摘要
探究温度对镍基合金Hastelloy C-276渗层显微组织、力学性能、摩擦磨损性能以及耐蚀性能的影响规律,以期获得硬度、耐磨性和耐蚀性优良的表面改性层。使用等离子碳氮共渗技术在不同温度(395、425、455、485 ℃)下制备表面改性层,镍基合金C-276经离子碳氮共渗后,渗层厚度从6.5到20.0 μm不等,表面硬度较原始合金均有不同程度提高。当处理温度≤395 ℃时生成的S相层较薄;随着处理温度升高,生成较厚的S相层和CrN硬质相,获得优良的耐磨性;进一步提升处理温度至485 ℃时,基体表面出现贫Cr,致使合金耐蚀性降低;当处理温度<450 ℃时样品表现出比基体更好的耐蚀性能。镍基合金Hastelloy C-276在425、455 ℃温度下进行碳氮共渗,可获得硬度、耐磨性和耐蚀性相对优良的表面改性层。
关键词
Abstract
In order to obtain a surface modified layer with excellent hardness, wear resistance and corrosion resistance, the influence of temperature on the microstructure, mechanical properties, tribological properties, and corrosion resistance of the ion carbonitriding coating on Hastelloy C-276 nickel base alloy was investigated.The surface modified layer was prepared by plasma carbonitriding technology at different temperatures (395, 425, 455, 485 ℃). After ion carbonitriding treatment, the thickness of the ion carbonitriding coatings ranged from 6.5 to 20.0 μm, and the surface hardness was higher than that of the original alloy. When the temperature was ≤395 ℃, the S-phase layer generated was relatively thin. As the processing temperature increased, a mixture layer of thicker S phase and CrN phase were formed, leading to excellent wear resistance. However, with further increase in the treatment