摘要
多孔Ti-6Al-4V合金植入人体内将长期处于体液腐蚀环境中,且不可避免地承受人体自重和运动产生的载荷,易引发应力腐蚀,增加无菌失败和严重并发症的风险。为了明确载荷水平及孔隙特性对多孔Ti-6Al-4V合金应力腐蚀性能的影响,本文通过数值仿真方法研究其力-电化学响应规律。基于应力腐蚀理论,将由孔隙特性引发的结构应力耦合到电极反应的平衡电位和交换电流密度表达式,建立了力-电化学耦合有限元模型,通过数值仿真方法分析了植入物试样承受弯曲载荷时,应力、电流密度以及电极腐蚀厚度等的力-电化学响应规律。结果表明:随着承载水平增加,应力集中明显的孔隙边缘区域腐蚀更为剧烈,最大腐蚀厚度均出现在孔梁边缘处。与无应力试样相比,超过屈服应力试样的5年腐蚀厚度增加了22%。孔隙尺寸显著影响应力分布、电化学腐蚀速率及最终的电极腐蚀厚度,随着孔隙的增大,电极5年腐蚀厚度逐渐减小,且大孔应力腐蚀速率低于小孔。
Abstract
Porous Ti-6Al-4V alloy, when implanted in the human body,is exposed to body fluid corrosion environment and inevitably experiences loads generated by human weight and movement. This can lead to stress corrosion, increasing the risk of sterility failure and serious complications. In order to clarify the influence of load level and pore size on the stress corrosion performance of porous Ti-6Al-4V alloy, this paper studies the mechanical electrochemical response through numerical methods.Based on stress corrosion theory, the equilibrium potential and exchange current density expressions of electrode reactions are coupled with the structural stresses induced