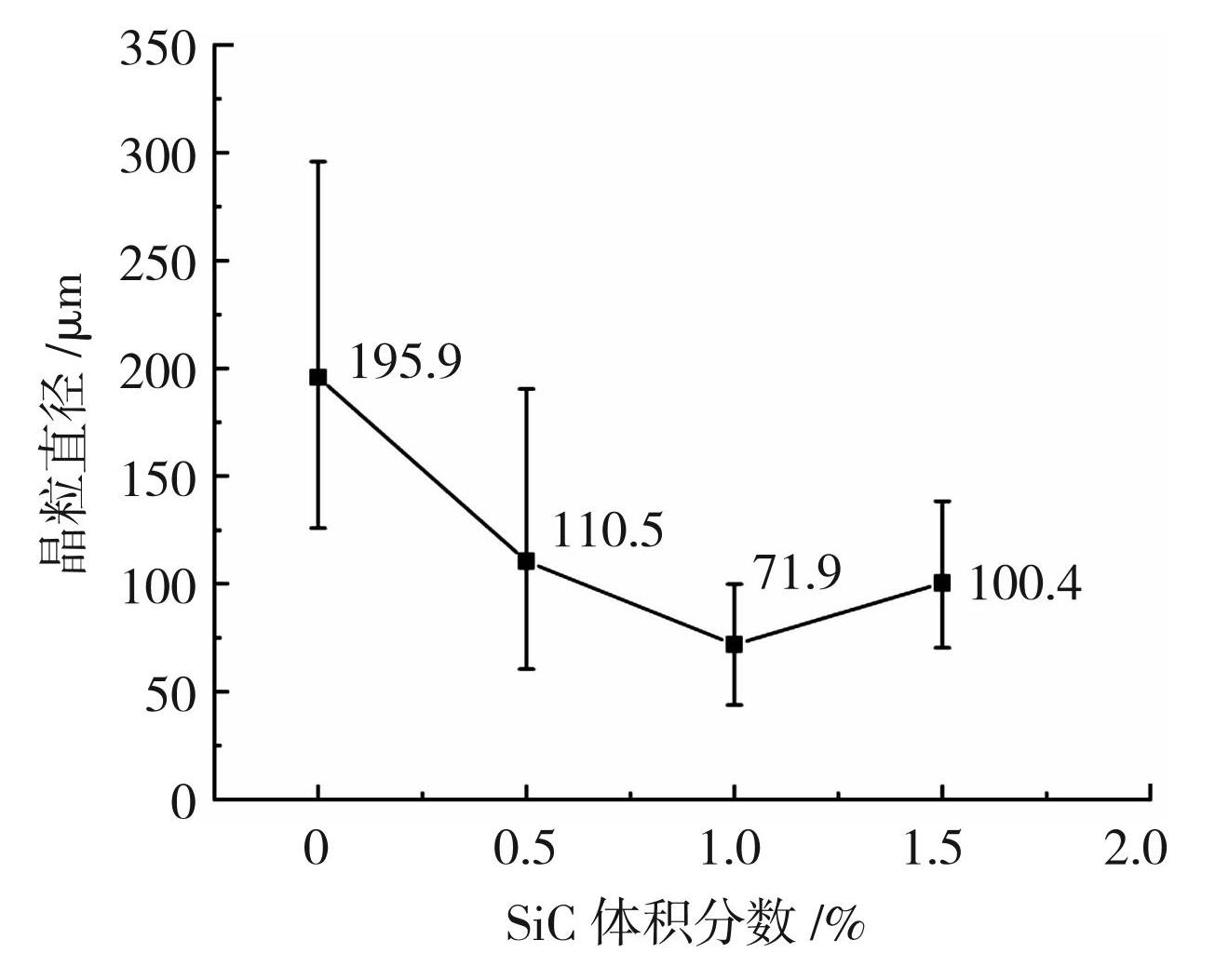
图3不同纳米SiC颗粒添加量Mg-9Al复合材料晶粒尺寸变化曲线
Fig.3Grain size change curve of Mg-9Al composites with different SiC nanoparticles added
图4为不同纳米SiC颗粒体积分数添加量下Mg-9Al复合材料SEM图。如图4(a)所示,未添加纳米SiC颗粒的Mg-9Al合金主要由具有连续网状结构和块状结构的共晶组织β-Mg17Al12和α-Mg基体组成。随着纳米SiC颗粒的添加,部分纳米SiC颗粒附着在β-Mg17Al12相及晶界的周围,基体中β-Mg17Al12相从连续网状结构转变为间断网状结构,β-Mg17Al12相具有明显的尺寸减小的现象,如图4(b)和图4(c)所示。在图4(d)中,发现纳米SiC颗粒具有明显的团聚现象,并伴随着部分颗粒的脱落。该现象证实了上一部分晶粒粗化的猜想,正是由于颗粒在晶界处附近发生大量的团聚,导致颗粒与界面结合力减弱,导致了脱落、缩孔和团聚等现象[16]。
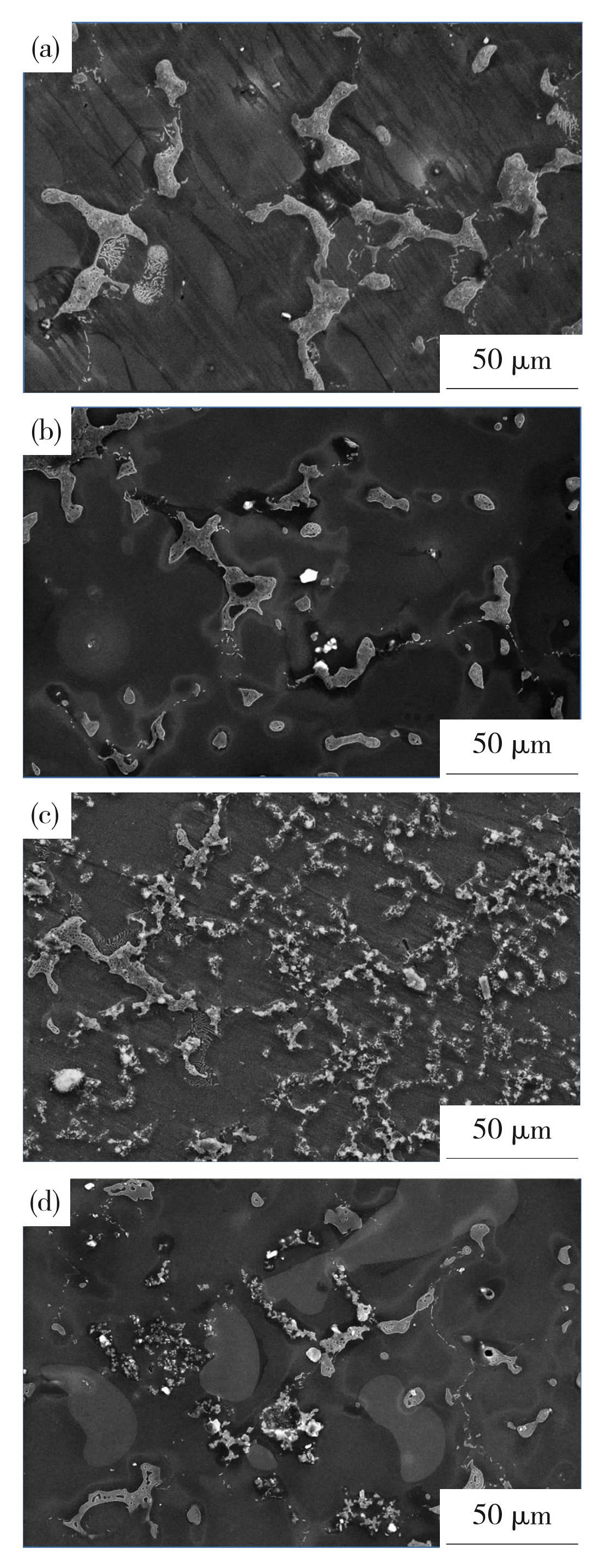