temperature to 485 ℃, the poor Cr phenomenon in the matrix occurred on the alloy surface, reducing its corrosion resistance. The samples treated below 450 ℃ showed better corrosion resistance than that of the substrate.The Hastelloy C-276 nickel-base alloy carbonitrided at 425 ℃ and 455 ℃ showed superior surface-modified layers in terms of excellent hardness, wear resistance and corrosion resistance.
Keywords
镍基耐蚀合金具有优异的耐蚀性和热稳定性,兼有高强度、高塑韧性等力学性能及可冶炼、铸造、冷/热变形、焊接和压力加工等成形性能,广泛应用于化学加工、湿法冶金、海洋工程、核燃料化工后处理、核能、油和天然气开采,污染控制点烟气脱硫装置等工业领域[1-2]。然而,在外加机械载荷下,镍基合金会发生严重磨损,极易导致高温下的磨损失效[3]。例如,镍基合金制造的耐蚀管道、泵、阀等器件,液体在其间的高速流动会引起振动,当振动强度过大时,会导致器件连接处发生磨损进而引起器件失效[4]。为改善镍基合金表面耐磨损性能,近年来,许多学者基于离子渗氮工艺在不锈钢表面改性中获得良好应用效果[5-8],积极探索离子渗氮在镍基合金表面的应用。Semenov等[9]研究了镍合金40KhNYu-VI在辉光放电渗氮后的显微组织和耐磨性,结果表明,氮化过程中形成的连续氮化铬层大大提高了零件表面的耐磨性,渗氮后的耐磨损性能提高了5~8倍。在Kumar等[10]的研究中也得到了类似的结果。Huang等[11]研究了Incoloy 901氮化层的生长动力学,发现随着温度的升高,氮化层的厚度显著增加,表面硬度得到极大提高。然而,和钢铁材料相比,传统的渗氮工艺应用于镍基合金时,所获得的渗层厚度较薄,因此,许多研究人员改进了镍基合金渗氮工艺,发展出如三极离子渗氮[12]、纳米共沉积法[13]、超声波纳米表面改性[14]、增材制造[15-16]等工艺。Espallargas等[17]研究了Ni-Cr合金离子渗氮处理后的干磨损和腐蚀磨损行为,干摩擦时,发现未经处理的合金比经离子渗氮处理的合金磨损严重得多;在0.5 mol/L H2SO4中,使用氧化铝摩擦副施加15 N载荷进行了磨损腐蚀测试,发现由于水的润滑作用,磨损率较低。其它研究也表明,在500℃以下,经渗氮后的镍基合金在NaCl溶液中耐蚀性得到了提高[14,18]。