by pore characteristics. A coupled mechanical-electrochemical finite element model is established. When the implant specimen is subjected to bending loads, the mechanical electrochemical responses,such as stress, current density and electrode corrosion thickness,are analyzed by numerical simulation.The calculation results show that with the increase of load level, the corrosion is more severe in the pore edge area with significant stress concentration. The maximum corrosion thickness occurs at the edges of the pore. Compared to specimens without stress, the corrosion thickness of specimens with stress after 5 years increases by 22% for specimens exceeding the yield stress. The pore size significantly affects the stress distribution, electrochemical corrosion rate and the final electrode corrosion thickness. With the increase of the pore size, the 5 year corrosion thickness of the electrode gradually decreases, and the stress corrosion rate of the large pore is lower than that of the small pore.
金属增材制造(Additive Manufacturing,AM)技术特别适合复杂金属构件的高性能制造,将其与表面改性技术相结合,为制备个性化、多孔钛合金植入物提供了新方法[1-3]。目前,针对AM多孔钛合金微观结构[4]、力学表征[5-8]和骨整合表征[9-10]等方面的研究较多。孔隙特征对生物材料上述性能的影响也已得到广泛认可。但考虑到人体体液是一个复杂的环境,长期应用造成的应力腐蚀问题不可避免,腐蚀产物的释放将引起局部或全身效应[11-12],增加无菌失败和严重并发症的风险[13-14]。
对于多孔钛合金的电化学腐蚀研究,有观点认为,孔隙等同于缝隙[15],阻碍了电解质和氧气在孔隙中的扩散,孔隙内钝化膜的初始失效导致孔隙内部加速溶解[16]。由于与电解质具有更大的接触表面积,多孔钛合金的腐蚀敏感性高于致密钛合金[17-18]。但也有观点认为,多孔材料的腐蚀性能与孔隙的连通性和几何形状有关,表面积并不是影响腐蚀速率的唯一因素[18-19]。因此,关于孔隙尺寸、孔隙率对腐蚀性能的影响,仍存在不同结论:一种是耐腐蚀性随着孔隙度的增加而增加[20],另一种是腐蚀速率随着孔隙度的增加而加速[21-22]。
另外,植入物在人体内不可避免地承受人体自重和运动产生的载荷,不同表面微结构可能发生不同程度变形。当植入物处于由人体介质组成的腐蚀环境中时,腐蚀和载荷引起的破坏过程交织在一起,其效果可能比其中任何一种因素单独作用时更严重[23]。然而,目前的研究并未考虑力学因素对腐蚀电场的影响,针对多孔钛合金在模拟体液中的应力腐蚀行为的相关研究较少。因此,承载条件下,应力如何影响多孔Ti-6Al-4V合金腐蚀性能的问题仍有待探究。为此,本文基于应力腐蚀理论,将由孔隙特性引发的结构应力应变,耦合到电极反应的平衡电位和交换电流密度表达式,建立腐蚀电场的力-电化学耦合模型,并借助有限元仿真,研究植入物试样在模拟体液中承受弯曲载荷时,孔隙特性对力学电化学耦合效应下应力、电流密度以及腐蚀电场的影响规律。
1 力电化学耦合有限元模型建立
1.1 几何模型的建立
采用商用COMSOL多物理软件,对多孔钛合金腐蚀的机械电化学效应进行有限元模拟。植入物在人体不同部位所承受的载荷较为复杂,其中人体骨多承受压缩载荷,当载荷呈偏心状态时,变形以弯曲为主。本文根据图1(a)所示的三点弯曲应力腐蚀实验的试样标准[24],建立几何模型。图1(b)、(c)分别为模型的三维示意图及具体尺寸图,模型长40 mm,宽度为8 mm,高度为1 mm,下方紫色区域为钛合金试样,上方灰色区域为模拟体液。其中,钛合金与模拟体液仅在试样中间区域接触,接触面为电极表面(橙色区域),如图1(c)所示。
