摘要
为了研究粉末冶金工艺和石墨烯对纯铝力学性能和耐腐蚀性能的影响,以铝粉和氧化石墨烯粉末为原材料,采用粉末冶金工艺,制备了石墨烯铝基复合材料杆材和粉末冶金纯铝杆材,并采用相同挤压工艺获得了熔融铸造纯铝杆材,开展了3种材料的力学性能、电学性能和中性盐雾腐蚀性能研究。利用金相显微镜(OM)、扫描电子显微镜(SEM)、透射电镜(TEM)、能谱(EDS)和重量变化等手段分析了3种材料的微观组织与腐蚀产物。结果表明,粉末冶金工艺能将纯铝材料的拉伸强度提高17.2%,同时保持电阻率几乎不变;0.5%含量石墨烯可使纯铝拉伸强度提高42.5%,且电阻率仅增大1.4%。在中性盐雾环境下,铸造纯铝的腐蚀速率略高于粉末冶金纯铝,石墨烯铝基复合材料和粉末冶金纯铝的腐蚀速率相当。石墨烯可有效提高纯铝力学性能,同时不明显降低其电阻率和耐腐蚀性能。
Abstract
In order to study the influence of powder metallurgy process and graphene on the mechanical properties and corrosion resistance of pure aluminum matrix, the graphene aluminum matrix composite rod and powder metallurgy pure aluminum rod were prepared by powder metallurgy process using aluminum powder and GO powder as raw materials. Additionally, the melt casting pure aluminum rod was obtained by using the same extrusion process. The mechanical properties, electrical properties and neutral salt spray corrosion properties of the three materials were studied. The microstructure and corrosion products of the three