尽管镍基合金的离子渗氮技术已经取得一定的进展,但渗氮所用温度过高容易导致镍基合金耐蚀性下降,因此后续又开发了低温渗氮技术,即在镍基合金表层生成膨胀奥氏体组织(即S相),这样可以在不降低合金耐蚀性的前提下大幅提升合金表面硬度和耐磨性。然而,研究发现,在不生成氮化物的情况下,离子氮化所获得的硬化层厚度很难超过10 μm。采用低温离子碳氮共渗同样可以获得S相,且渗层厚度比低温离子渗氮提升50%以上。目前,对于镍基合金离子碳氮共渗还未有详细的研究,渗层的耐磨损和耐腐性性能也未见报道。因此,本文以镍基耐蚀合金Hastelloy C-276为研究对象,通过离子碳氮共渗技术制备具有高硬度、良好的耐磨性和耐蚀性的表层组织。对经过碳氮共渗后的试样进行显微组织、力学性能、摩擦学性能的分析,确定不同工艺条件对渗层组织及性能的影响规律。
1 实验
1.1 渗层制备
实验材料选用上海墨钜特殊钢有限公司生产的镍基合金Hastelloy C-276(以下简称C-276)棒材,采用ARL3460火花直读光谱仪对C-276的元素进行分析测定,测量3次,读取平均值,测定结果如表1所示。使用线切割将C-276棒材切割成10 mm×10 mm×10 mm的正方体试样,然后依次用240#、400#、600#、1 000#、1 500#、2 000#水磨砂纸将试样各表面磨平,再分别用1和0.5 μm的金刚石抛光膏进行抛光,随后用丙酮和去离子水在超声波清洗机中清洗后吹干备用。采用LDMC-30F触屏式脉冲控制型辉光离子渗扩炉进行碳氮共渗,调节炉压控制在300~350 Pa,脉冲电压650 V,电流20 A,分别先后通入C2H2与N2、H2,体积比为N2∶H2=1∶3,工艺参数如表2所示。
表1Hastelloy C-276的化学成分(质量分数/%)
Table1Chemical composition of Hastelloy C-276 (wt.%)

表2离子碳氮共渗时间与温度参数
Table2Time and temperature parameters of ion carbonitriding
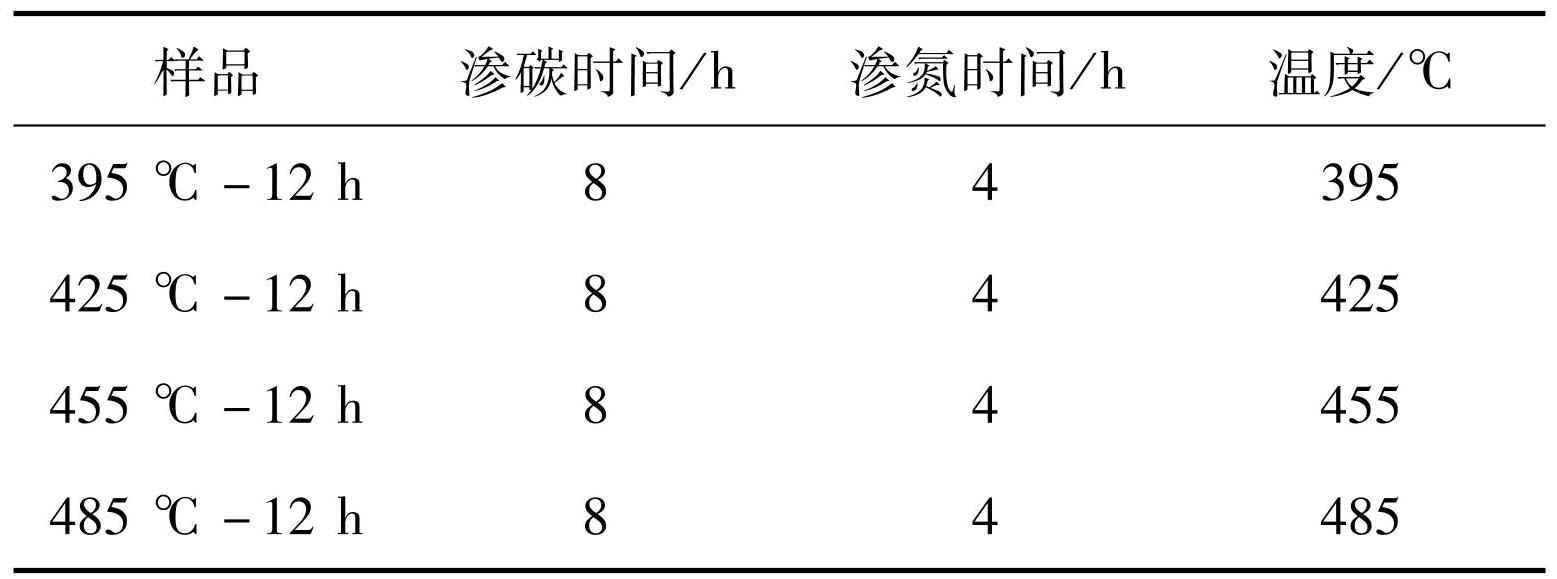
1.2 表征方法
对完成碳氮共渗的C-276试样进行镶样研磨和抛光处理,采用HCl(15 mL)+ HNO3(5 mL)腐蚀样品,腐蚀时间为 30 s,再用酒精超声清洗吹干。采用智能全自动Axio Image型蔡司(ZEISS)金相显微镜观察碳氮共渗样品截面金相组织形貌;采用DX-2700型X射线衍射仪对镍基合金C-276基体和碳氮共渗试样分别进行物相分析,选用Cu靶,管电压40 kV,电流30 mA,扫描范围为30°~100°,扫描步长为0.03°;采用ZEISS公司生产的Zeiss Sigma300型扫描电子显微镜对试样表面的微观形貌进行观察;采用MVC-1000JMT1型显微硬度计检测试样的表面硬度和截面硬度;采用CHI600E 型电化学工作站进行检测分析,在测试表面暴露出10 mm×10 mm工作区域,选择3.5wt.%NaCl溶液作为腐蚀介质,工作温度为室温。使用MS-M9000型多功能摩擦试验仪对样品进行摩擦学性能检测,选用直径为5 mm的Al2O3陶瓷球,频率为2 Hz,摩擦时间为30 min,摩擦长度为5 mm,摩擦方式为往复式干摩擦。