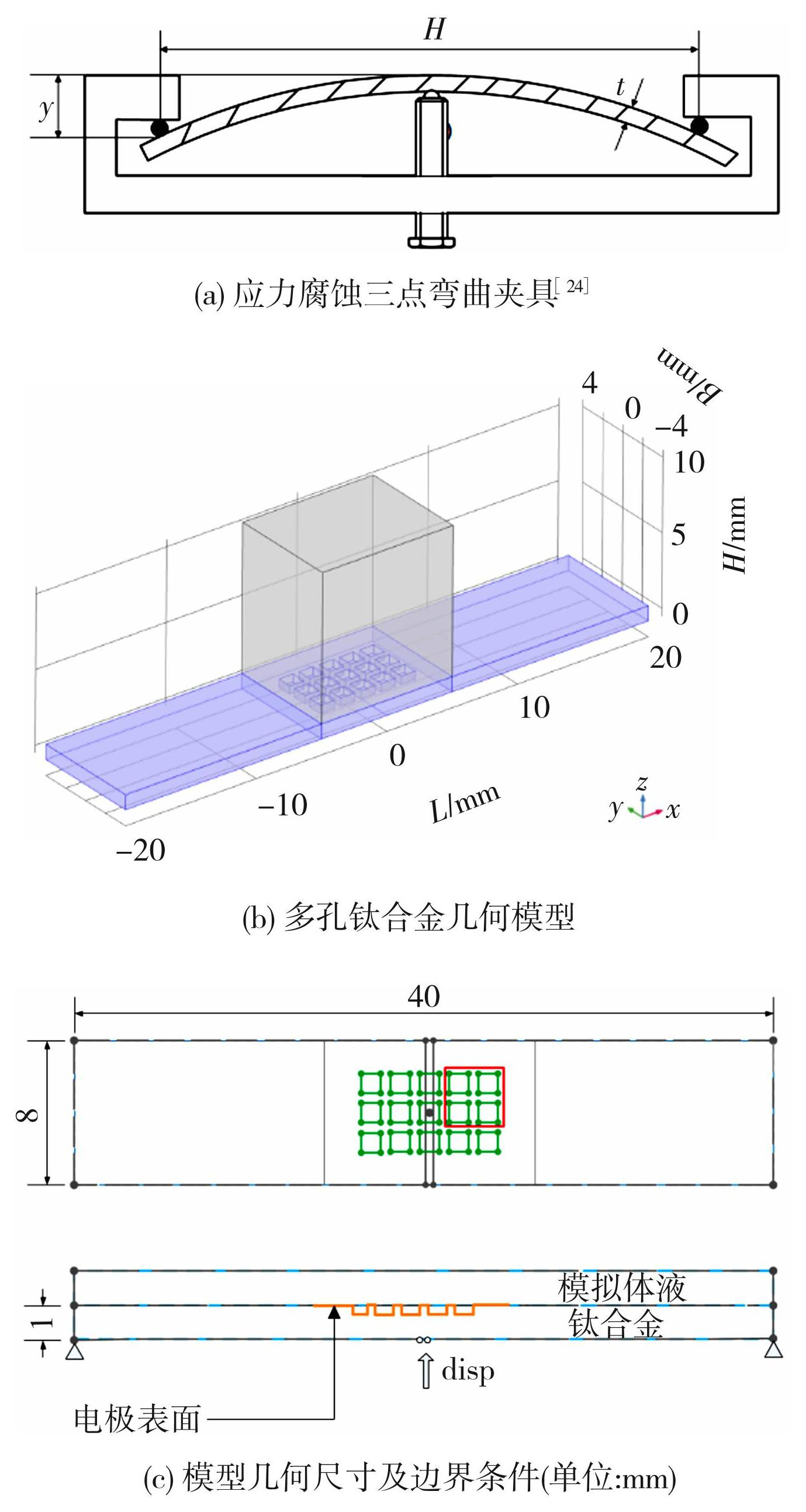
图1多孔钛合金建模
Fig.1Modeling of porous titanium alloy: (a) stress corrosion three-point bending fixture[24]; (b) geometric models of porous titanium alloys; (c) model geometry and boundary conditions
三点弯曲加载试样的最大拉应力在其凸面中点处,以该点为中心,布置3行5列孔隙。多孔孔隙尺寸参照图2所示的Gai等[25]和Radlof等[26]制备的用于人体骨植入物的多孔Ti-6Al-4V合金形貌。孔隙尺寸分别为323.7、462.70和1 081.8 μm,孔大小规则,形状分布规律,孔隙率随之由24.6%増加至70.3%,具体参数见表1。图2(c)为图1(c)红色方框孔隙尺寸放大图,以最大孔隙为例,标注孔隙尺寸及孔梁厚度。
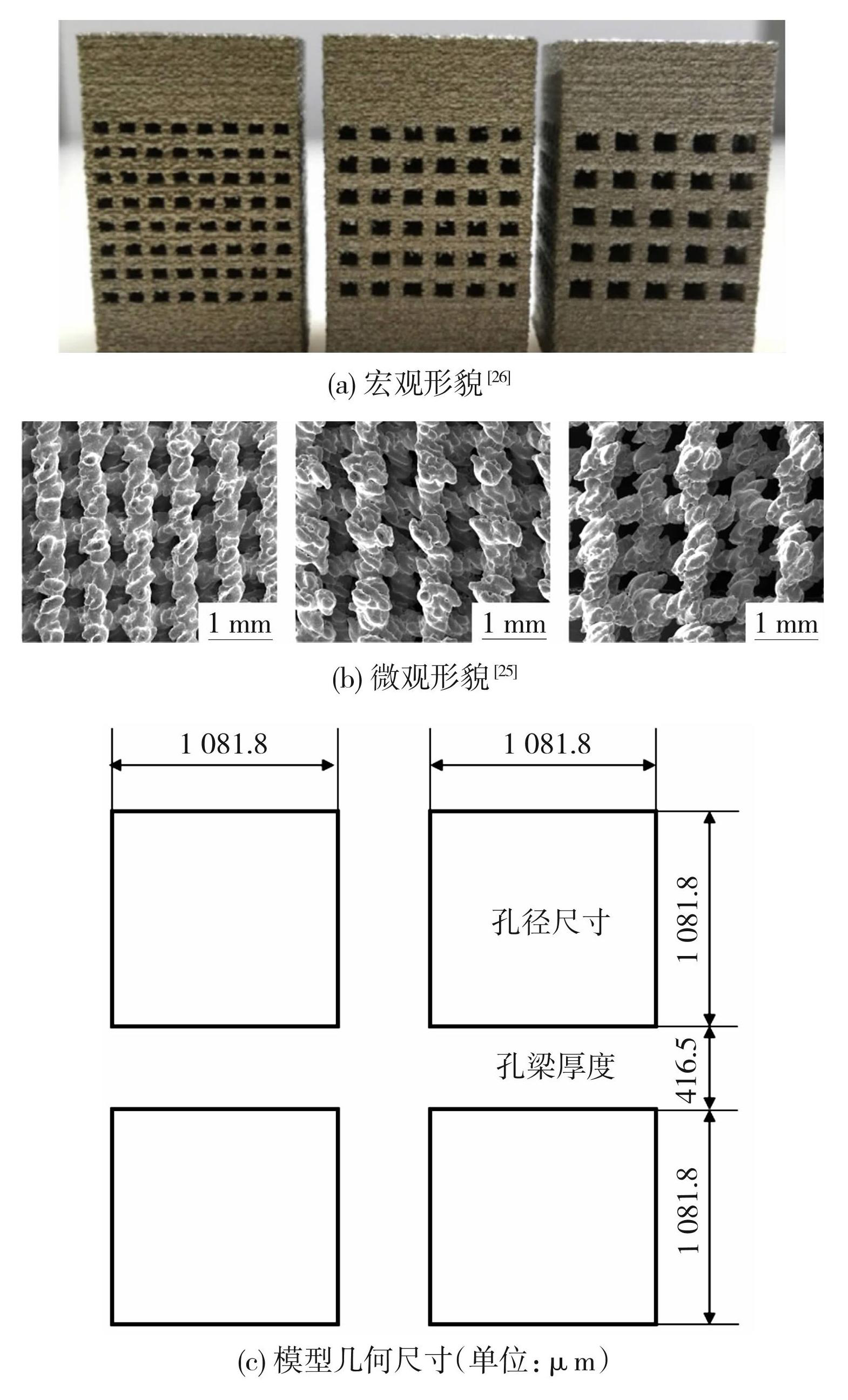
图2多孔钛合金形貌
Fig.2Morphology of porous titanium alloy: (a) macroscopic morphology [26]; (b) micromorphology [25]; (c) model geometry
表1钛合金植入物形貌特征
Table1Morphology characteristics of titanium alloy implants
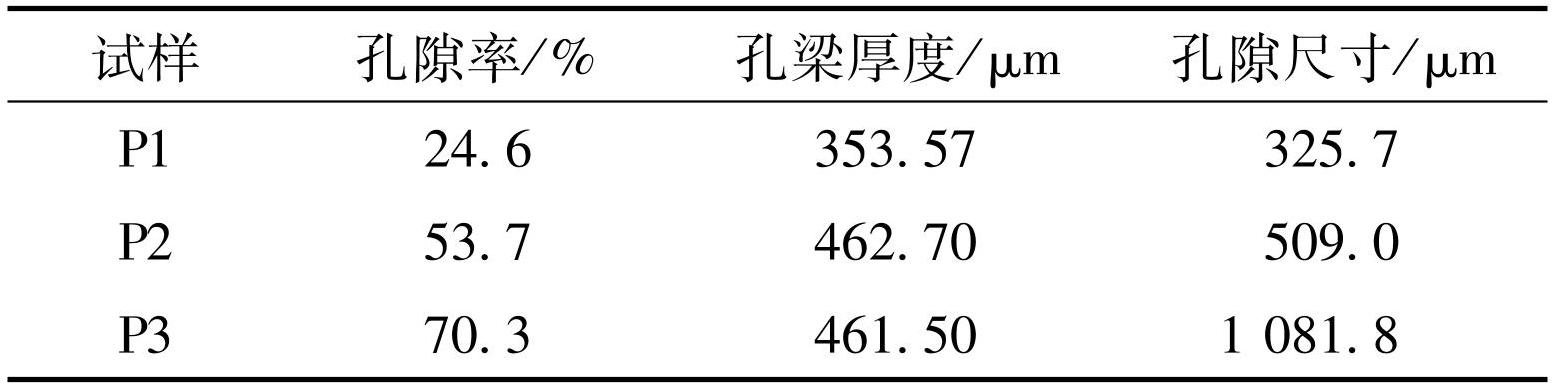
1.2 多物理场耦合方程
多孔钛合金植入物植入人体后应能承受1百万个步态周期,以髋关节为例,每年约3.6×106周次。其表面直接与周围环境中的组织和细胞相互作用[27],植入物表面微结构-载荷-生理腐蚀环境共同作用,属于多物理场耦合,涉及变形、应力、物质传输、电化学等。本文从弹塑性应力、腐蚀介质和界面处的电流密度、多孔结构力-电化学耦合3个方面进行有限元分析,其中与力-电化学耦合效应相关的关键方程如下。
1.2.1 阳极反应
阳极反应用阳极Tafel表达式表示,阳极的局部电流密度为
(1)
式中:i0,a为交换电流密度;ba为Tafel斜率;ηa为过电位。其中,
(2)
