摘要
为研究复合管热轧过程中的应力变化规律及复合管变形规律,本文以六机架热连轧316L/20复合管为例,采用理论分析结合有限元模拟的方法,获得了变形过程中双层金属的壁厚与等效应力分布情况。按照理论计算所得工艺参数进行轧制实验,并对经轧制实验轧出的复合管进行拉剪实验和夹持实验,同时对轧制试样界面结合处进行了晶间腐蚀和微观组织观察。力学性能实验结果显示,轧制试样结合面层间剪切强度达到445 MPa,所能承受的最大剪切应力远大于国标要求。微观组织观察显示,金属间界面结合良好,且在界面处形成明显的过渡层,未发现晶间腐蚀裂纹。研究表明,轧后复合管双层金属壁厚分布均匀,结合情况良好,验证了本文轧制模型工艺参数的合理性。
Abstract
In order to study the stress variation and deformation pattern of 316L/20 composite pipe during hot rolling, theoretical analysis combined with finite element simulation method is used in this paper. Taking 316L/20 composite pipe for six-stand hot rolling as an example, the distribution of wall thickness and equivalent stress of the bilayer metal during deformation are obtained. Rolling experiments are carried out according to the calculated process parameters, followed by tension-shear tests and clamping test on the rolled composite pipes. Additionally, intergranular corrosion and microstructure observations are performed at the interface of the rolled samples. The test results show that the interlaminar shear strength at the interface of the rolled samples reaches 445 MPa, which exceeds the maximum shear stress required by the national standard. Microstructure observations reveal that the intermetallic interface is well bonded with a clear transition layer formed at the interface. No intergranular corrosion crack is found. The study confirms that the wall thickness of the double-layer metal