2 结果与分析
2.1 金相组织
图1为镍基合金C-276在395、425、455、485℃下离子碳氮共渗12 h后各试样用王水试剂腐蚀后的截面金相照片。从图1中可以看出,395℃-12 h、425℃-12 h、455℃-12 h试样在经离子碳氮共渗后形成了明显的白亮色渗层,可以与基体清楚区分,而基体部分已被腐蚀出明显的晶界,表明渗层具有比基体更好的耐蚀性,485℃-12 h渗层呈现深色和浅色双层结构,这表明随着处理温度升高部分S相分解,CrN在试样表面析出,同时观察到455℃-12 h试样也有少量析出,说明该样品的耐蚀性也出现降低。试样395℃-12 h、425℃-12 h的渗层厚度分别为6.45、9.93 μm;试样455℃-12 h、485℃-12 h渗层由析出层和S相层组成,试样455℃-12 h析出层厚度为3.19 μm,渗层总厚度为14.03 μm;试样485℃-12 h析出层厚度为8.69 μm,渗层总厚度为20.02 μm。当碳氮共渗处理时间一致时,渗层厚度随着处理温度升高而增加。
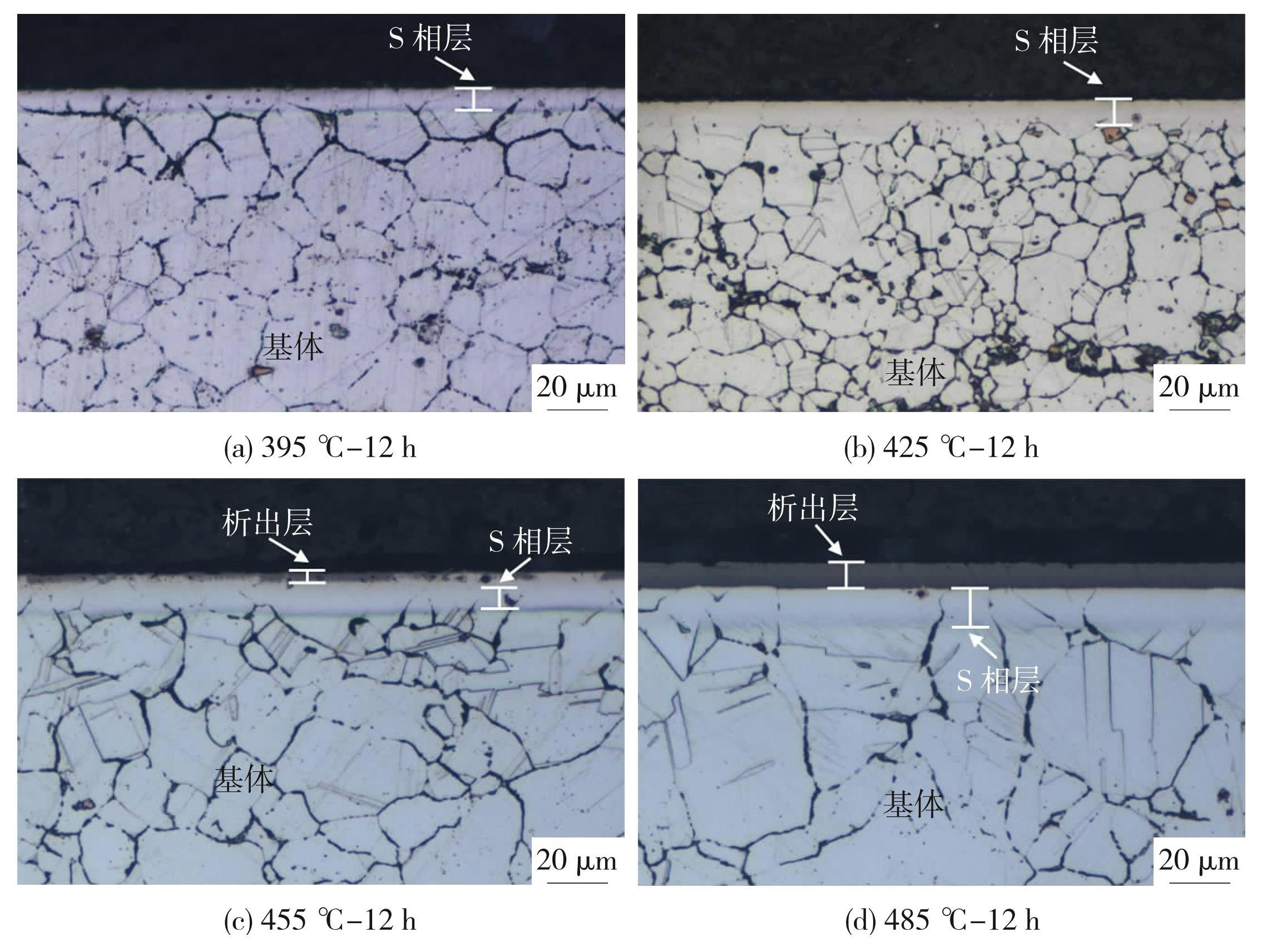
图1不同处理温度共渗层金相组织截面形貌
Fig.1Metallographic cross section morphology of the interpenetrating layer at different treatment temperatures: (a) 395℃-12 h; (b) 425℃-12 h; (c) 455℃-12 h; (d) 485℃-12 h
2.2 相组成分析
图2为镍基合金C-276基体和不同温度碳氮共渗处理试样的X射线衍射谱图,从XRD谱图可以看出,不同温度碳氮共渗处理的镍基合金C-276奥氏体基体衍射峰向低角度偏移(0.56°~2.04°),根据布拉格方程2dsinθ=nλ可知,由于N、C原子进入奥氏体产生晶格膨胀使得晶面间距增大,故衍射角减小,且衍射偏移程度随着温度升高而降低,这表明4种不同温度处理后的C-276试样上都形成了含氮和碳的膨胀奥氏体组织。而当处理温度升高时,在455和485℃处理的试样中观察到CrN的衍射峰,经标定分别为CrN的(111)和(220)面,表明在较高温度下处理的C-276试样,其表层S相发生了分解。相关研究指出[19-20],当碳氮共渗温度大于450℃时,CrN会在碳氮共渗过程中析出。
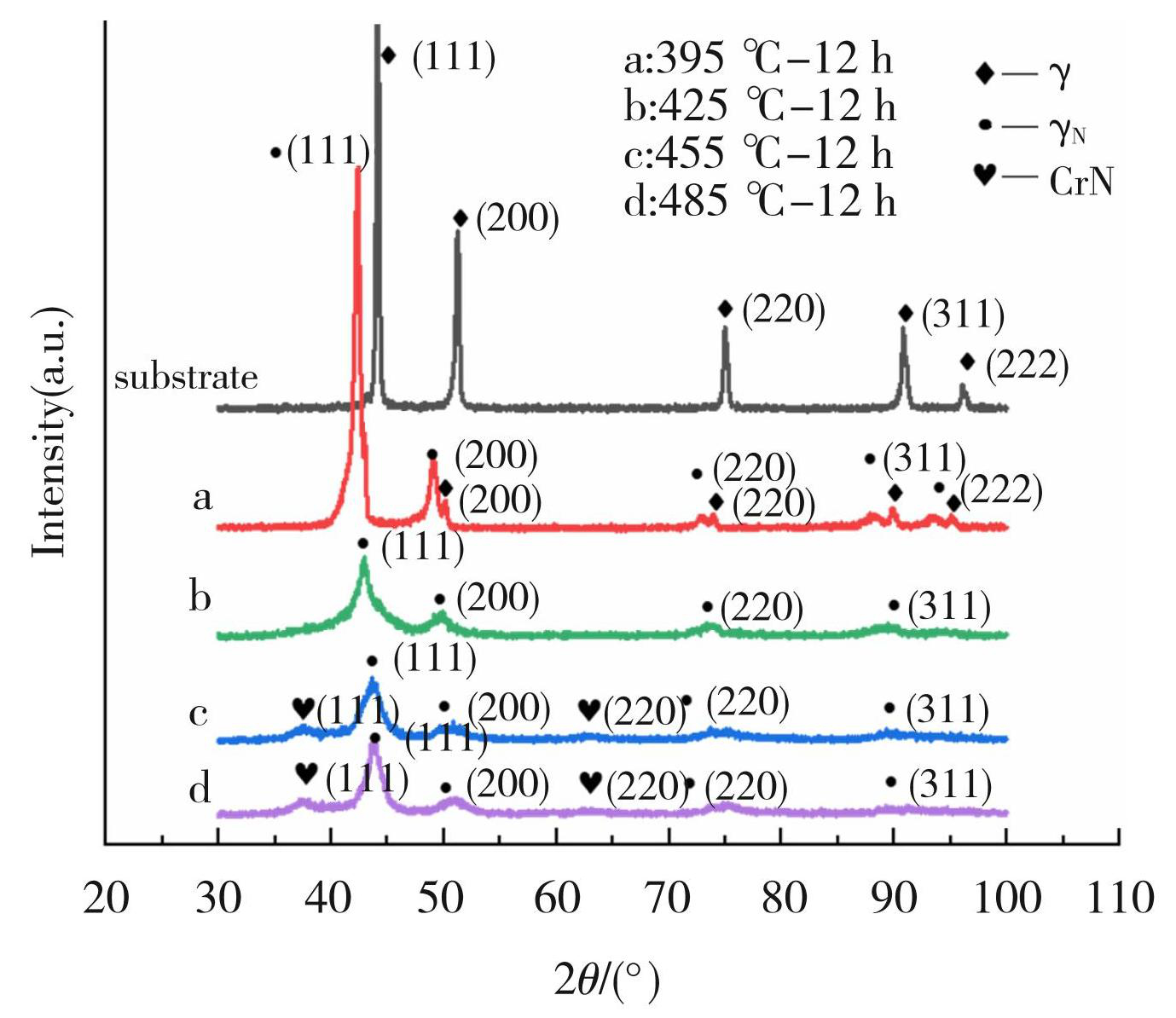
图2不同处理温度下共渗层X射线衍射(XRD)谱图
Fig.2X-ray diffraction (XRD) of the interpenetrating layer at different treatment temperatures