materials were analyzed by means of optical microscopy (OM), scanning electron microscopy (SEM), transmission electron microscopy (TEM), energy-dispersive X-ray spectroscopy (EDS) and weight change analysis. The results show that the tensile strength of pure aluminum can be increased by 17.2% by powder metallurgy, while the electrical resistivity remains almost unchanged. The tensile strength of pure aluminum increased by 42.5% with the addition of 0.5% graphene content and the electrical resistivity increased by only 1.4%. In the neutral salt spray environment, the corrosion rate of cast pure aluminum is slightly higher than that of powder metallurgy pure aluminum, while the corrosion rate of graphene aluminum matrix composite and powder metallurgy pure aluminum are comparable. Graphene can effectively improve the mechanical properties of pure aluminum without significantly compromising its electrical resistivity and corrosion resistance.
铝合金具有密度低、比强度高、导电导热能力强、加工成型性好以及高的性价比等优势,正在迅速成为电缆市场中的一股新力量[1-2]。但导线力学性能和电学性能的匹配性问题一直制约着铝导线的发展:纯铝导线的导电率相对较高,但导线强度较低;铝合金导线强度满足使用要求,但导电率略低。石墨烯是一种新型二维碳材料,具有极低的电阻率(10 nΩ·m)和极高的强度(130 GPa)[3]。大量研究表明[4-8]:通过在铝基体中添加石墨烯可以将材料的拉伸强度提高50%以上,有望满足高压输电线对高强度铝合金导线的迫切需求。在正常自然条件下,铝合金表面具有较强的耐蚀性[9],但在实际使用过程中,铝合金的局部腐蚀现象往往很严重[10-11],对于不同形式的局部腐蚀其过程和机理也存在较大差异。铝及其合金大气腐蚀主要是材料受到大气中所含水分、氧气和腐蚀性介质的联合作用而引起的电化学破坏,是电化学腐蚀的一种特殊形式。国内外的研究学者对多种铝合金的大气腐蚀作了广泛的研究,但对石墨烯铝基复合材料的腐蚀实验研究报道较少,Xie等[12]发现石墨烯可阻碍盐雾腐蚀时Cl-离子对Al基体的侵入,从而提高复合材料的耐腐蚀性能;Zhang等[13]发现石墨烯的加入可将ADC12铝合金的极化电阻提高66%;Khezerlou等[14]发现当石墨烯含量为0.5%时,石墨烯铝复合材料具备最佳的耐腐蚀性能。粉末冶金是制备石墨烯铝基复合材料的重要方法,但是尚无石墨烯和粉末合金工艺共同对铝基体腐蚀性能的影响研究。
本文采用粉末冶金的方法制备了石墨烯铝基复合材料杆材,并与粉末冶金法制备的纯铝杆和熔融铸造法制备的纯铝杆进行了性能对比,分析了石墨烯的加入对材料力学性能、电学性能和腐蚀性能的影响,对材料的微观组织、石墨烯分布情况和腐蚀情况进行了表征分析。
1 实验
实验原材料为铝锭(纯度99.7%)和hummer法制备的氧化石墨烯粉末[15]。首先采用氮气雾化的方法将铝锭加工为纯铝粉,筛分后粒度为200~400目。随后将一定质量的氧化石墨烯粉末在无水乙醇中超声30 min,然后加入纯铝粉,在水浴锅中保持60℃,并不断搅拌,待无水乙醇基本挥发后,放入真空烘箱80℃烘干24 h。烘干后的混合粉末于480℃、120 MPa条件下热等静压2 h,获得致密的复合材料锭坯,锭坯在400℃热挤压(挤压比81∶1)为直径10 mm的杆材。作为对照,以纯铝粉为原料,采用相同的方法制备了粉末冶金纯铝杆,将普通铝锭经相同挤压工艺得到了铸造纯铝杆,样品编号和制备方法如表1所示。