is well distributed and the combination is good, which validates the rationality of the process parameters in the rolling model proposed in this study.
双金属复合管可以在各种苛刻的条件下使用[1],最重要的原因是,其内外层材料都可以根据不同的工作环境来调节,且不局限于一种或者两种材料[2]。由两种不同金属材料组成的复合管可以将两种材料的优点同时发挥出来[3]。并且双金属复合管用作油气输送管道,需求量很大[4],市场需求促使国内龙头企业大力发展双金属复合管,并在工业前线得到了应用[5]。而复合管在轧制过程中可能存在壁厚不均匀、管材断裂和表面质量差等问题,轧得的管材质量不合格,直接报废,造成大量损失。国内学者对上述问题提出了不同的解决方案。
南京理工大学提出一种双金属油气复合管X65/2205的制备方法,可提高复合管综合性能[6]。江阴华润制钢有限公司公开了一种双金属复合管的连轧方法,生产出内外表面质量较好的双金属复合管[7]。江苏金鹰绝缘管业有限公司发明了一种耐磨耐腐蚀双金属复合管制备装置及其方法,这种边挤压边预热的方式让内衬管可以连续局部快速塑性变形,从而与外管道的内壁贴合[8]。寇永乐等[9]开发了适合基管直径为114~660 mm的双金属复合管自动穿管机组。王冬林等[10]对双金属复合管直度不合格现象进行了理化分析,在合理选用基管及优化水压工艺后,双金属复合管复合效果得到极大改善。刘建彬等[11]从理论上分析和研究了双金属冶金复合管在弹性和弹塑性状态下内压力与内外层金属壁厚、强度的对应关系。