经过碳氮共渗处理后的的样品的衍射峰与基体相比明显宽化,而且宽化程度随着温度升高而加剧,这与样品基体中因氮和碳扩散而产生的残余应力有关。奥氏体不锈钢经过渗氮后表层形成SN相,经渗碳后表层形成SC相,两种S相并没有本质区别,这是因为C和N原子间隙固溶在奥氏体晶格中导致了晶格膨胀。在Zhao等[21]的研究中,证实了C和N可以同时溶解在面心立方(fcc)奥氏体晶格中,形成亚稳态氮和碳的膨胀奥氏体(S相)。
2.3 渗层硬度
图3为基体与经不同温度离子碳氮共渗试样的表面维氏显微硬度。从图3中可以看出,在经395~485℃、12 h碳氮共渗处理后,试样的表面硬度分别达到了基体的3~4倍。渗层的硬度主要与渗层的相组成和厚度有关。在辉光放电作用下,大量活性N、C原子高速持续轰击试样表面,试样表面的钝化膜被清除,N、C原子进入晶格内,形成过饱和间隙固溶体,即S相,氮原子进入奥氏体晶格发生间隙固溶强化,使得固溶体的硬度高于基体。当温度进一步升高或处理时间延长时,固溶体中的间隙原子超过固溶极限,产生了硬度更高的硬质相。在经离子碳氮共渗的4种试样中,485℃-12 h试样表面硬度最高,一方面是由于处理温度更高,N、C原子在镍基合金中的扩散更加迅速;另一方面,较高碳氮共渗温度下,Cr与N结合生成CrN,而CrN的硬度可达1 500HV左右,它的存在也对表面硬度的提高做出了贡献。
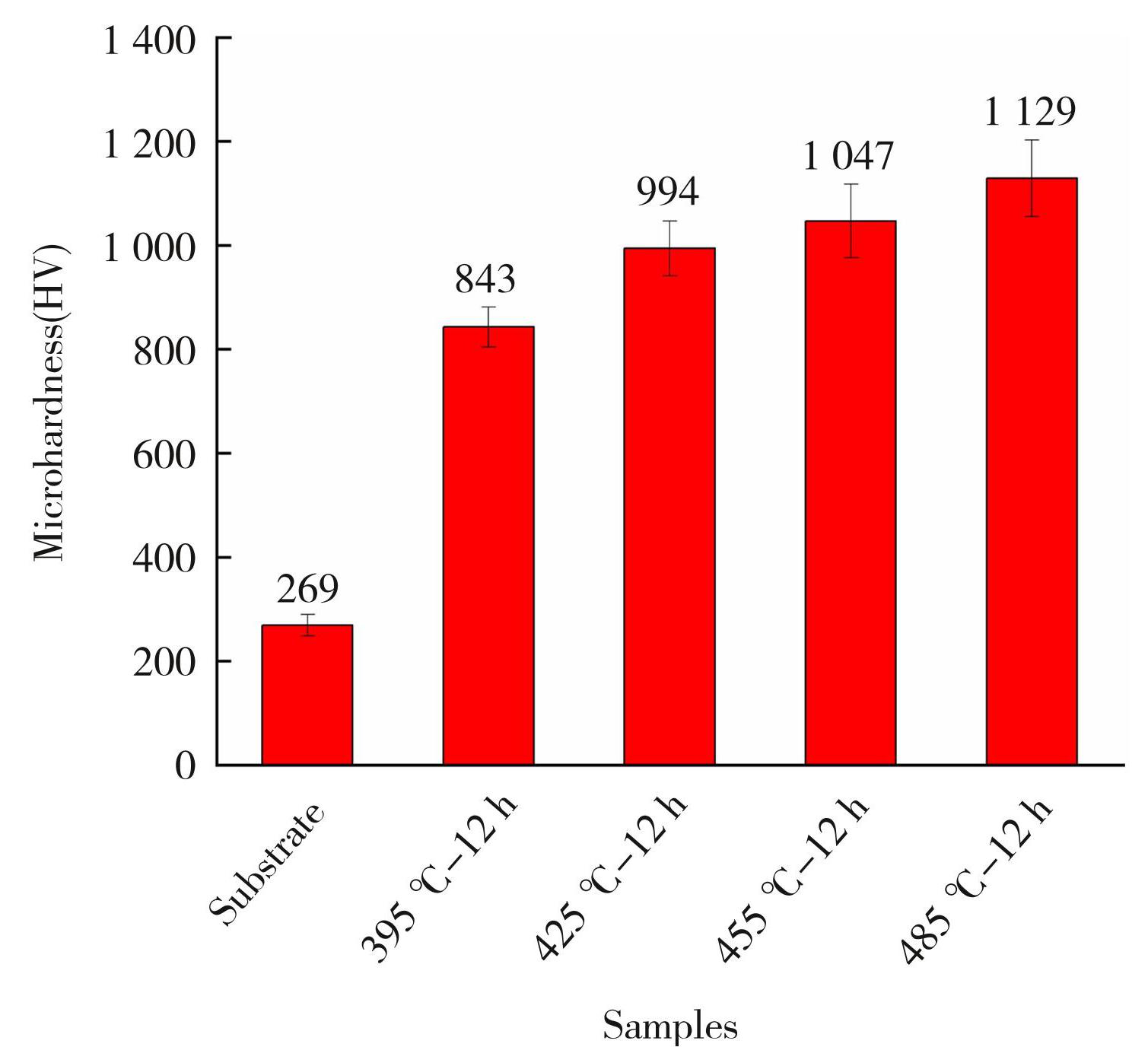
图3不同处理温度下的共渗层表面硬度
Fig.3Surface hardness of the interpenetrating layer at different treatment temperatures
图4为不同温度碳氮共渗试样截面渗层硬度与试样表面距离的关系。从图中可以看出,基体硬度在280HV~320HV范围内,485℃-12 h的试样由于渗层较厚且存在析出相CrN,从表面到9 μm处硬度值基本保持不变,在10~18 μm硬度随着到试样表面的距离增加而减小。试样395℃-12 h硬度在距离试样表面6 μm处接近基体。随着处理温度降低,由于扩散速度变慢,渗入奥氏体基体中的N、C原子减少,从而造成硬度降低。综上所述,在不同温度下碳氮共渗12 h处理后的C-276试样截面硬度分布存在梯度,且与金相观察到的渗层厚度相对应,随着处理温度增加,硬度下降趋势更大。硬度值随着其距各自表面深度的增加而降低。
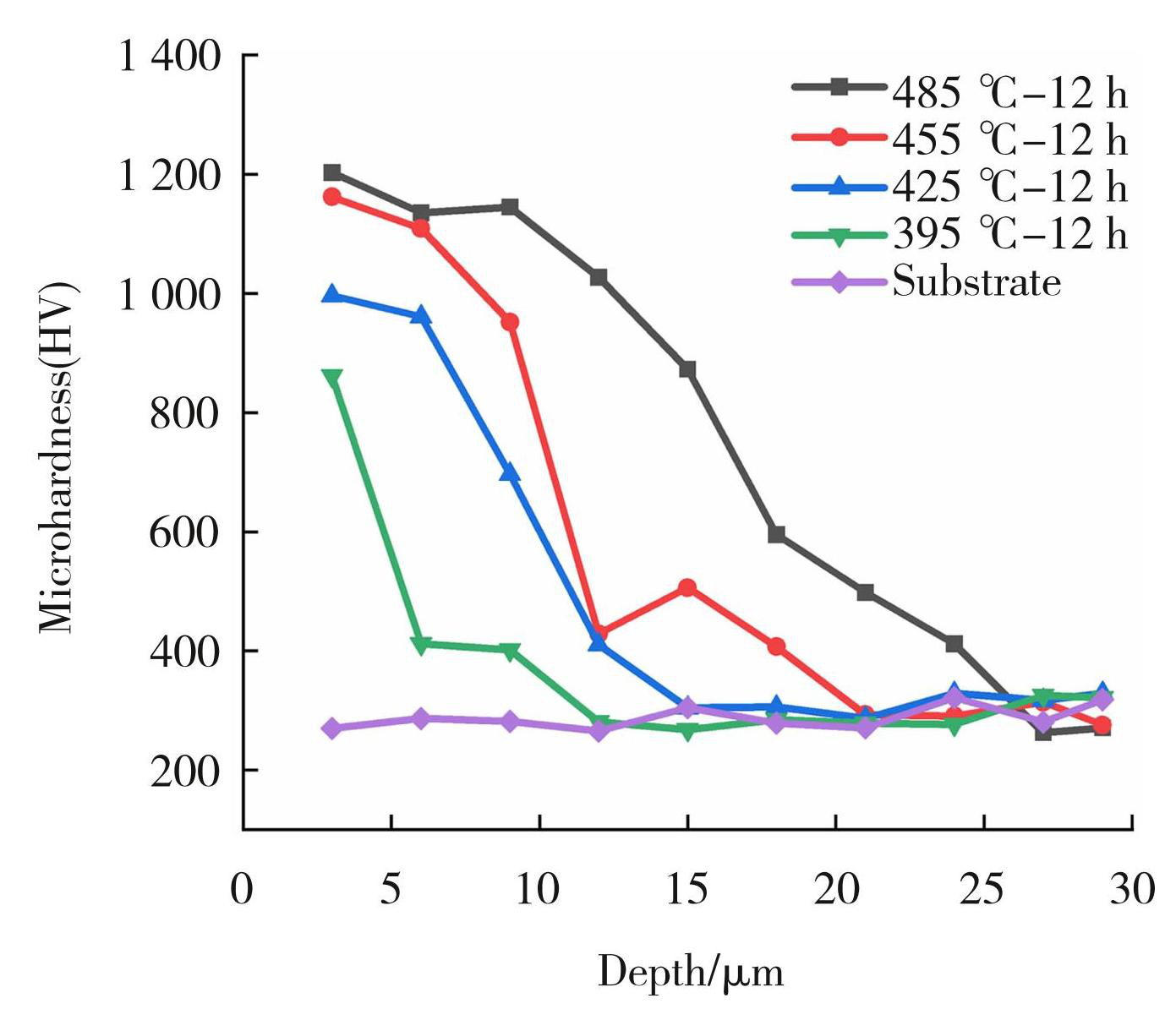
图4不同处理温度共渗层截面硬度分布
Fig.4Hardness distribution of cross section of interpenetrating layer at different treatment temperatures
2.4 摩擦学性能