式中:φs为外部电位;φl为电解质电位;Ea,eq为平衡电位。平衡电位[28]由式(3)右侧的3项组成,第1项为阳极反应的标准平衡电位,第2项为弹性变形引起的平衡电位变化,第3项为塑性变形引起的平衡电位变化。
(3)
(4)
(5)
式中:ΔPm等于1/3材料的屈服强度;Zm为钛腐蚀的平均电荷数(Zm=4);Vm为钛的摩尔体积(Vm=9.48×10-6 m3/mol);R为理想气体常数(R=8.315 J/mol·K);T为绝对温度(T=298.15 K),F为法拉第常数(F=96 485 C/mol);α为方向决定因素(α=0.45);N0为塑性变形之前位错的初始密度(N0=4.81×109 cm-2)[29];εp为通过弹塑性模拟得到的塑性应变。
1.2.2 阴极反应
载荷引起的变形可改变阴极面积,导致电化学反应重新分布。塑性变形过程中产生的滑移台阶、微裂纹和表面缺陷的增加会降低反应活化能。阴极反应采用阴极Tafel表达式表示,阴极的局部电流密度为
(6)
式中:i0,c为交换电流密度;bc为Tafel斜率;ηc是过电位。阴极过电位可表示为
(7)
其中,Ec,eq0为阴极反应的标准平衡电位,其他参数与式(2)含义相同。
阴极反应的交换电流密度为
(8)
式中:i0c为无外部应力/应变情况时的交换电流密度;σMises为由模拟计算得到的Von Mises应力。
1.3 材料属性
1.3.1 固体力学参数
对钛合金进行弹塑性固体应力模拟时,选择各向同性硬化模型[28],其表达式为
(9)
式中:σexp为钛合金的应力应变曲线; σys为钛的屈服强度,即880 MPa; εp为是塑性应变; σe是有效应力; E为是弹性模量,即110 GPa。
1.3.2 电化学参数
Robert 等[30]研究了37℃下,Ti-6Al-4V植入物在尿液、血清和关节液3种体液中的电化学腐蚀行为。通过Tafel外推,得到不同体液对应的腐蚀电位(Ecorr)、腐蚀电流密度(icorr)、阳极和阴极Tafel斜率(ba和bc)。本文以关节液的实验数据作为有限元模拟初始输入的电化学腐蚀参数,如表2所示。
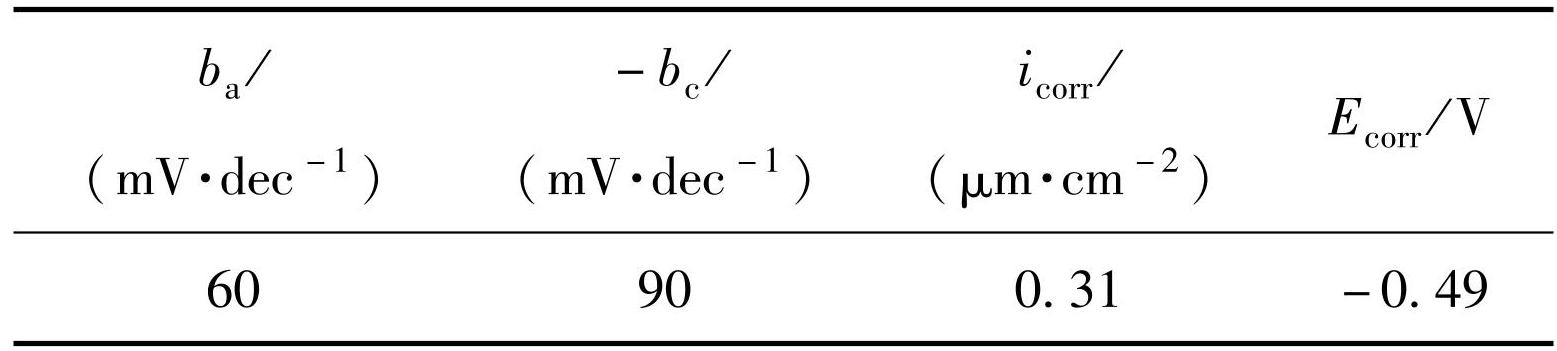
1.4 物理场选择及边界设置
应力腐蚀为多物理场耦合过程,选择固体力学和二次电流两个物理场进行耦合。通过固体力学接口计算弹塑性应力,通过二次电流接口实现腐蚀介质域的电流密度分析,电荷转移与过电位之间的关系通过Tafel方程来表示。钛合金与模拟体液接触面为电极表面,随着阳极表面腐蚀电极边界移动,其法向移动速度v可由下式计算