王于金等[12]研究分析了典型双金属复合辊和复合管离心铸造工艺特点与成形规律,探查工艺参数对结合界面与结合性能的影响规律,揭示了双金属复合管的离心铸造过程中的组织演变机理。彭威等[13]将直接挤压和扩径剪切变形工艺相结合来制备具有良好性能的Mg/Al双金属管材,并探究挤压温度对Mg/Al复合管材成形过程的影响,得到的Mg/Al双金属复合管材结合良好,结合界面无缺陷和裂纹。
复合管轧制工艺研究理论逐渐成熟,但对复合层的结合性能与强度研究较少。本文对复合管连轧过程中各种关键参数进行设计计算,并采用有限元模型进行分析,对内侧金属与外层金属以及层间应力进行分析,获得变化规律。通过各种实验研究来分析其结合情况,检验是否满足工业要求,本研究对双金属结合层性能研究具有实际意义。
1 参数计算
本文将采用六机架连轧模型,模拟轧制后的复合管,探究其影响成形的参数,对其关键参数进行分析,并给出具体的设计思路和方法。
1.1 变形量分配
针对6道次的分配原则考虑各机架的变形量。
1)全部机架分为两部分,前四机架为承受大减径量道次,因此,采用较大的减径量;后两个机架采用较小的减径量,预算连轧过程总的减径量,依次分配给6个道次,且单个道次的延伸系数不超过1.5。
2)根据管材连轧过程的变形量分配减径率,单号第1、第3、第5机架的减壁量之和与双号第2、第4与第6机架的减壁量之和相等,且等于钢管轧制过程总的减壁量。
3)总延伸率为每一道次延伸率之积。
假设复合管连轧来料外层金属外径为d0、双层金属的初始壁厚之和为s0,sw为初始外层管的壁厚,sn为内层管的初始壁厚,则
(1)