表1样品编号和制备方法
Table1Sample number and preparation method
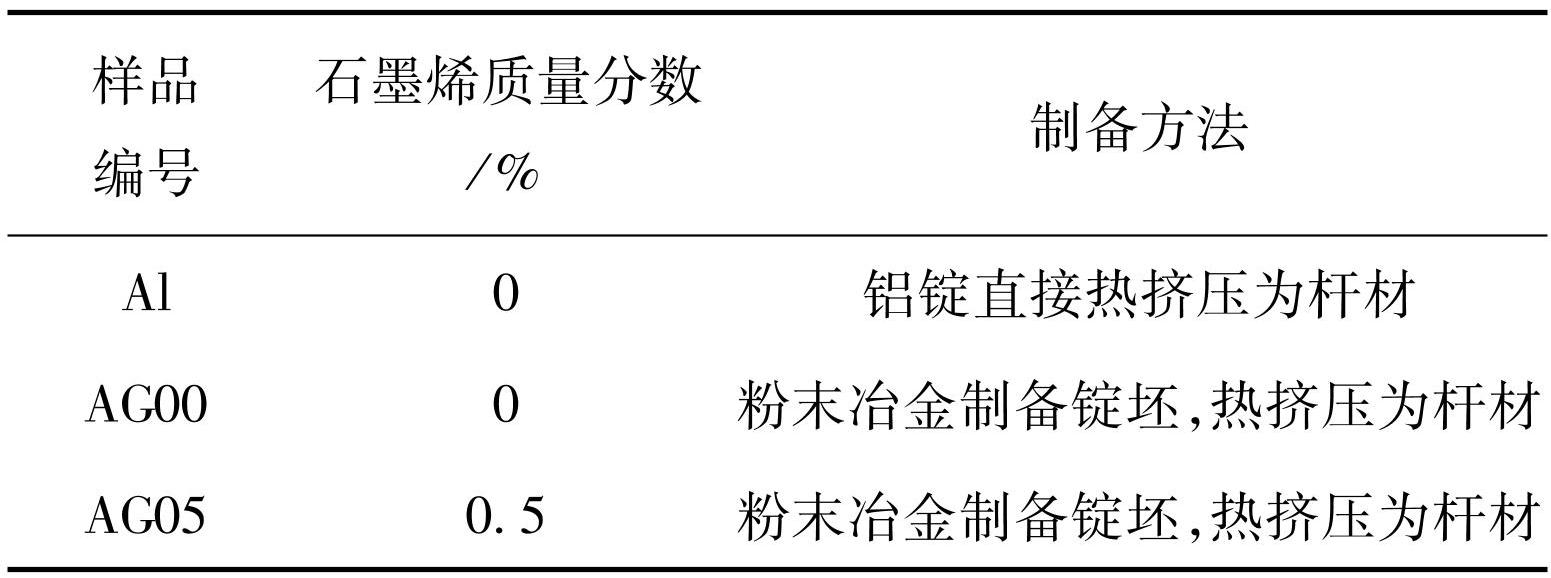
力学性能测试按照国标《GB/T4909.3—2009裸电线试验方法第3部分:拉力试验》进行,拉伸性能测试样品尺寸为Φ10 mm×250 mm,标距长度100 mm,拉伸速率25 mm/min;电学性能测试按照国标《GB/T3048.2—2007第2部分:金属材料电阻率试验》进行,电学性能测试样品尺寸为Φ10 mm×1 500 mm,测试温度为(20±1)℃,样品在房间中恒温4 h再进行测试;每个样品均测试3个试样,实验结果取平均值。中性盐雾腐蚀实验按照国家标准GB/T10125—2012《人造气氛腐蚀试验盐雾试验》进行,腐蚀性能测试样品尺寸为Φ10 mm×100 mm,实验温度为(35±2)℃,采用质量浓度为(50±5)g/L的NaCl溶液,溶液的pH范围在6.5~7.2,盐雾的沉降率为(1.5±0.5)mL/(80 cm2·h);中性盐雾腐蚀实验的试验周期设为24、48、96和168 h;测试结束后将样品用低于40℃的流动去离子水清洗,以去除试样表面残留的盐雾溶液,在距离试样300 mm处用不超过200 kPa的空气立即吹干,随后用电子天平进行称重,并与腐蚀前的试样重量进行比较,用精度为0.1 mg的电子天平测量试样质量。采用扫描电镜(SEM,JEOL JSM-7001F)观察石墨烯在铝粉表面的分散情况、杆材样品表面形貌和拉伸断口;采用金相显微镜(DM4M)观察杆材样品微观组织;采用透射电镜(TEM,FEI F20)观察杆材样品中的石墨烯分布情况。
2 实验结果
2.1 氧化石墨烯在铝粉中分散
实验采用的纯铝粉末形貌如图1(a)所示,为典型气雾化球形粉末,在大颗粒粉末周围存在数量众多的小尺寸粉末,其中大颗粒尺寸约20~50 μm,小颗粒尺寸约 5~10 μm。hummer法制备的氧化石墨烯粉末呈片状,如图1(b)所示,片径在几百微米。在无水乙醇中分散、干燥后,氧化石墨烯片层附着于铝粉末表面,如图1(c)所示,其中氧化石墨烯片径明显小于铝粉末直径,这是因为在无水乙醇中分散时,氧化石墨烯粉末被超声波破碎为小片径粉末,从而利于氧化石墨烯在铝粉表面的均匀分散。