(10)
式中:ia为阳极电流密度; M为钛的摩尔质量; ρ为钛的密度。钛合金与模拟体液接触面作为电极界面的移动过程,通过变形几何进行建模,借助瞬态方法求解模型,模拟应力腐蚀时间为5年。
本文根据应力腐蚀试样标准,建立三点弯曲有限元模型,约束试样左、右两端,下方中间处承受垂向位移(用disp表示)。利用COMSOL软件中参数化扫描功能实现三点弯曲位移变化,以disp作为扫描参数,取值分别为0、0.8、1.0、1.2、1.4、1.6 mm。网格类型为四面体网格,同时细化钛合金孔隙与模拟体液的接触面(蓝色区域)。如图3所示,模型单元数共计16 505个。
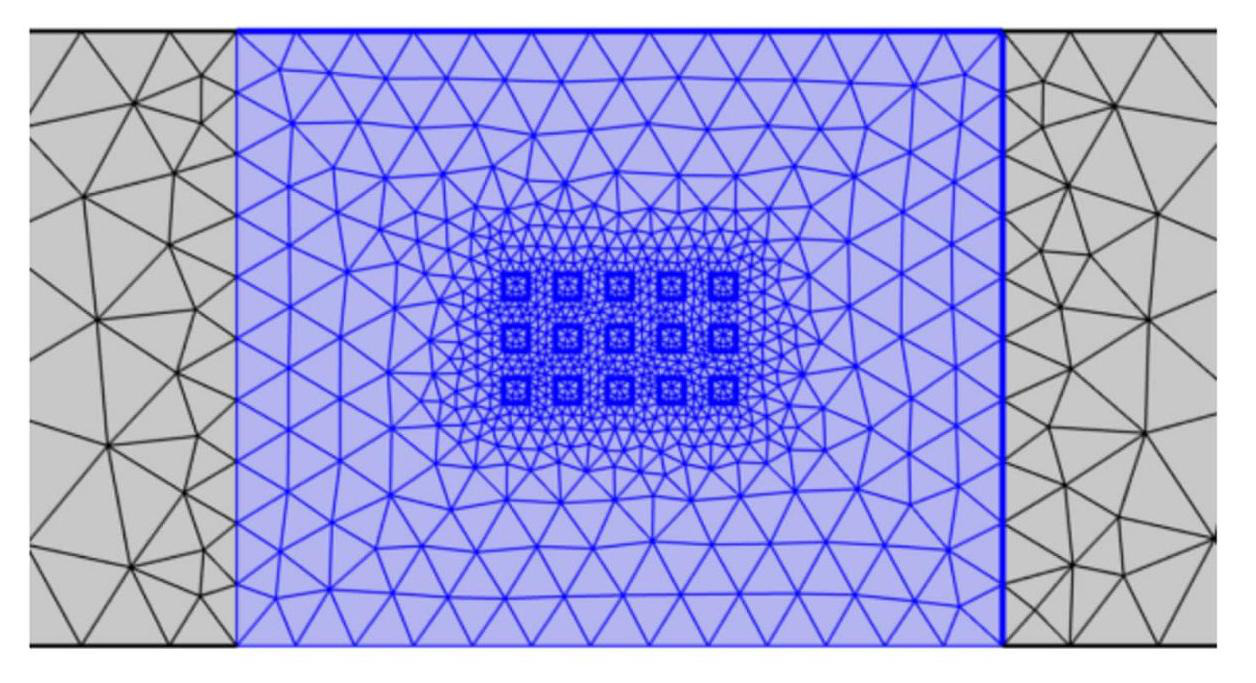
图3有限元网格
Fig.3Finite element mesh
2 模拟结果对比分析
2.1 力学电化学效应对电流密度的影响
有限元模型包括试样表面的电化学腐蚀反应、多孔试样在弯曲载荷下的应力-应变行为以及孔隙内部及孔梁处的应力加速腐蚀3类。孔隙尺寸323.7 μm,加载位移为1.4 mm的电极应力及电解质电流密度如图4所示。从图4可以看出,试样中部承受向上载荷,中间位置处孔、梁边缘处应力较大,电流密度由两侧向中间,中间含有孔隙区域应力水平高,电流密度大。

图4多孔Ti-6Al-4V合金Von Mises应力及电解质电流密度云图
Fig.4Von Mises stress and electrolyte current density cloud image of porous Ti-6Al-4V alloy
为了比较不同加载位移的应力和腐蚀电流密度分布,本节取图4蓝色线框位置,绘制Von Mises应力和电流密度曲线图(图5),横轴为x方向坐标,纵轴左侧为Von Mises应力,右侧为腐蚀电流密度。由图5可以看出,未加载时应力和局部电流密度均为0,随着施加载荷的逐渐增大,孔隙边缘处应力逐渐增加并超过屈服应力,与之对应的腐蚀电流密度增加,说明随着载荷的增大,应力集中较为明显的孔隙边缘区域腐蚀更为剧烈。
2.2 力学化学效应对电极腐蚀厚度的影响
图6为孔隙尺寸509.0 μm,加载位移分别为0、1.0、1.2、1.4、1.6 mm,模拟应力腐蚀时间为5年的电极腐蚀厚度变化云图,模型中电化学计算输入条件保持一致,固体力学只改变加载位移。由图6可知,随着施加载荷的增加,电极的5年腐蚀厚度受应力影响较大,未承受载荷时,腐蚀厚度最大为0.024 33 mm,随加载位移增大,5年腐蚀厚度逐渐增大,最大腐蚀厚度均出现在孔梁边缘处,具体数值见表3。