令双金属管经六机架轧制成形后的复合管外径为d(型槽底处)、复合管总壁厚为s,芯棒直径为dm,则芯棒直径为(图1所示)
(2)
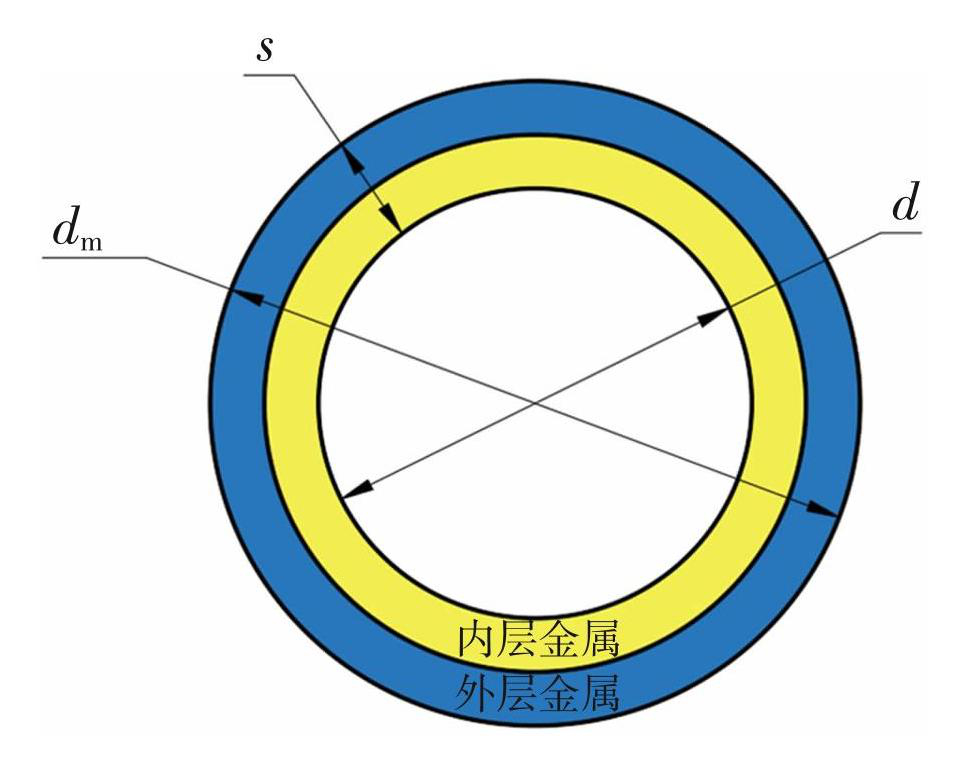
图1轧后复合管的尺寸
Fig.1Dimensions of rolled composite pipes
连轧过程总对数减径率(γ)为[14]
(3)
各机架减径率(γi)为
(4)
式中η为经验系数,此处η的取值范围为2~6。
连轧过程复合管的总减壁量(Δs)为
(5)
各机架的减壁量
(6)
各机架辊缝处复合管壁厚
(7)
式中:κi为各机架的减壁率;Si-1为前一机架辊底处复合管壁厚值(S0=S1=s0),mm。
根据管材连轧过程的变形量分配和机架排列顺序,各机架减壁量关系为
(8)
1.2 孔型设计
连轧孔型的适配性直接影响到复合管成型的精度,不仅是对复合管材外径精度的影响,对管材横截面的双层壁厚均匀性影响更为重要。在设计孔型之前需要先确定轧制表,依据管材参数进行孔型设计,在设计过程中重点要考虑总减径率、总减壁率和总延伸率3个参数。
本文的孔型选择扩展椭圆-圆形相结合,便于金属周向流动,使得双层壁厚具有较高的横向精度。前四机架采用带圆弧侧壁的椭圆孔型,称之为减径、减壁机架,主要作用是为适应轧管的外径波动,使孔型磨损均匀,同时对于复合管尽量实现横向均匀减壁。后两个机架采用带圆弧侧壁的圆孔型,为均壁、均径机架,主要作用是保证复合管的内外径的圆度。
根据变形制度和孔型设计方法确定每一机架孔型参数。各机架的孔型长半轴ai的计算公式为
(9)
各机架的孔型短半轴bi的计算公式为
(10)
(11)