图5为镍基合金C-276基体试样和在395、425、455和485℃下碳氮共渗处理试样在5 N载荷下的摩擦系数随时间变化曲线。从图5中可以看出,镍基合金C-276基体摩擦系数在初始阶段即快速上升到0.9附近,随后摩擦系数逐渐下降,从5 min开始稳定在0.6~0.8,但波动起伏较大,整个过程中最大摩擦系数为0.91,平均摩擦系数为0.71。试样395℃-12 h的摩擦系数则随着实验时间延长缓慢上升,由于该工艺下渗层较薄,到15 min后,随着渗层被磨穿,摩擦副与基体直接接触,造成摩擦系数变大,在22 min后,摩擦系数大小和波动起伏趋势与基体相一致,最大摩擦系数为0.78,平均摩擦系数为0.60。试样455℃-12 h摩擦系数在初始阶段即上升至0.5附近,随后在小范围内波动,最大摩擦系数为0.58,平均摩擦系数为0.51。随着处理温度的进一步升高,485℃-12 h摩擦系数逐渐减小,但摩擦系数波动相比于455℃-12 h较大,在磨损后期更加不稳定,平均摩擦系数为0.39。通过对比可知,425℃-12 h试样的摩擦系数在此批试样中最为稳定,平均摩擦系数为0.29,通常高硬度意味着更好的耐磨性能,但425℃-12 h处理的试样在硬度和厚度方面都不如455℃-12 h处理的试样却拥有更低的摩擦系数,原因可能是由于硬质相CrN在磨损过程中与含N、C的奥氏体固溶体相接触,导致455℃-12 h、485℃-12 h试样摩擦力相对较大。而425℃-12 h试样由于渗层较厚的S相兼顾较高硬度与耐磨性,不容易被磨穿,其摩擦系数也相对较低。
图6为在5 N载荷下,C-276基体和不同温度离子碳氮共渗处理后试样与氧化铝摩擦副对磨的摩擦磨损形貌图。
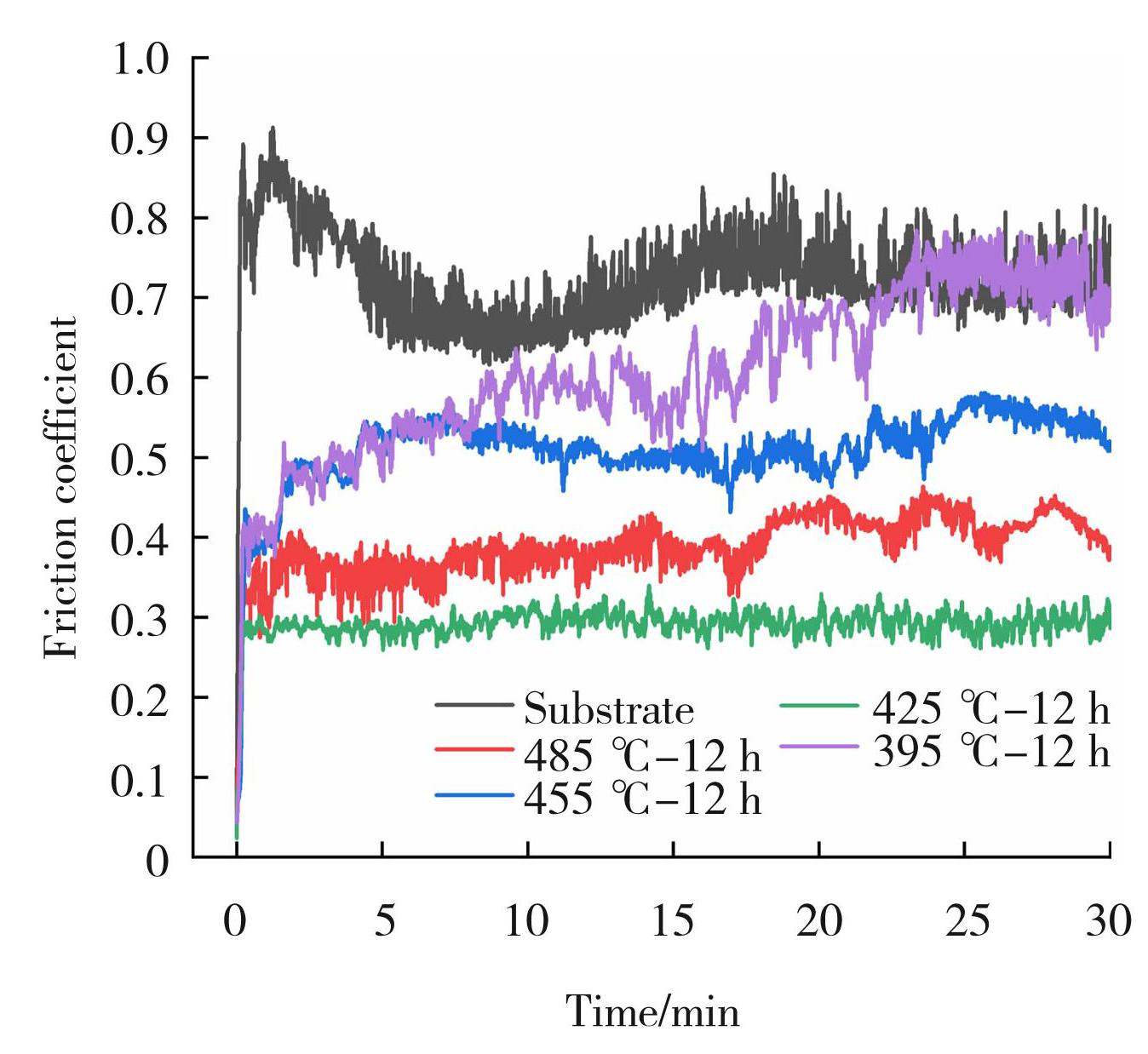
图5碳氮共渗试样的摩擦系数-时间曲线
Fig.5Friction coefficient time curve of carbonitriding sample
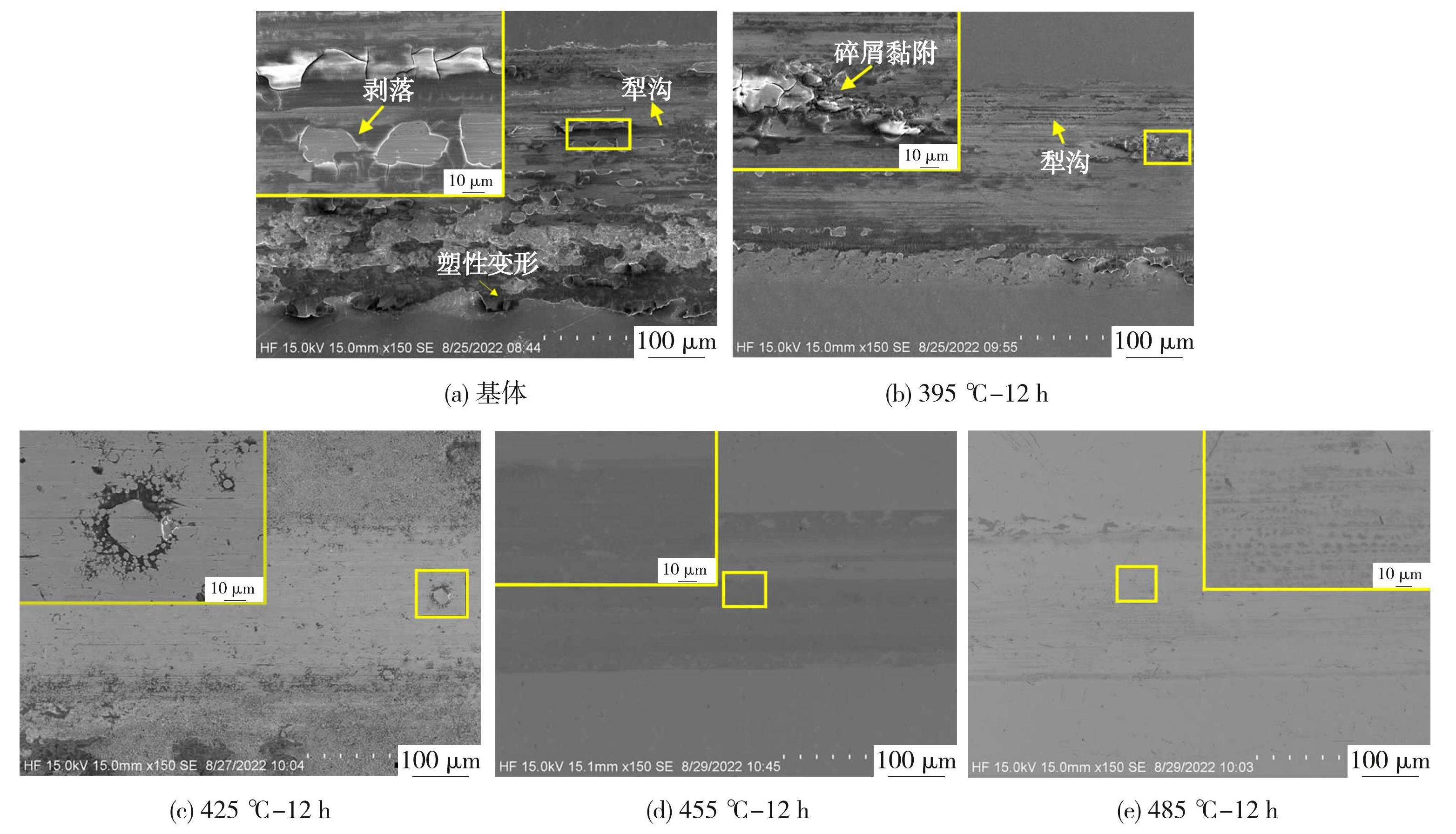
图6基体和不同共渗层在5 N载荷下的磨损形貌及局部放大形貌
Fig.6Wear morphology of carbonitriding layer under 5 N load and locally enlarged morphology: (a) substrate; (b) 395℃-12 h; (c) 425℃-12 h; (d) 455℃-12 h; (e) 485℃-12 h
从基体的磨痕形貌图6(a)可以看出,基体表面有明显的磨痕,磨痕深且宽,由于镍基合金C-276表面硬度低,在低载荷作用下,接触应力超过接触点屈服强度,磨痕边缘存在明显的塑性变形,磨痕中沿摩擦副滑动方向存在平行的犁沟且较深,在摩擦接触区沿着滑动方向出现了许多黑色片状粘着堆积物的磨屑,并出现了大量的剥落和黏附现象,接触面的损伤破坏严重,呈现出典型的磨粒磨损和黏着磨损特征。从图6(b)中可以看出395℃-12 h试样磨痕存在深浅不一的少量平行犁沟,同时出现了少量剥落和黏附现象,并且有少量磨屑堆积。可以看到磨痕表面存在黑色和白色分布的磨屑,这是由于随着磨损的进行,试样与摩擦副接触部分温度升高,摩擦表面与氧化介质反应形成了氧化物,可以推断试样的磨损形式是磨粒磨损和氧化磨损。