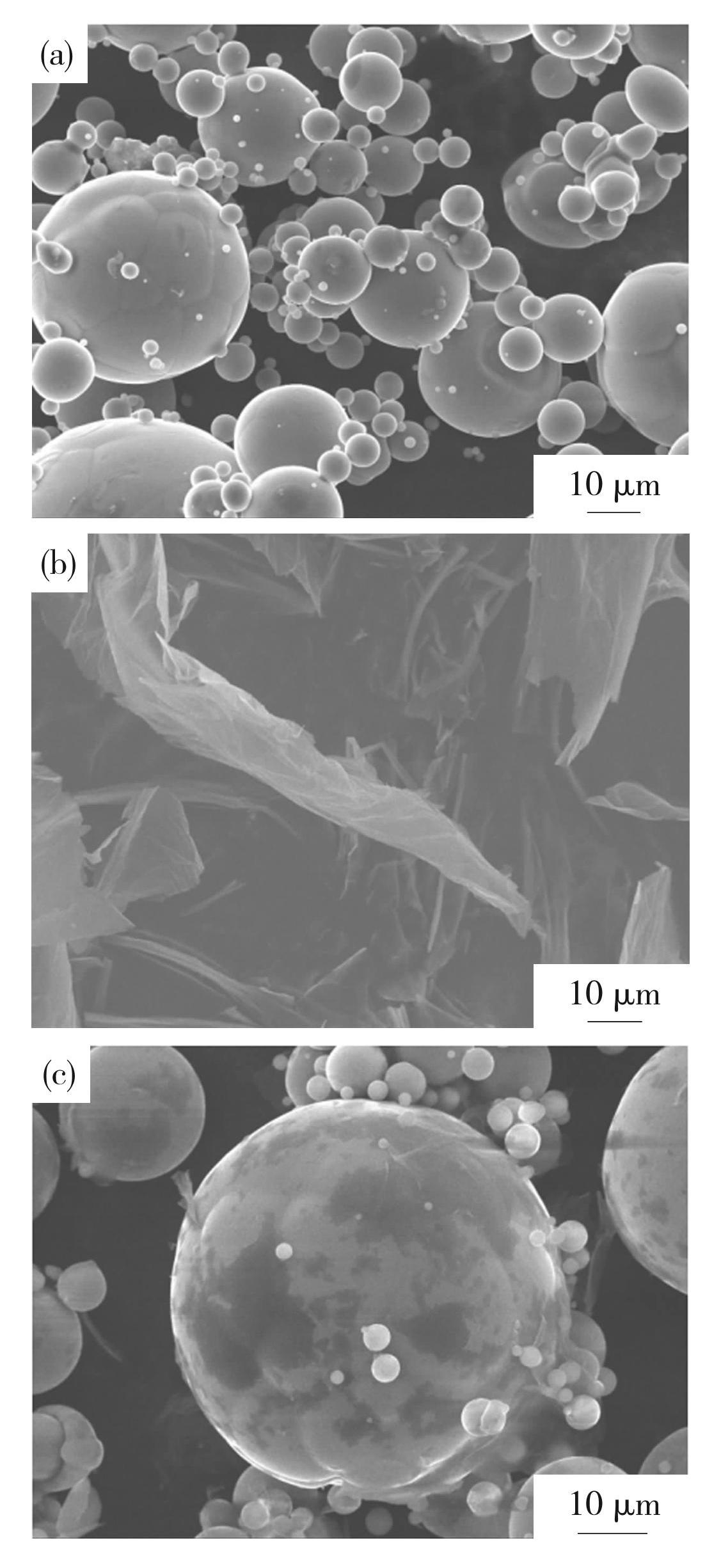
图1原始铝粉末(a)、原始氧化石墨烯粉末(b)和氧化石墨烯/铝混合粉末(c)的SEM图
Fig.1SEM images of (a) raw aluminum powder, (b) raw graphene oxide powder and (c) GO/Al mixed powder
2.2 力学性能和电阻率
挤压获得的3种Φ10 mm样品的密度均为2.69 g/cm3,说明采用热等静压+热挤压的工艺路线,制备了近乎全致密的粉末冶金纯铝杆和石墨烯铝基复合材料杆材,对3种样品进行力学性能和电学性能测试,结果如表2和图2所示。铸造铝杆(Al)的拉伸强度最低,仅有87 MPa;粉末冶金纯铝杆(AG00)的拉伸强度为102 MPa,相比于铸造铝杆提高17.2%;石墨烯铝基复合材料(AG05)拉伸强度达到124 MPa,相比于铸造铝杆提高42.5%,石墨烯表现出了良好的增强效果。断裂延伸率则表现出相反的趋势,粉末冶金纯铝杆的断裂伸长率(45.2%)相比于铸造铝杆(52%)略有降低,而石墨烯铝基复合材料的断裂伸长率(26.7%)相比于铸造铝杆降了48.6%。
在电阻率方面,粉末冶金铝杆(27.91 nΩ·m)和石墨烯铝基复合材料(28.30 nΩ·m)相比于铸造铝杆(27.86 nΩ·m)均有所增大,但幅度分别为0.2%和1.4%,说明粉末冶金工艺对电阻率的影响非常小,而石墨烯的加入会略微增大材料的电阻率。
表2样品的力学性能和电学性能
Table2Mechanics and electrical performance of samples
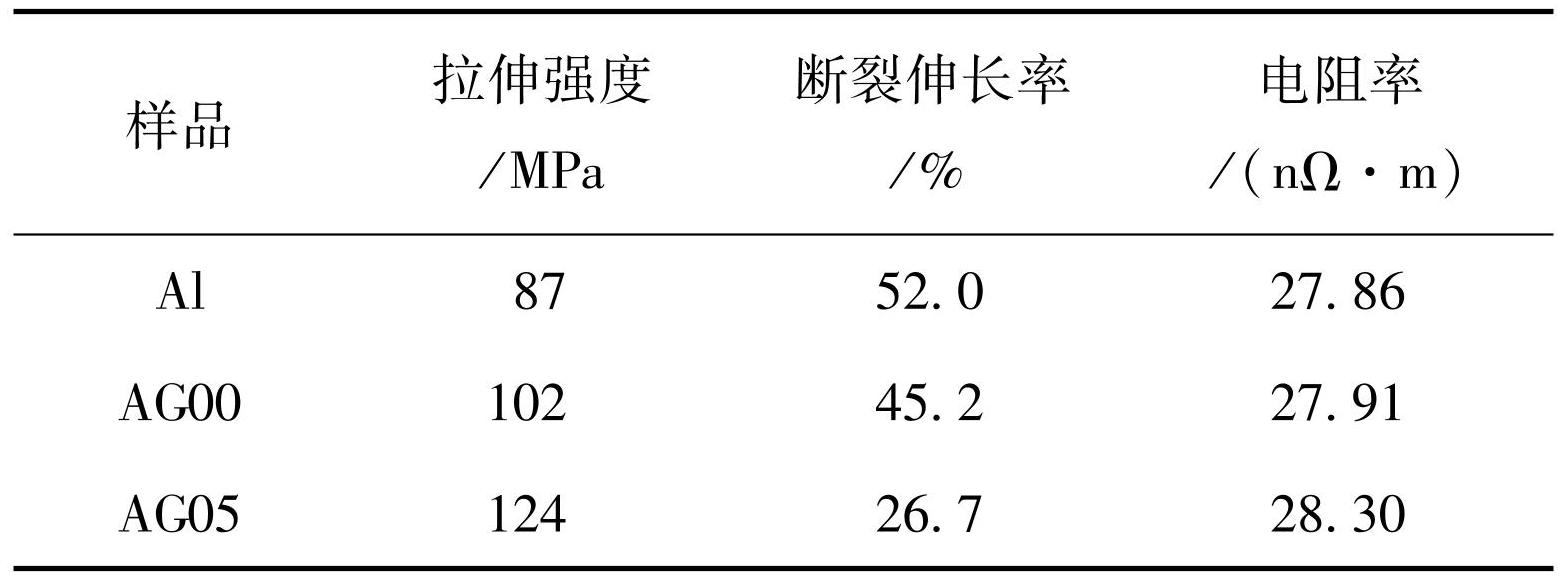
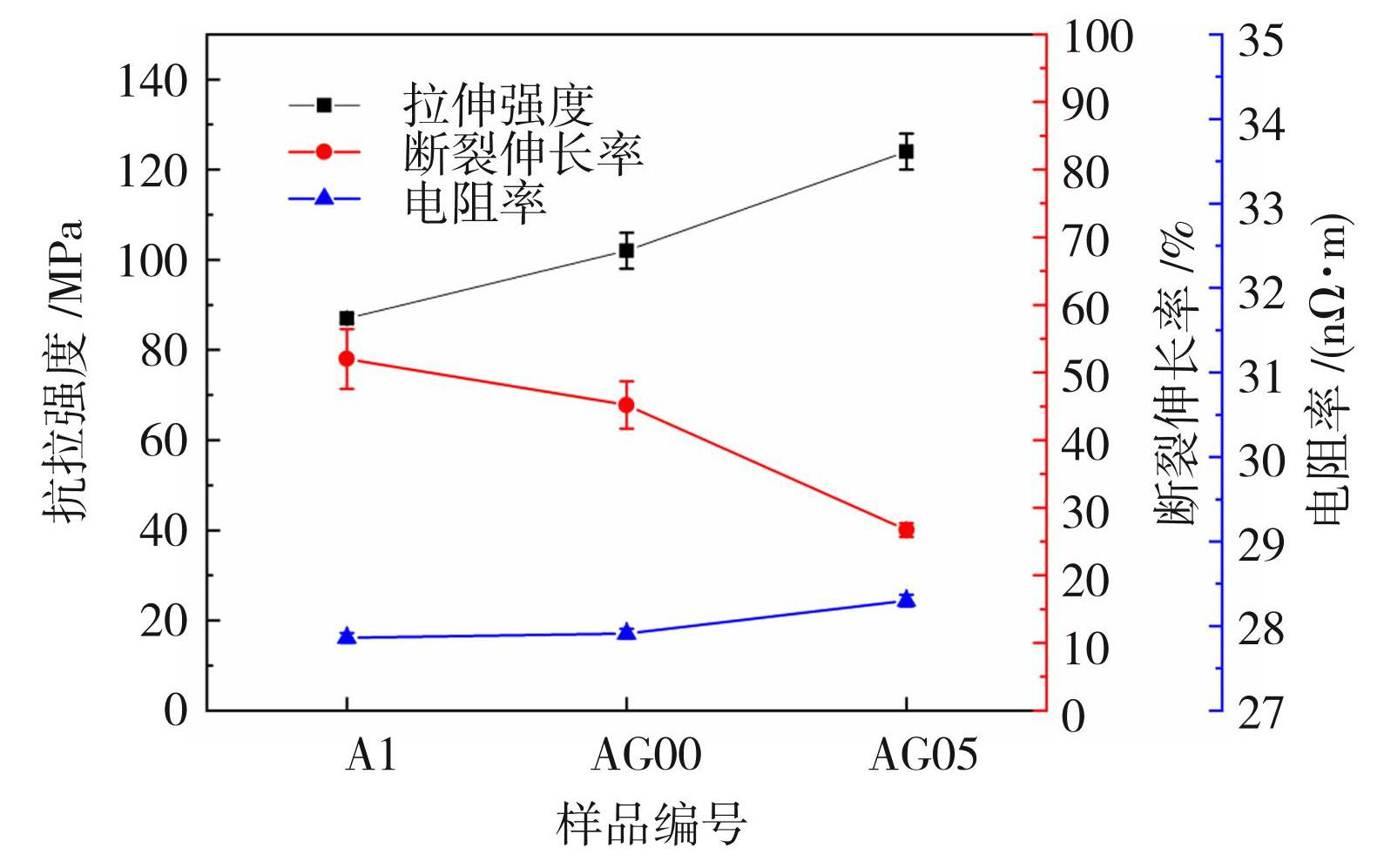
图2样品的力学性能和电学性能对比曲线
Fig.2Comparison curves of mechanical and electrical properties of samples
2.3 腐蚀性能