图4不同纳米SiC颗粒添加量Mg-9Al复合材料SEM图:(a)基体合金;(b)0.5vol.%;(c)1.0vol.%;(d)1.5vol.%
Fig.4SEM images of Mg-9Al composite with different SiC nanoparticles added: (a) matrix alloy; (b) 0.5vol.%; (c) 1.0vol.%; (d) 1.5vol.%
2.2 纳米SiC颗粒在Mg-9Al合金中分布形态
图5为1.0vol.%SiC/Mg-9Al复合材料的SEM和EDS图。通过EDS能谱可知,颜色的深浅作为相的组成、相的分布、颗粒的组成与颗粒的分布依据。较高浓度的Al元素分布在晶界附近,如图5(c)所示,并依据Mg-Al合金二元相图可知,晶界处的为共晶组织β-Mg17Al12相。
图51.0vol.% SiC/Mg-9Al 复合材料SEM(a),以及Mg(b)、Al(c)、Si(d)、C(e)元素面扫描分析
Fig.5(a) SEM analysis of 1.0vol.% SiC/Mg-9Al composites, surface scanning analysis of (b) Mg, (c) Al, (d) Si and (e) C elements
图5(d)中可明显观察到大量的Si元素分布位置与Al元素分布位置大致相同,其可证明大部分纳米SiC颗粒分散在β-Mg17Al12相附近,少量的Si元素存在晶粒内部。由于β-Mg17Al12相存在于晶界处,即可间接证明NPs分布在晶界附近和β-Mg17Al12相上。复合材料EDS能谱可证明纳米SiC颗粒存在于Mg-9Al合金中,与XRD分析结果一致。从而得出NPs主要表现为两种分布类型,即晶内分布(在α-Mg晶粒内部)和晶间分布(沿晶界或晶界上的共晶相)。
图6为1.0vol.%SiC/Mg-9Al复合材料高倍SEM显微组织图。由图6(a)可知,在共晶相上依附着大量的球状纳米SiC颗粒,并在共晶相周围和晶界附近存在少量NPs。对图6(a)黄色区域进行放大,对其颗粒的尺寸进行测量,最小颗粒尺寸接近50 nm,最大颗粒尺寸约为100 nm。可以发现存在多处纳米SiC颗粒团聚现象,但其团聚尺寸为纳米级别。可以说明,随着合金凝固进行,纳米SiC颗粒被α-Mg枝晶推到固液界面前沿,当冷却到共晶相温度时,纳米SiC颗粒依附在β-Mg17Al12相上,随着共晶相的生长,部分纳米SiC颗粒存在于共晶相的内部,部分纳米SiC颗粒停留在晶界附近。该现象证明了随着纳米SiC颗粒添加量的增多,β-Mg17Al12相尺寸在逐渐减小,起到抑制共晶相生长的效果。