同样的氧化物也可以在基体试样的磨痕形貌中观察到。从图6(c)中看出,425℃-12 h试样表面仅受到轻微磨损,磨痕浅且窄,磨损面没有黏附和剥落现象,也没有明显的犁沟和塑性变形,在1 000倍的局部放大图中,可以看到由于试样表面受到高能离子的轰击引起溅射再沉积形成的颗粒状结构被磨损,但并未完全磨损至试样基体裸露,说明渗层并未磨穿,磨痕中沿摩擦副滑动方向的少量犁沟表明该试样的磨损形式是以磨粒磨损为主。与425℃-12 h试样相似,455℃-12 h试样磨痕的磨损程度较轻(如图6(d)所示),磨痕中没有明显的犁沟和塑性变形,仅有少量的剥落产生,随着处理温度的升高,485℃-12 h试样的磨损程度最少(如图6(e)所示),该试样磨痕既没有因摩擦而产生的犁沟和剥落现象,也没有因试样与摩擦副反复摩擦导致温度升高而生成的黑色氧化物,该样品具有最佳的耐磨性。
图7为不同温度碳氮共渗处理后各试样在5 N载荷下的磨痕轨迹轮廓图和其磨痕轮廓截面图。
图7试样在5 N载荷下的磨痕轮廓与磨痕截面图
Fig.7Profile and cross section of wear mark of sample under 5 N load: (a) 395℃-12 h; (b) 425℃-12 h; (c) 455℃-12 h; (d) 485℃-12 h; (e) substrate; (f) two dimensional profile of different temperature wear marks
从图7中可以看出,基体试样的磨痕深度值为7.04 μm,磨痕宽度为560 μm,而试样395℃-12 h的磨痕深度值为8.33 μm,磨痕宽度为560 μm,对于基体和395℃-12 h试样,二者的磨损形式相似且摩擦系数和磨损体积的数值也相近。试样425℃-12 h、455℃-12 h和485℃-12 h的磨痕深度值分别为1.81、1.24、1.67 μm,磨痕宽度值分别为320、190、390 μm。由此可见,当碳氮共渗处理温度在425至485℃范围内,各试样的摩擦学性能差异不大。
2.5 电化学性能测试
图8为镍基合金C-276基体和不同处理温度碳氮共渗试样在3.5wt.%NaCl溶液中的Tafel极化曲线。其中横坐标为实验过程中施加在样品表面的电压,纵坐标为流经工作电极电流的对数。利用塔菲尔外推法得到样品的自腐蚀电位(Ecorr)、自腐蚀电流密度(Jcorr)数据结果如表3所示。
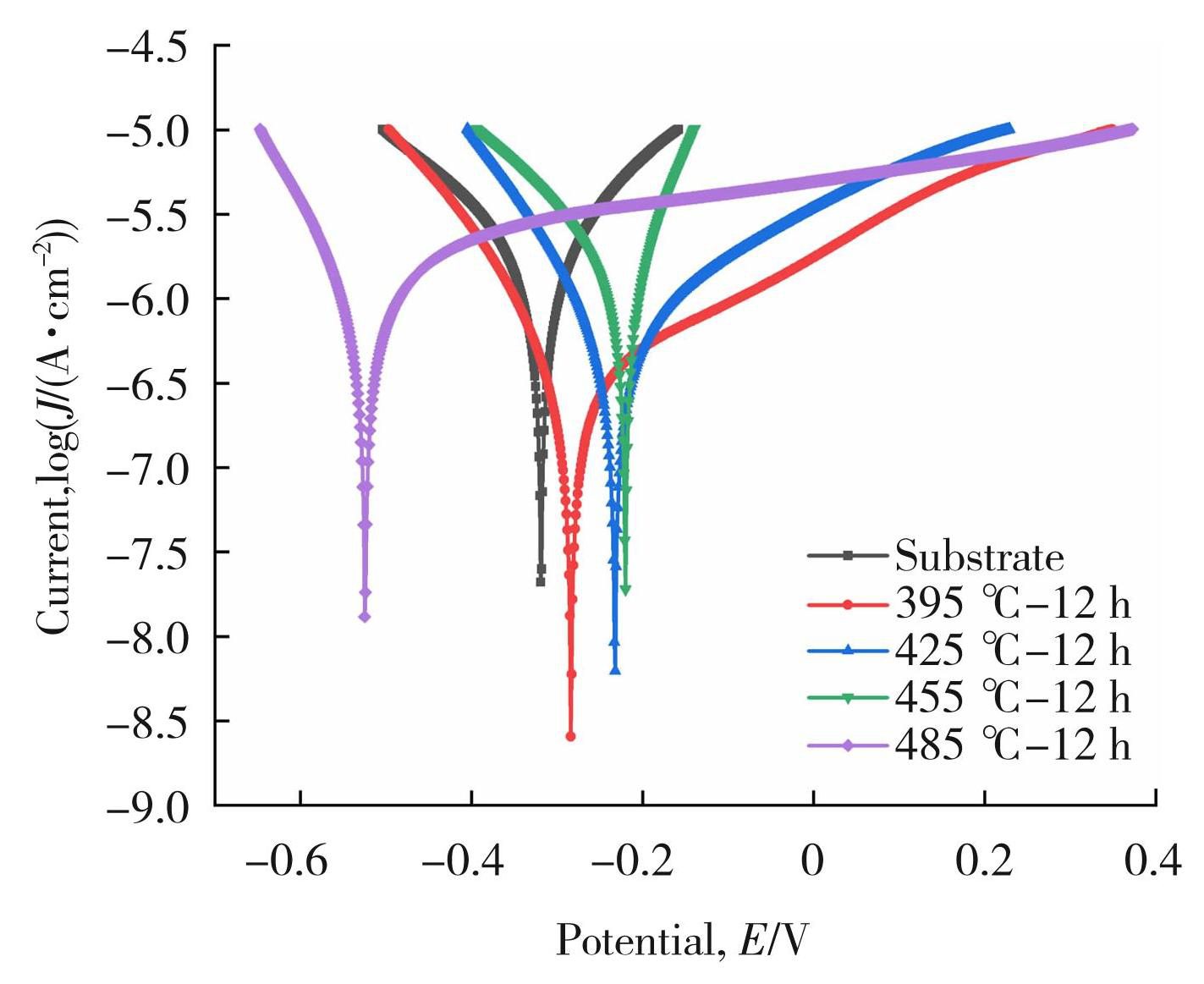
图8基体和不同温度碳氮共渗试样电化学极化曲线
Fig.8Chemical polarization curves of carbonitriding samples at different treatment temperatures
表3基体与不同温度碳氮共渗试样自腐蚀电位和自腐蚀电流密度