3 种样品腐蚀增重随腐蚀时间变化曲线如图3所示。可以看到,随盐雾腐蚀时间的延长,试样质量均逐渐增大,说明3种样品腐蚀程度均与腐蚀时间正相关;通过质量变化曲线可知,相同腐蚀时间条件下,铸造纯铝(Al)的增重最明显,粉末冶金材料AG00和AG05较为接近,说明粉末冶金纯铝和石墨烯铝基复合材料的耐腐性能均优于铸造纯铝。
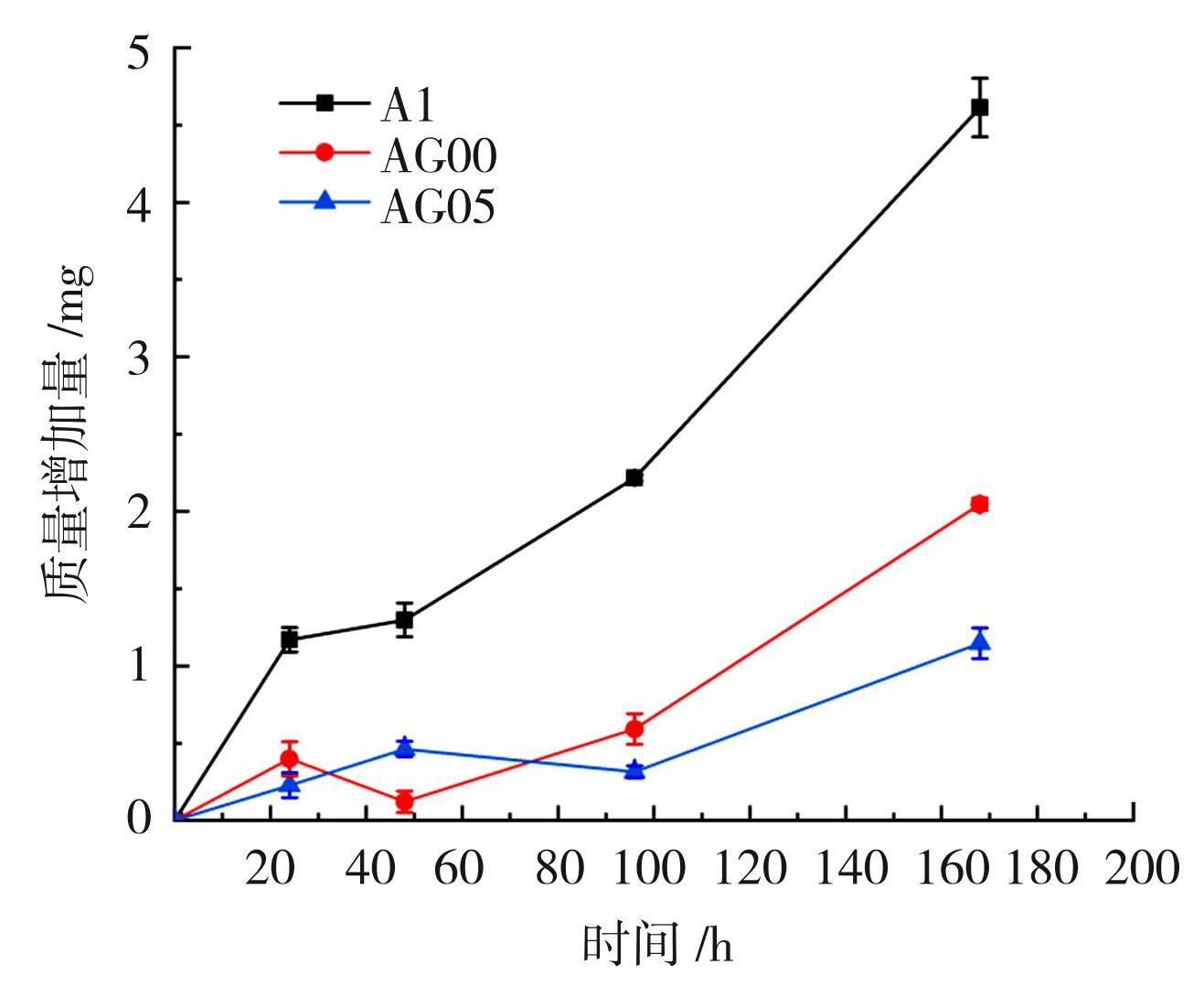
图3样品在不同盐雾腐蚀时间下的质量增加曲线
Fig.3Sample mass increase curves under different corrosion time of salt spray
进一步分析3种材料的腐蚀速率变化规律,即单位时间、单位面积上质量的变化,结果如图4所示,可见3种材料的腐蚀速率Al>AG00≈AG05。3种样品的盐雾腐蚀初期都是一个加速腐蚀的过程,具有相对较高的腐蚀速率,随后腐蚀速率逐渐放缓,腐蚀至96 h时,腐蚀速率降至最低,腐蚀至168 h时腐蚀速率再次略微升高,此时腐蚀是活性阴离子的竞争吸附使氧化膜逐渐溶解,裸露出来的铝合金基体与第二相形成局部腐蚀电池的结果[16-17]。
3 种样品平行于挤压方向的金相组织如图5所示,可以看到铸造纯铝(Al)样品组织十分干净,且无织构;而粉末冶金纯铝(AG00)样品表面存在较多细小黑点,为粉末冶金中常见组织[18]。而石墨烯铝基复合材料(AG05)中还存在少量黑色颗粒(图5(c)画圈处),为材料中添加的石墨烯粉末,且在挤压变形过程中,部分石墨烯粉末聚集成了长条形结构,使石墨烯铝基复合材料表现出了一定的挤压织构。
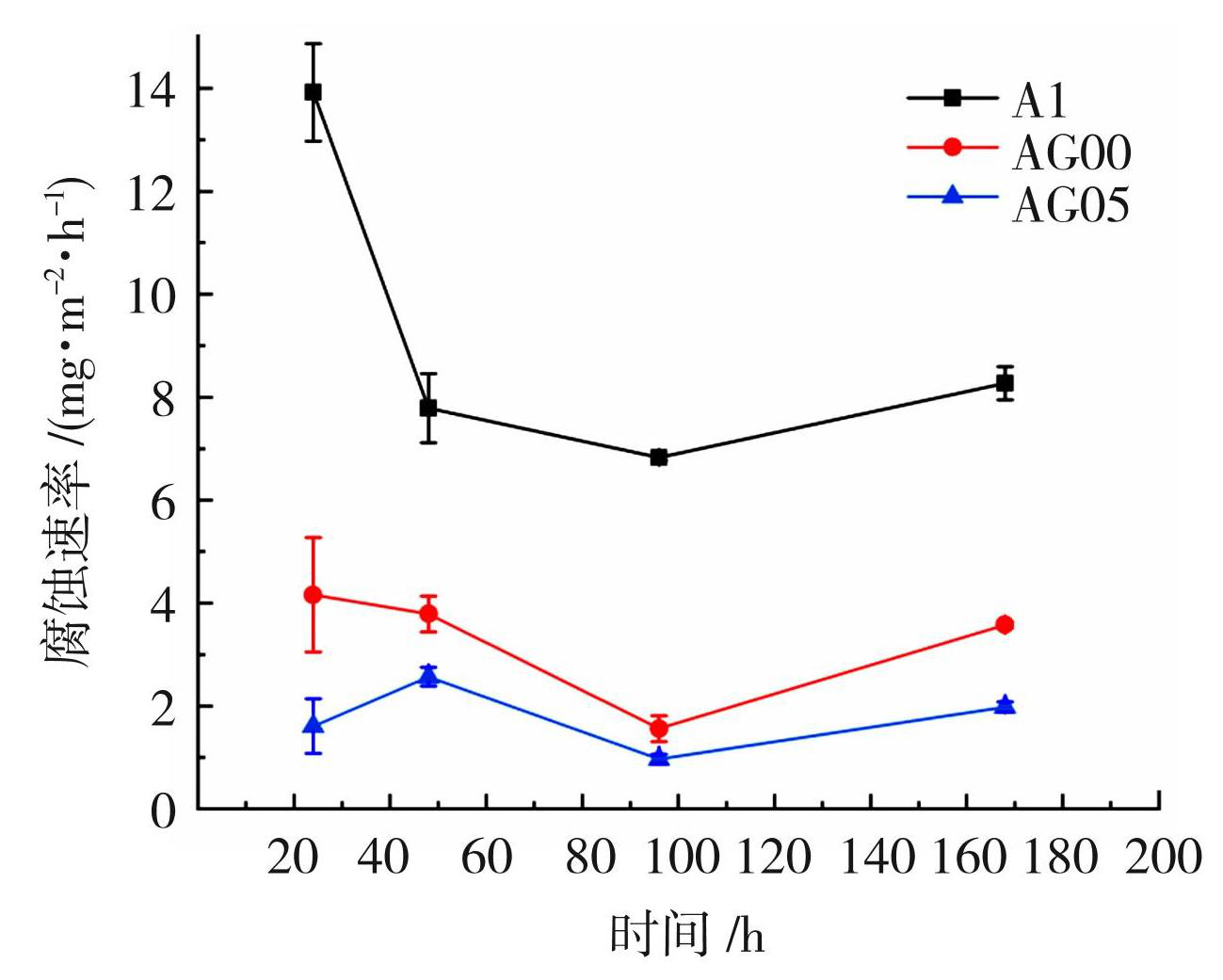
图4试样在不同盐雾时间下的腐蚀速率变化曲线
Fig.4Corrosion rate curve of samples under different salt spray time

图53种样品的微观金相组织
Fig.5OM images of samples: (a) Al; (b) AG00; (c) AG05
3 分析讨论
3.1 石墨烯在铝基中的分布
为分析石墨烯在铝基复合材料中的分布情况,对AG05样品进行了透射电镜分析,结果如图6所示,图中箭头标出了石墨烯的在铝基复合材料中的位置,可以看到其主要存在于铝晶粒间,且石墨烯与铝基体间紧密结合,无明显的孔洞等缺陷。
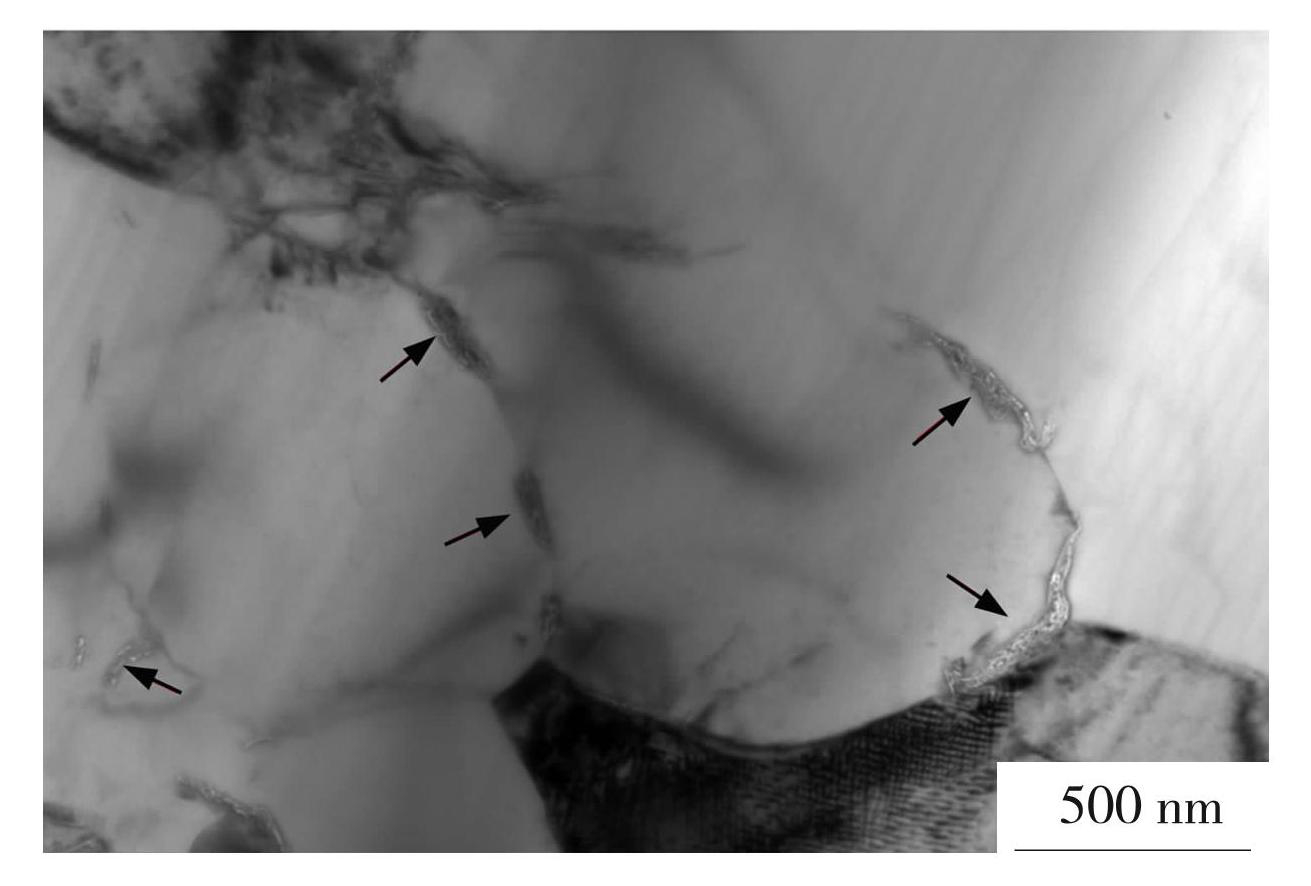