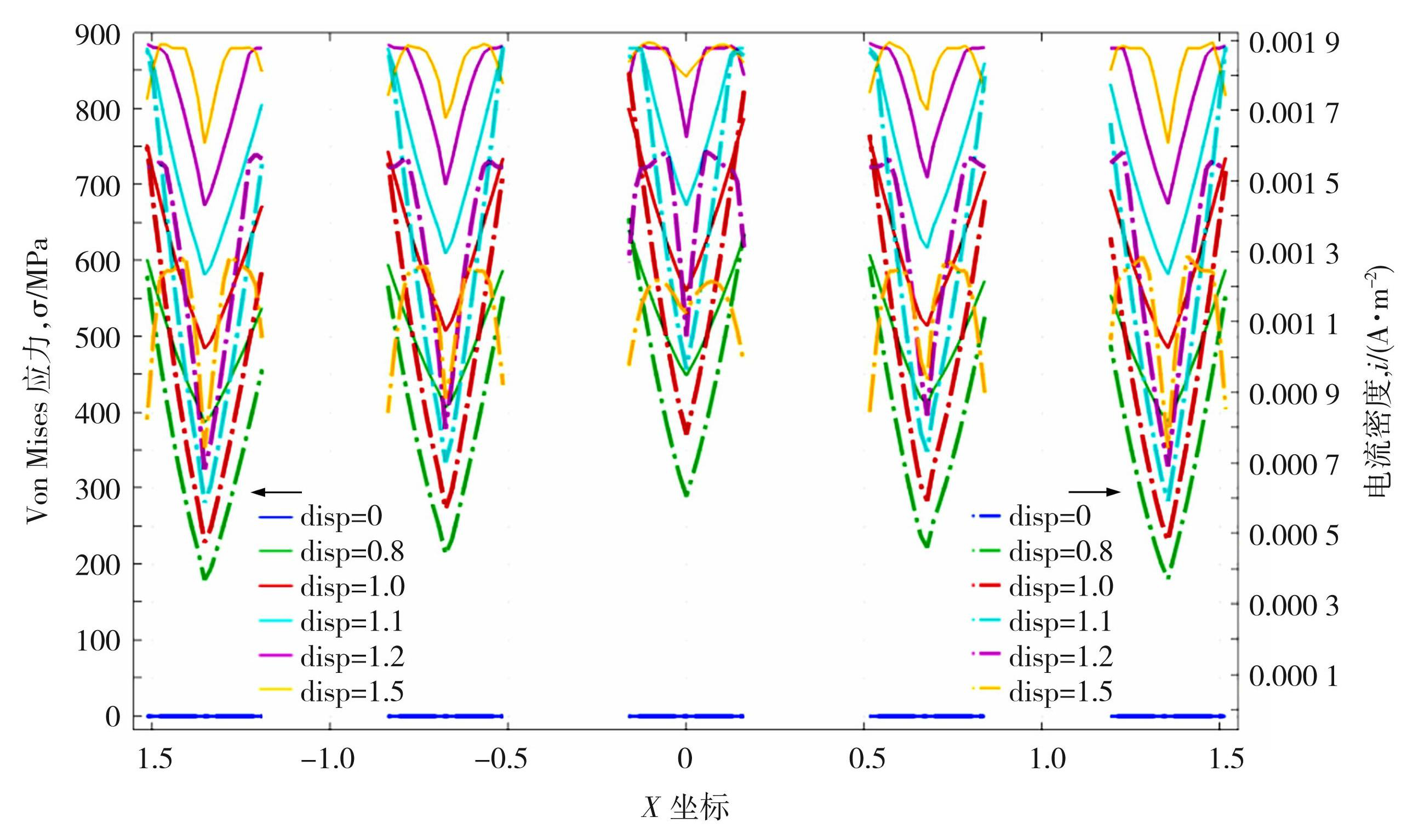
图5不同载荷下Von Mises应力和电流密度曲线图
Fig.5Von Mises stress and current density curves under different loads
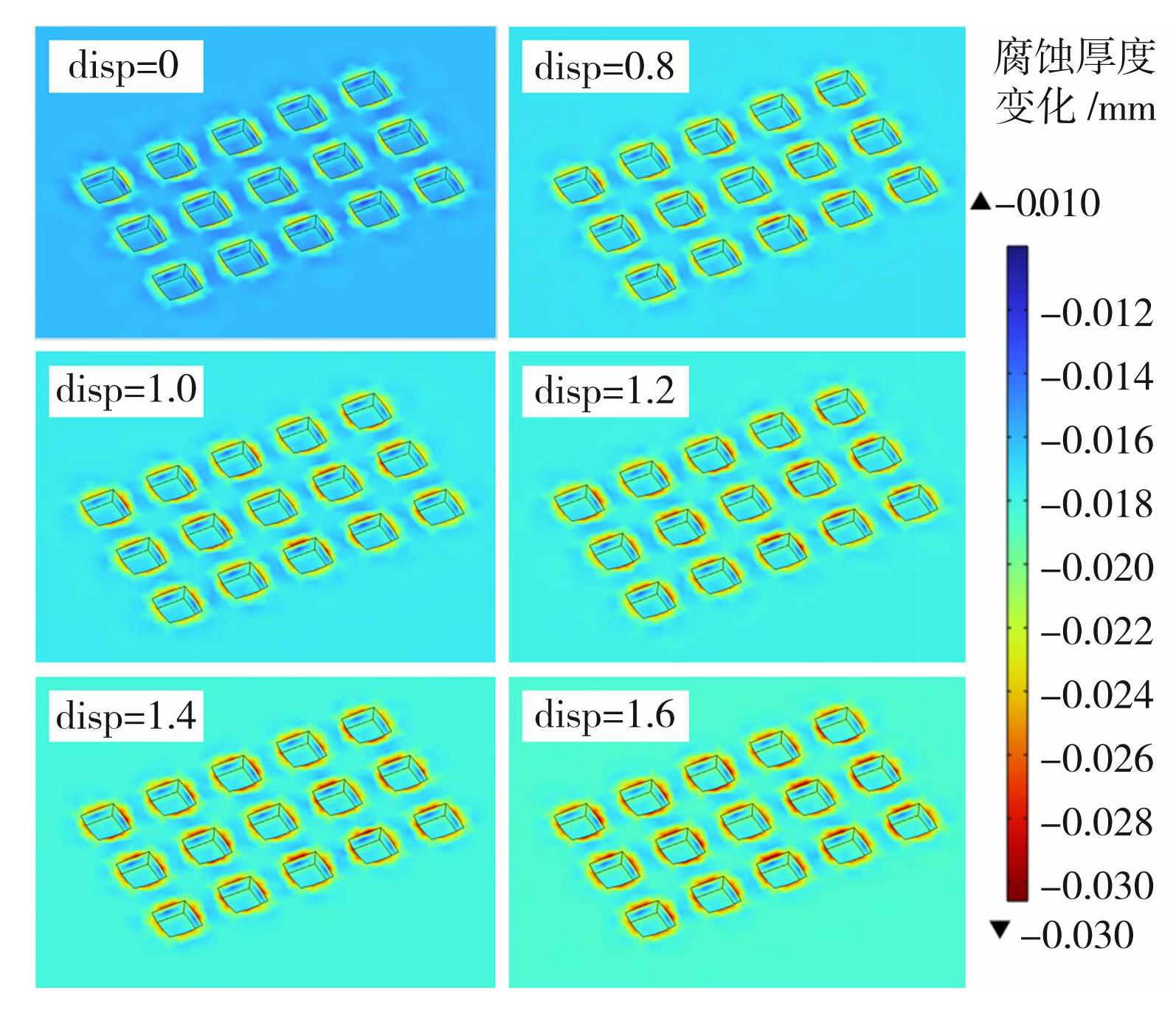
图6不同载荷下Ti-6Al-4V合金腐蚀厚度变化(腐蚀时间5年)
Fig.6Change of corrosion thickness of Ti-6Al-4V alloy under different loads (corrosion time 5 years)
表3不同载荷下Ti-6Al-4V合金腐蚀厚度变化
Table3Corrosion thickness changes of Ti-6Al-4V alloy under different loads
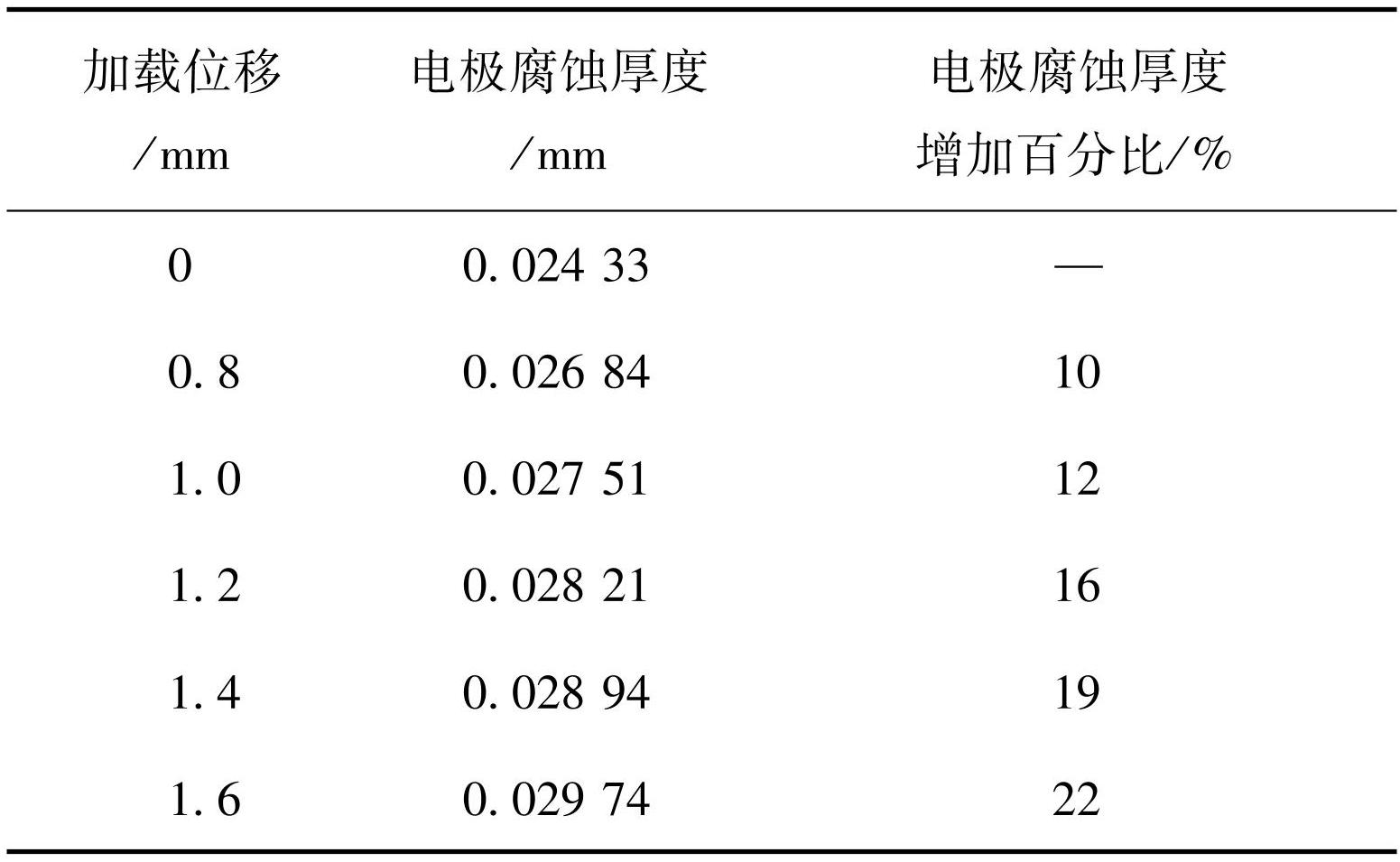
为了量化应力对电极厚度变化的影响,以无应力条件,即未加载时电极腐蚀厚度为基准,计算加载条件下电极腐蚀厚度增加的百分比,可以看出垂向位移为0.8 mm时,电极腐蚀厚度比未加载时增加了10%,此时的电极应力及腐蚀电流密度如图7(a)所示。

图7多孔Ti-6Al-4V合金von Mises应力及电解质电流密度云图:(a)腐蚀初始阶段;(b)腐蚀5年
Fig.7Von Mises stress and electrolyte current density of porous Ti-6Al-4V alloy: (a) initial corrosion; (b) corrosion for 5 years
孔梁边缘处,应力集中更明显,加载初始阶段,最大Von Mises应力为579 MPa,随腐蚀时间的增加,腐蚀厚度变化导致孔隙几何形貌改变,相同承载条件下,应力水平略有差异,图7(b)为模拟应力腐蚀5年的Von Mises应力,其最大值为559 MPa。孔梁边缘处较高的应力水平使得该区域较无应力电极更易发生电化学腐蚀,电极腐蚀厚度增加了10%。随载荷继续增加至1.6 mm时,电极腐蚀厚度最大达到0.029 mm,较无应力情况增加了22%,说明试样应力水平显著影响电极腐蚀厚度。
2.3 孔隙特性对电化学行为的影响