式中:si顶为第i机架辊顶处复合管总壁厚,mm;λ为经验系数,此处取值1~1.2。
各机架孔型椭圆度系数
(12)
孔型偏心距
(13)
孔型圆弧半径
(14)
根据连轧过程的变形特点,连轧孔型几何参数如图2(a)所示,包括减壁段槽底半径R1,减径段侧壁弧半径R2,辊缝连接弧半径R5,脱离角α1,连接弧角α2,辊缝S,轧辊宽度L,偏心距E,C1、C2、C3分别为R1、R2、R5的圆心。孔型直径的大小与脱离角度的位置以及辊缝的尺寸对横向壁厚的均匀性和复合管的外径有重要的影响。表1为本文所用的部分轧辊参数。
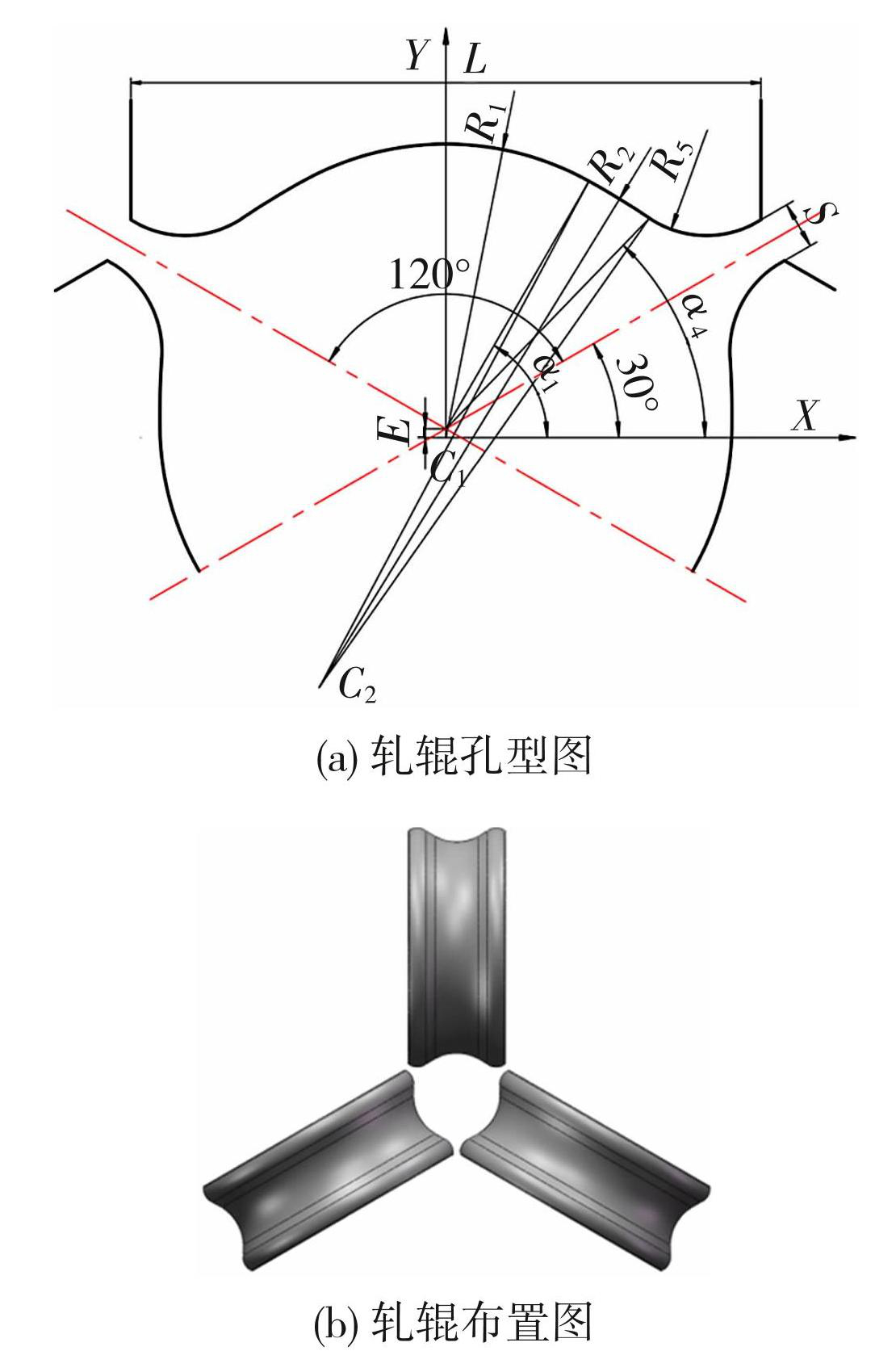
图2三辊连轧管孔型图
Fig.2Three-roll tube pass diagram: (a) rolling pipe pass diagram; (b) pipe rolling layout
表1孔型基本参数
Table1Basic parameters of the pass
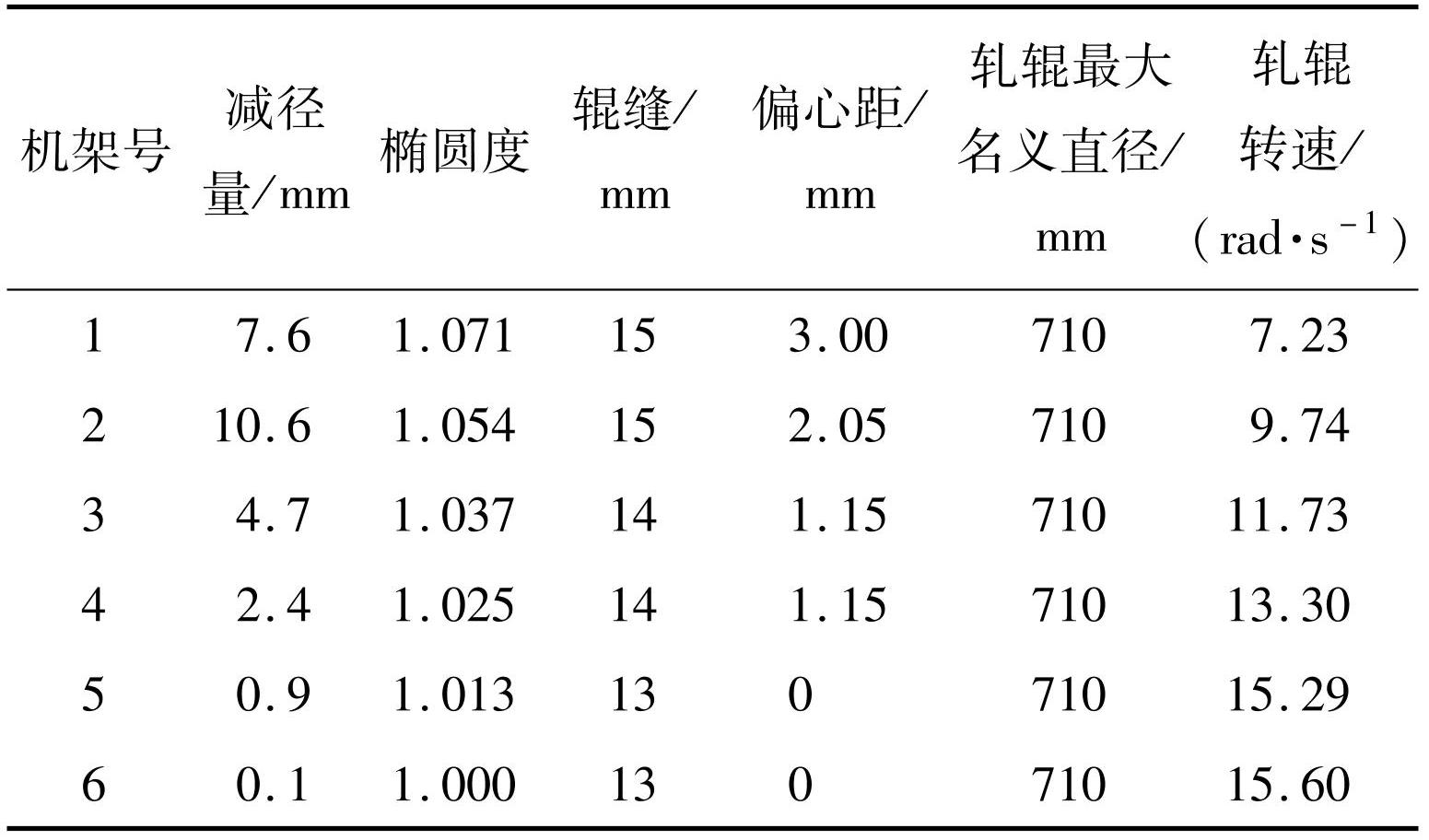
2 有限元分析
2.1 有限元模型
设计模型的外层材料为20#钢,内层为316L不锈钢,外层碳钢尺寸为Φ220 mm×17 mm,内层316L尺寸为Φ186 mm×6.5 mm。经取样实测发现两层金属之间已经完全复合,因此建立模型设定相互作用时,采用绑定约束将两层金属绑定在一起,由于结合层是以微米计算,因此忽略不计。轧制温度为1 100℃,芯棒直径为162.2 mm。为了减少运算量,复合管长度选择为835 mm。