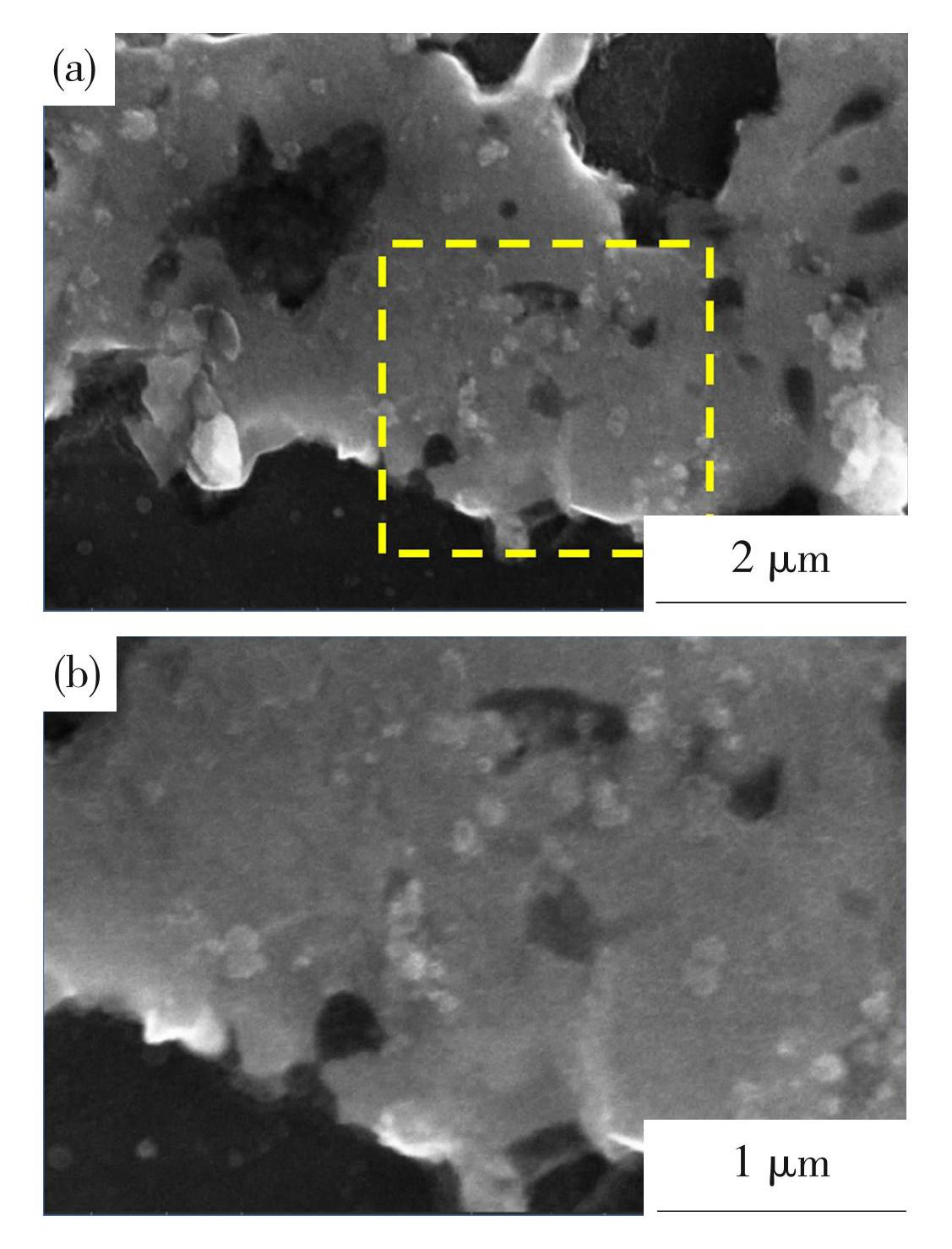
图61.0vol.% SiC/Mg-9Al 复合材料高倍SEM(a)以及图6(a)黄色区域放大图(b)
Fig.61.0vol.% SiC/Mg-9Al composite high magnification SEM (a) and fig.6 (a) yellow area magnification (b)
图7为1.0vol.%SiC/Mg-9Al复合材料HRTEM显微组织图。图7(a)表明,大量的纳米级的颗粒附着在β-Mg17Al12相上,且分散较为均匀。再一次证明当纳米SiC颗粒被推到固液界面前沿后,随着共晶相生长,将纳米SiC颗粒包裹在共晶相内部,起到细化共晶相的效果。对图7(a)黄色区域进行放大,进行选区电子衍射(SAED)图谱分析,得到纳米SiC颗粒衍射环,并进行标定,可证明黑色颗粒为SiC纳米颗粒。通过对HRTEM分析可得到,纳米SiC颗粒在共晶相内部为均匀分散的效果,并且在晶界附近形成多层的纳米颗粒保护层。