图6AG05样品的TEM图片
Fig.6TEM image of AG05
同时,石墨烯和铝基体界面处未形成明显的碳化物相[19]。说明采用热等静压+热挤压的方式实现了石墨烯铝基复合材料的致密成形,且由于成形温度较低,石墨烯和铝基体的反应速率较慢,有效避免了石墨烯与铝基体的化学反应。
3.2 杆材拉伸断口分析
Al、AG00和AG05 3种试样拉伸断口形貌如图7所示,其中Al和AG00样品的断口中存在大而深的韧窝,说明两种材料具备良好的塑性,与拉伸性能结果一致。而AG05样品断口中的韧窝相对细小,且在韧窝中存在薄片状物质,EDS能谱分析结果表明,其主要为C,说明该薄片物质为石墨烯。
3.3 杆材表面腐蚀产物分析
图8是Al、AG00和AG05 3种试样在腐蚀时间0、48、168 h条件下的腐蚀形貌SEM图。经盐雾实验后,试样表面均出现了不规则的块状物,随着腐蚀时间的增长,这种腐蚀产物逐渐增多增厚。48 h时的腐蚀产物较为疏松,这种结构可以为氧气提供更多的通道,促进腐蚀的进行。随后,腐蚀产物逐渐变得致密,氧通道逐渐减少,致使腐蚀速率逐渐变慢,最后在试样表面形成一层致密的氧化铝保护层[17]。
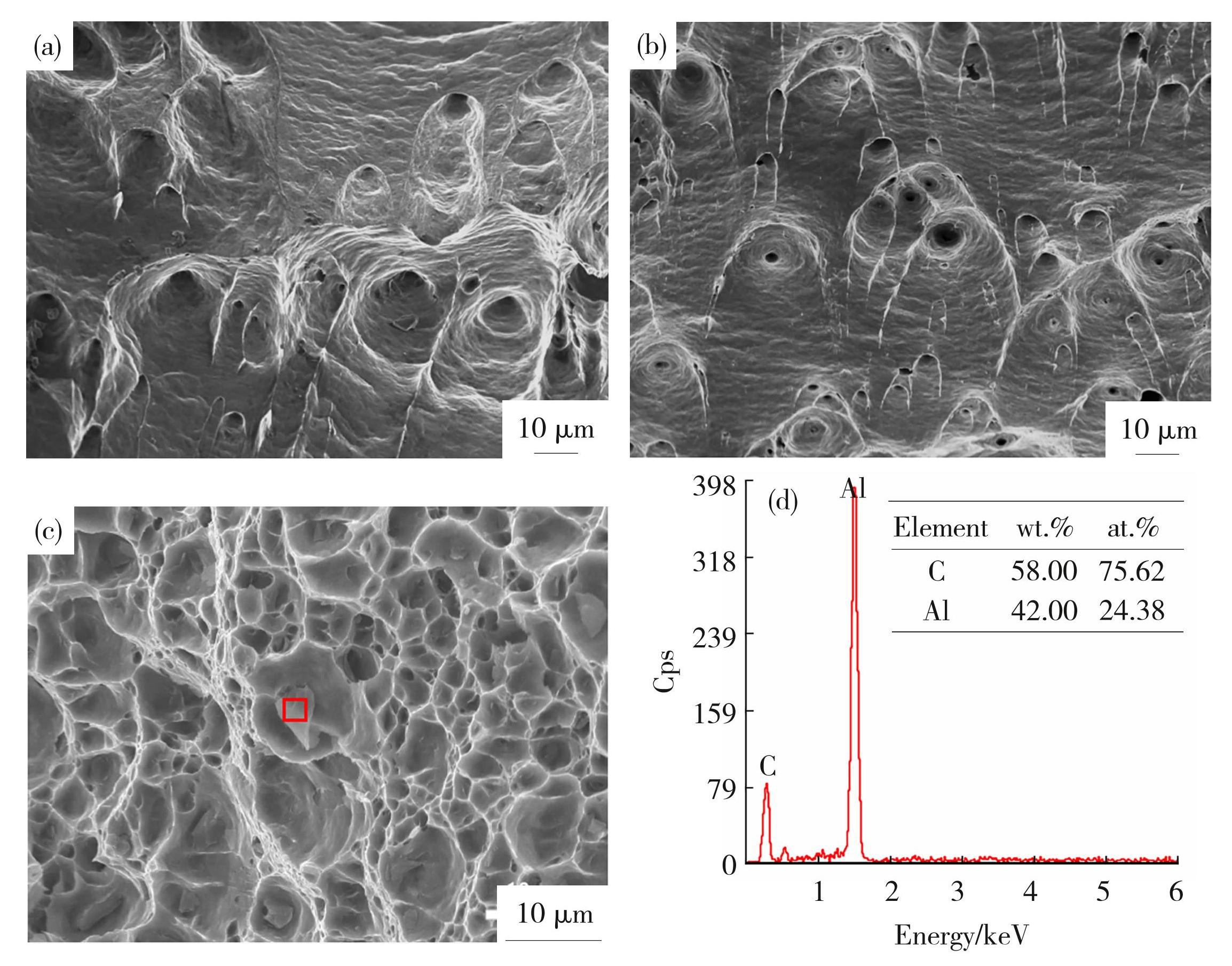
图7 (a)Al、(b)AG00、(c)AG05样品拉伸断口SEM图片,(d)图7(c)中方框位置的EDS能谱分析结果
Fig.7SEM images of Tensile fracture of (a) Al, (b) AG00 and (c) AG05, (d) EDS spectrum of Fig.7 (c) at the box position
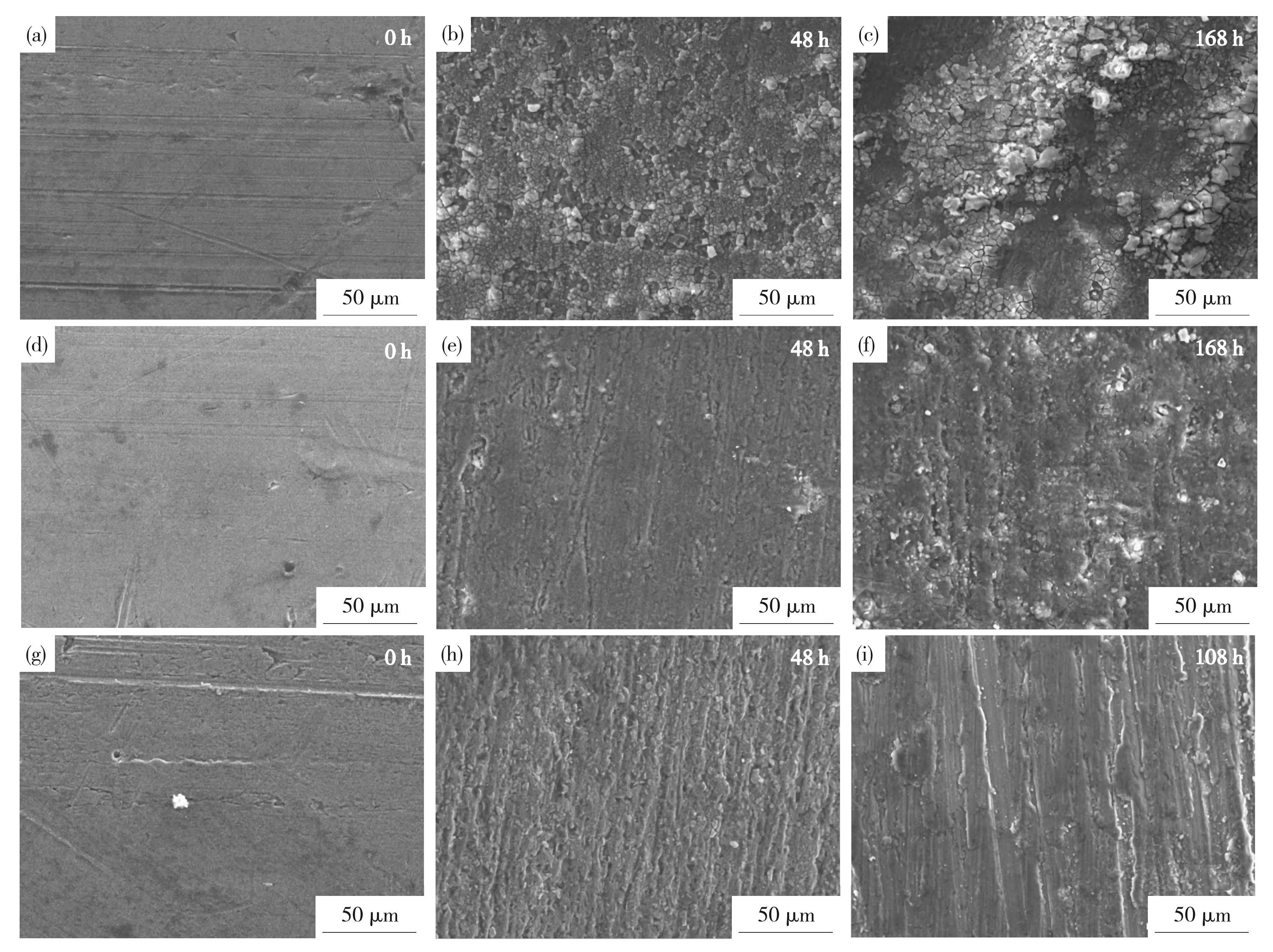
图8不同时间中性盐雾实验后3种试样腐蚀形貌SEM照片
Fig.8SEM images of corrosion samples: (a) , (b) , (c) Al; (d) , (e) , (f) AG00; (g) , (h) , (i) AG05
随着腐蚀的不断进行,试样表面逐渐出现腐蚀点(坑),随腐蚀时间的延长,腐蚀点(坑)的数量和尺寸均明显增加,试样的腐蚀程度增大,在腐蚀168 h后,3种试样表面的腐蚀点(坑)连成条状,方向与样品挤压加工痕迹一致[20]。铝合金在中性条件下的腐蚀行为的阳极反应和阴极反应如下[17]:
铝及其合金腐蚀产物的形成过程为:氧化膜外层转变为一薄层γ-AlOOH,然后,在γ-AlOOH上又会覆盖上一层A1(OH)3(也可写成A12O3·3H2O),由此可推断试样表面腐蚀产物为氢氧化铝。通过表面形貌比对,3种材料的腐蚀速度为:Al的腐蚀速度最快,在24 h时表面就出现大量的腐蚀产物,腐蚀程度较高,168 h表面的腐蚀点数量较多。其次是AG00材料,腐蚀程度最小的是AG05,该结果与2.3节腐蚀增重结果一致。
Judge[21]提出,铝的铸造和粉末冶金工艺对材料耐腐蚀性的影响主要体现在材料的致密度上,致密度高,对应材料耐蚀性能好。但2.2节对Al、AG00、AG05 3种材料的密度测试结果均为2.69 g/cm3,说明导致两种工艺试样耐腐蚀性能差别的因素不只是致密度。不同工艺下材料的表面形貌是有细微差别的,由于铸造纯铝硬度相对较低,使得其在加工过程中,表面更易受到损伤,表现为铸造纯铝试样表面划痕更深,如图8(a)所示。腐蚀性介质就容易积存在这些缝隙中,并渗透到里层,加剧材料的腐蚀。因而表现出铸造纯铝较粉末冶金纯铝更易腐蚀的现象。
根据传统腐蚀理论,石墨烯和铝存在电位差,石墨烯的引入会在铝基体内部形成原电池,从而加速铝材料的腐蚀。但石墨烯具有独特的二维结构,其片层能在铝基体表面和内部形成网络结构,能够有效阻止氧气和水分子等腐蚀因子,建立起“迷宫式”的物理屏障作用,延缓金属的腐蚀速率,能在一定程度上提高金属的耐腐蚀性能[22-24]。正是由于石墨烯独特的二维结构,对水分子、氧分子等腐蚀因子产生阻隔作用,弥补石墨烯与铝的电位差所产生的腐蚀作用,最终表现为石墨烯铝基复合材料与粉末冶金纯铝的耐腐蚀性能相当。
4 结论
1)粉末冶金工艺能使纯铝的拉伸强度提高17.2%,同时电阻率基本不变;添加0.5%石墨烯后,复合材料的拉伸强度相比于铸造纯铝提高42.5%,且电阻率无明显降低。
2)中性盐雾条件下,铸造纯铝的耐腐蚀性能略低于粉末冶金纯铝,是由于挤压变形过程中,铸造纯铝硬度较低、表面的划痕更深,使得腐蚀性盐雾在缝隙处易聚集,降低了其耐蚀性能。石墨烯的加入未对复合材料的腐蚀速率产生明显影响,是因为石墨烯在金属基体中形成了网络结构,能阻碍腐蚀介质的渗入,从而抵消电化学加速腐蚀的效果。