Table3Self-corrosion potential and self-corrosion current density of carbonitriding samples at different treatment temperatures

由表3可知,基体的自腐蚀电位为-0.319 V,自腐蚀电流密度最大,较低的腐蚀电位表明基体相对于其他试样耐腐蚀能力较低,且腐蚀速率最高。395℃-12 h试样的自腐蚀电位较高,与基体相比自腐蚀电流密度小了一个数量级,表明在较低温度下碳氮共渗对C-276合金的耐蚀性有所提升。随着碳氮共渗温度的升高,425℃-12 h和455℃-12 h试样的自腐蚀电流增大,说明耐蚀性有所降低,但仍优于基体试样的腐蚀速率。485℃-12 h试样自腐蚀电位低于基体,自腐蚀电流密度与基体相当,表明485℃-12 h试样的耐蚀性变差,原因是膨胀奥氏体分解生成铬的氮化物和碳化物沉淀使基体贫Cr,使得样品耐蚀性降低。综上所述,在低温(<450℃)碳氮共渗生成的S相,对基体的耐蚀性有所提高。在480℃以上进行碳氮共渗处理则使C-276合金的铬化物析出,耐蚀性降低。
3 分析与讨论
镍基合金C-276经C、N共渗处理后,表层硬度会得到有效提升,但其硬化层组织分为两种,当温度<425℃时,组织为极度过饱和固溶体(S相);当温度>425℃时,则是奥氏体基体上弥散分布着大量细小的硬质相。因硬质相主要由铬和钼的氮化物组成,所以会造成表层组织的耐蚀性下降,从金相照片上显示为硬化层变黑(王水腐蚀),但从不同工艺试样的自腐蚀电位和自腐蚀电流数据来看,由于镍基合金C-276含有17%的Cr和14%的Mo,即使有一定量的铬和钼以化合物形式析出,其在3.5wt.%盐水中的耐蚀性仍然保持较高水平。
随着处理温度升高,硬化层的厚度得到了提升,这对于耐磨性是比较有利的,因此存在处理温度提高,磨痕深度下降的趋势。不过温度升高会带来粗糙度变差,从而导致摩擦系数和磨痕宽度上升,对耐磨性带来不利影响。综上所述,425℃-12 h样品由于渗层厚度和粗糙度均处于相对较优的水准,保证了低的摩擦系数和承压能力,同时表层组织为耐蚀的S相,因此该组试样具有最好的综合性能。
4 结论
1)随着镍基合金C-276等离子碳氮共渗温度提高,活性N、C原子渗入试样表面,形成了S相碳氮共渗层,即氮和碳的膨胀奥氏体相。
2)经12 h碳氮共渗,395、425℃处理的试样渗层厚度分别为6.5、9.9 μm;455、485℃处理的试样渗层由S相和CrN组成,析出层厚度和渗层总厚度分别为3.2、14.0 μm和8.7、20.0 μm。渗层总厚度随着处理温度的提高而增加。
3)随着碳氮共渗温度的升高,试样表面硬度显著提高,约为基体的3~4倍。摩擦磨损实验表明,在较高的碳氮共渗处理温度(≥425℃)可形成高硬度的S相使其拥有良好的耐磨性能。电化学检测结果表明,在395~455℃碳氮共渗处理的镍基合金耐蚀性能有所提高,然而,在485℃下处理可造成基体贫Cr,耐蚀性降低。