当形核发生时,多层的纳米颗粒保护层结构则会减小形核产生的溶质排放,溶质排放减弱,根据溶质抑制形核理论[17],溶质的富集会抑制晶粒的生长,形核所产生的的潜热减弱,促进周围未形核颗粒成为有效核心,使Mg-9Al合金产生一定的晶粒细化效果。
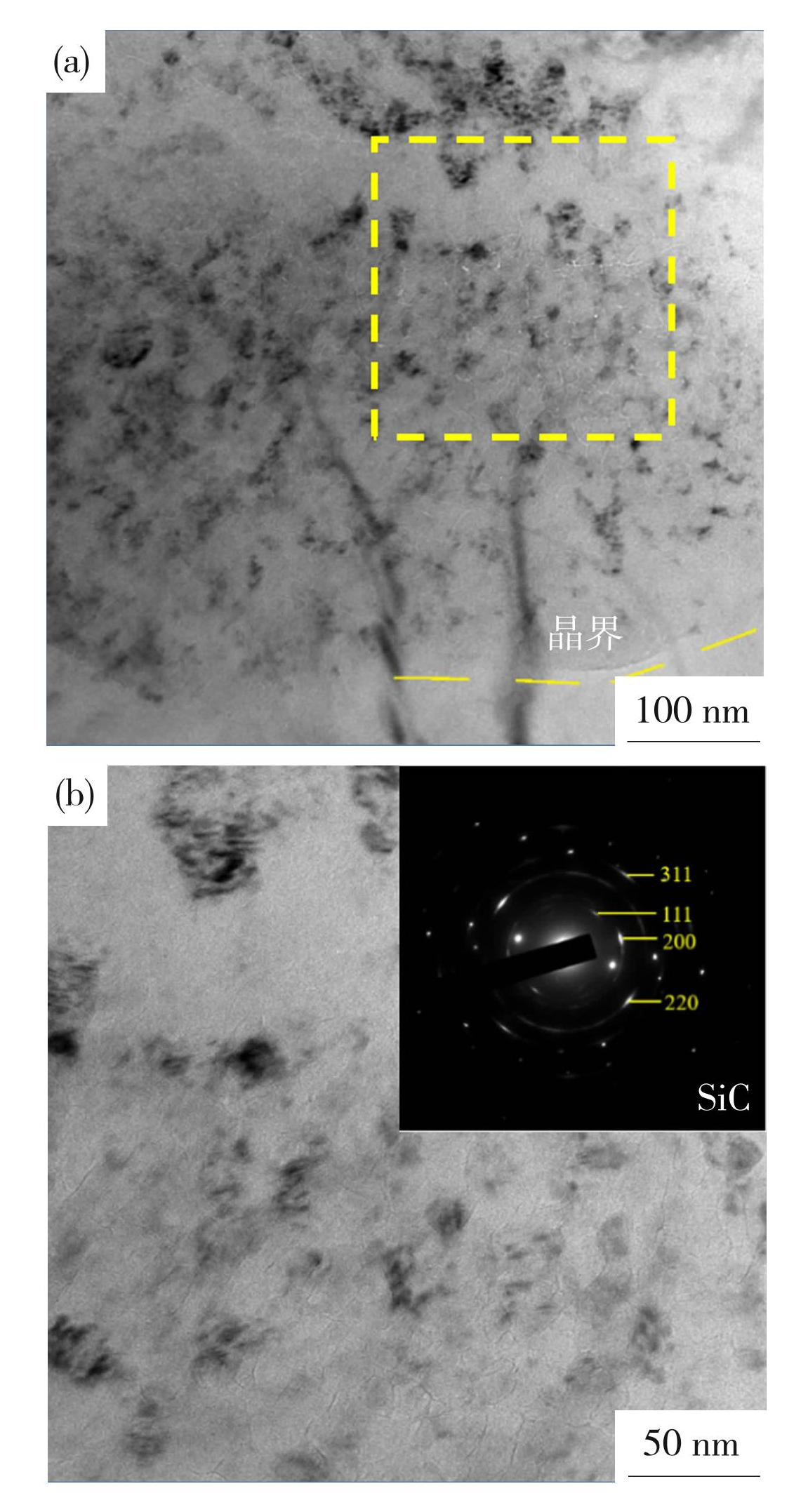
图71.0vol.% SiC/Mg-9Al 复合材料HRTEM(a)以及图7(a)黄色区域放大图及SAED(b)
Fig.71.0vol.% SiC/Mg-9Al composite HRTEM (a) and fig.7 (a) yellow area enlargement and SAED (b)
2.3 纳米颗粒对Mg-9Al合金晶粒细化机理
目前,对于纳米SiC颗粒细化机理,主要存在3种细化机理理论:1)异质形核理论[18]:当纳米SiC颗粒在凝固过程中被固液界面捕获,则停留在基体内部,若纳米SiC颗粒与基体界面之间有着良好的错配度关系,则纳米SiC颗粒会成为形核质点,促进合金形核,达到晶粒细化的效果;2)纳米SiC颗粒钉扎理论[10]:当纳米SiC颗粒停留在固液界面前沿钉扎,则会造成较大的曲率过冷,抑制晶粒的生长,产生合