多孔结构对骨长入有促进作用,孔隙尺寸同时影响固体力学应力水平及电化学反应速率。本文将比较3种孔隙尺寸(小尺寸323.7 μm、中尺寸509 μm、大尺寸1 081.8 μm)对电极腐蚀厚度的影响,模型中改变固体力学加载水平,其余固体力学及电化学反应参数保持一致,计算结果见表4。由表4可以看出,随着孔隙的增大,电极腐蚀厚度逐渐减小,说明大孔应力腐蚀速率低于小孔。这一结果与Sharma等[31]和Gai等[25]的研究结果类似,而与Alves等[17]的研究结果不同。主要原因是Alves 等的研究对象为孤立且形状不规则的小孔隙,孔隙形态复杂,电解质难以填充进入小孔隙,导致氧气很快耗尽且得不到有效补充,因此孔隙内钝化膜生长较慢,同时,Alves 等的研究中也未考虑应力对电化学腐蚀过程的影响。本文将所研究的孔隙布置于试样表面,与电解质直接接触,较大的孔隙减小了由电化学反应引起的孔内微环境变化,因此降低了局部腐蚀的风险。
表4孔隙尺寸对多孔Ti-6Al-4V合金腐蚀厚度变化影响
Table4Effect of pore size on corrosion thickness change of porous Ti-6Al-4V alloy
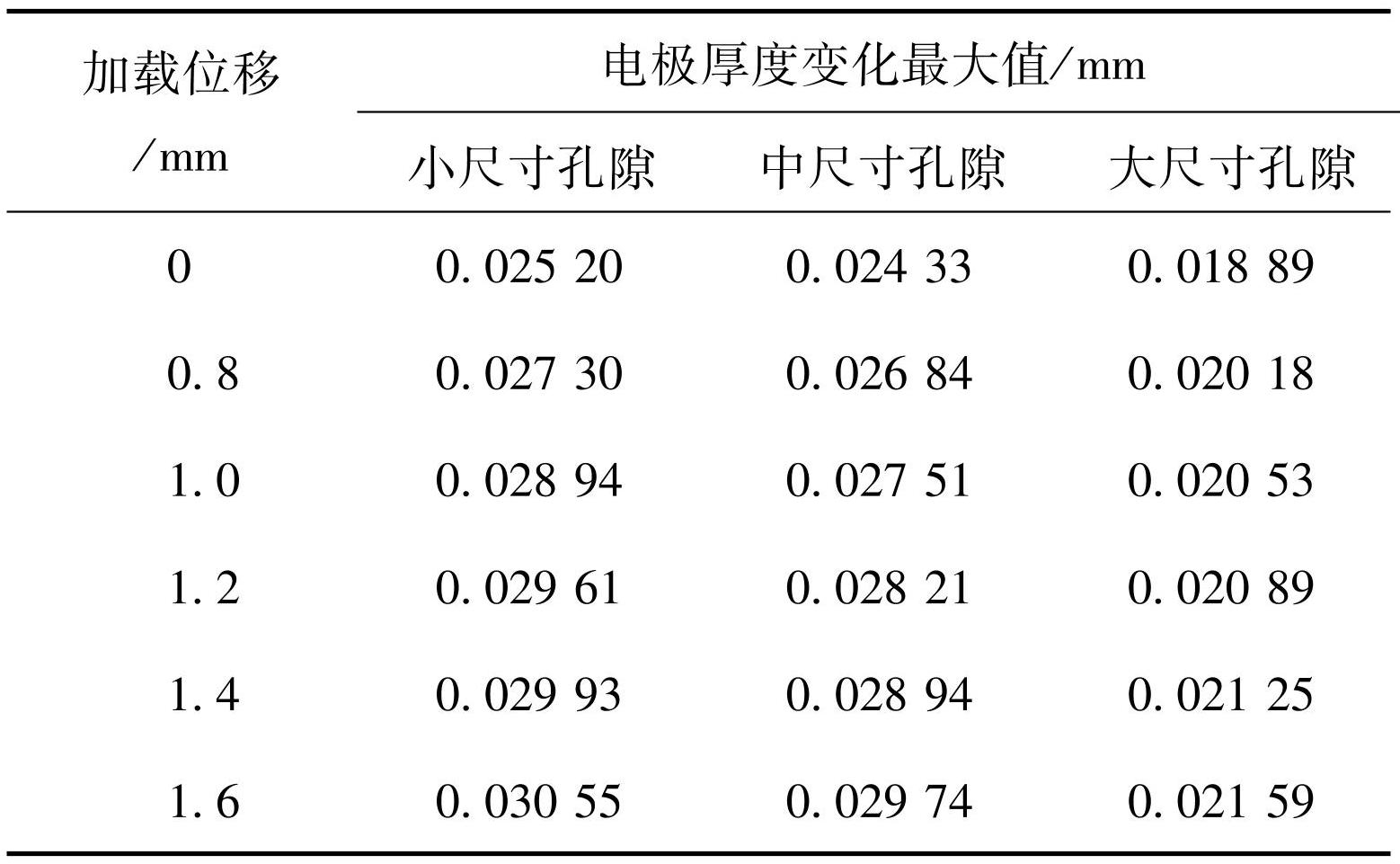
为了量化加载位移对电极厚度变化的影响,以未加载时电极腐蚀厚度为基准,计算加载条件下电极腐蚀厚度增加百分比,从图8可以看出,3种孔隙下,电极腐蚀厚度均随加载水平增加而增加,应力与电化学腐蚀耦合在一起,显著影响了电化学腐蚀速率和最终的电极腐蚀厚度。
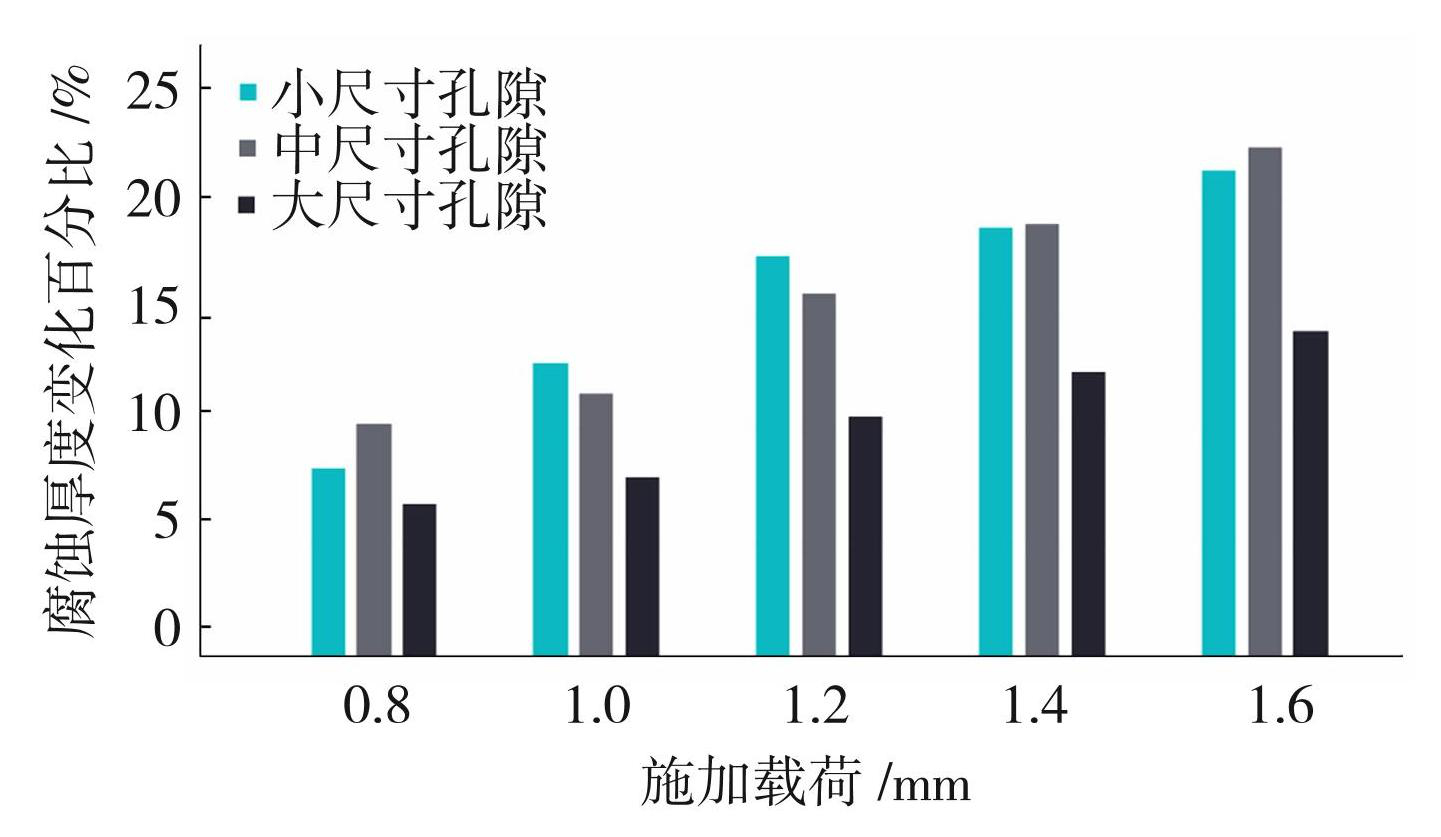
图8载荷水平及孔隙对多孔Ti-6Al-4V合金腐蚀厚度影响
Fig.8Influence of load level and porosity on corrosion thickness of porous Ti-6Al-4V alloy
3 结论
1)基于应力腐蚀理论,将由孔隙特性引发的结构应力耦合到电极反应的平衡电位和交换电流密度表达式,建立了腐蚀电场的力学-电化学耦合有限元模型。
2)随载荷增大,应力集中较为明显的孔隙边缘区域腐蚀更为剧烈,最大腐蚀厚度均出现在孔梁边缘处。随应力水平提高,腐蚀电流密度逐渐升高,与无应力试样相比,超过屈服应力试样的5年腐蚀厚度增加了22%。
3)比较了3种孔隙尺寸下电极5年腐蚀厚度,随着孔隙的增大,电极腐蚀厚度逐渐减小,大孔应力腐蚀速率低于小孔。