金细化的效果;3)溶质扩散抑制理论[11]:当纳米SiC颗粒停留在固液界面前沿,抑制的α-Mg枝晶周围溶质扩散,根据溶质抑制生长理论[17],则会减小枝晶的生长速率,潜热释放减弱,促进其他周围晶粒有效形核,达到晶粒细化效果。根据SEM、TEM结果,抑制溶质扩散理论在本文中占主导地位。图8给出了纳米颗粒抑制晶粒生长机制示意图。图8(a)~(c)为未添加纳米SiC颗粒的Mg-9Al合金凝固过程。随着凝固的进行,熔体中的过冷度达到临界形核所需过冷度且该位置恰好具有形核质点,α-Mg开始形核,并在液相中长大。
图8(d)~(f)为添加纳米SiC颗粒的Mg-9Al合金凝固过程。随着凝固的进行,纳米SiC颗粒成功分散并且游离在熔体内部,熔体中的过冷度达到形核所需临界过冷度且恰好存在形核质点,α-Mg开始形核,纳米SiC颗粒开始依附在α-Mg枝晶周围,随着枝晶的生长,固液界面排斥纳米SiC颗粒,枝晶推动着纳米SiC颗粒,并在枝晶周围形成一层或多层包覆层,减少溶质扩散,导致枝晶生长速率的减慢,成分过冷增大,潜热释放降低,溶质扩散程度减弱,使熔体更容易达到形核过冷,促进形核的产生,从而达到晶粒细化的效果。
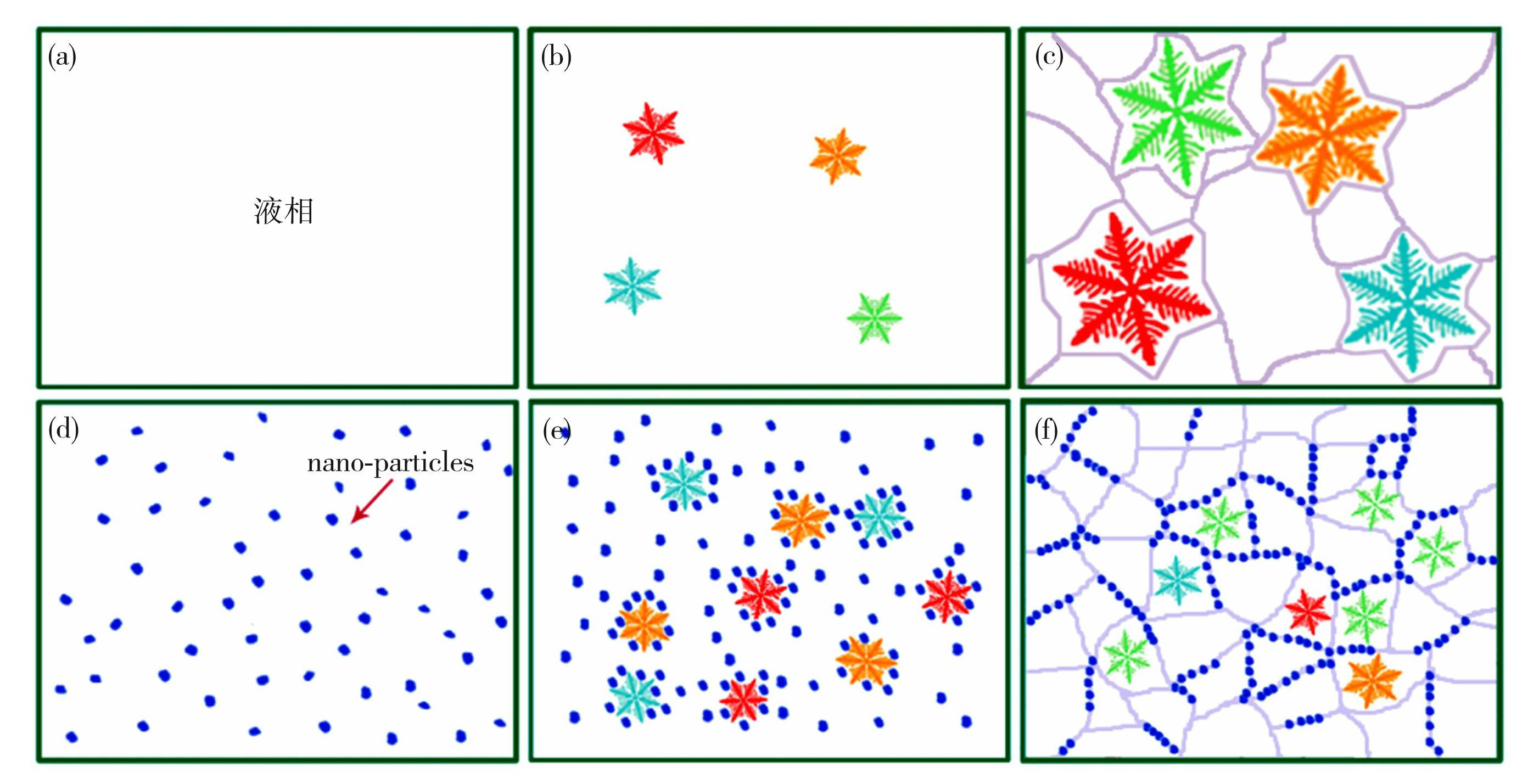
图8纳米SiC颗粒抑制晶粒生长机制示意图:(a)~(c)未添加纳米SiC颗粒;(d)~(f)添加纳米SiC颗粒
Fig.8Schematic diagram of the mechanism of nanoparticles inhibiting grain growth: (a) ~ (c) without adding nano-SiC particles; (d) ~ (f) adding nano-SiC particles
3 结论
1)采用半固态搅拌与高能超声分散方法成功将纳米SiC颗粒添加到Mg-9Al合金中,纳米颗粒并未与基体合金发生反应。当纳米SiC颗粒添加量为1.0vol.%时,复合材料晶粒组织细化最为明显,相比于基体合金晶粒尺寸减小了约63%。
2)纳米SiC颗粒在合金中的分散主要存在3种形式:少量的纳米SiC颗粒存在于晶粒内部,部分颗粒存在于晶界附近,其余部分存在于共晶相中。
3)纳米SiC颗粒诱导Mg-9Al合金晶粒细化机理为:纳米SiC颗粒在晶界周围形成多层纳米颗粒包覆层,减弱溶质扩散的排放,导致枝晶生长速率的减慢,成分过冷增大,潜热释放降低,使熔体更容易达到形核过冷,促进形核的产生,达到晶粒细化的效果。