轧辊和芯棒的弹性变形可以忽略不计,在模型中设置为刚体,采用的单元格类型为R3D4,划分后网格如图3所示,轧管和外层管坯之间的动摩擦系数为0.3,内层管坯与芯棒之间的摩擦系数为0.1。内外层管划分单元,由于复合管是轴对称模型,为保证网格划分均匀,单元格类型为C3D8R六面体网格单元,这种单元格可以保证周向上不发生畸变。为了保证计算精度,对内外金属管定义切割平面后为边布种,使得横截面上的网格大小划分均匀。
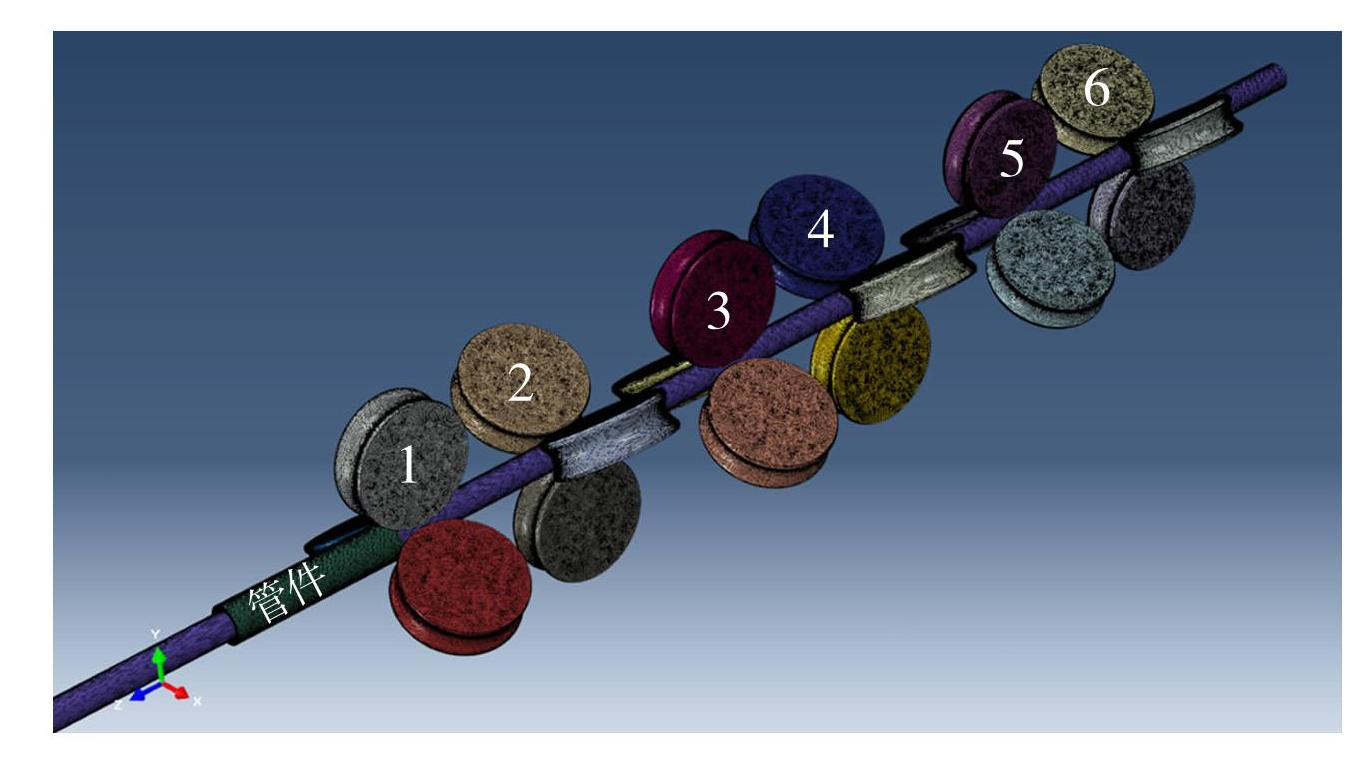
图3复合管连轧模型
Fig.3Composite pipe continuous rolling model
2.2 应变速率研究
在理想状态下,通过计算轧管在每一机架轧制过程中与轧辊中心的接触弧长和减径量来求解其应变速率,计算结果如表2所示。
表2应变速率
Table2The Strain rate
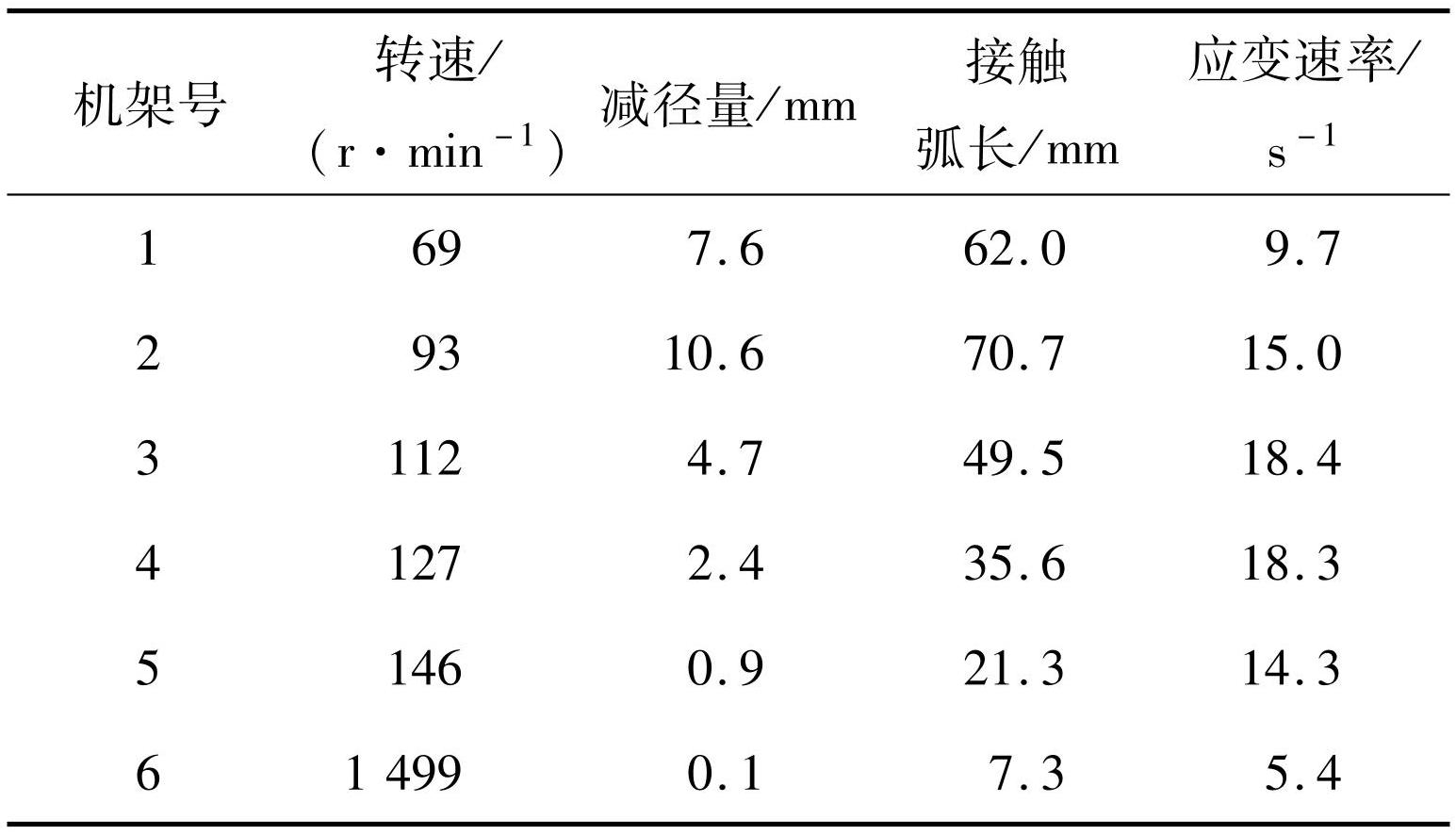
内外层金属采用Gleeble-3800热模拟试验机进行压缩实验,提取其应力-应变曲线,如图4所示。
2.3 轧后外形及壁厚
图5所示是ABAQUS软件模拟钢管连轧过程开始与结束时壁厚节点位置变化情况。图5(a)为模拟前节点位置,此时节点间的距离即钢管的壁厚,图5(b)为模拟结束后节点位置。
由于复合管的连轧过程中金属流动大,属于三维大变形过程,而且在轧辊和芯棒的作用下,内外壁的金属流动情况并不相同,复合管的网格和节点发生偏移,对应节点的距离出现偏差,节点间距离已经不能代表壁厚的大小。因此,本文采用3次样条插值曲线对连轧过程中复合管的内外表面及结合面节点坐标提取后进行插值,进而求得复合管的壁厚。
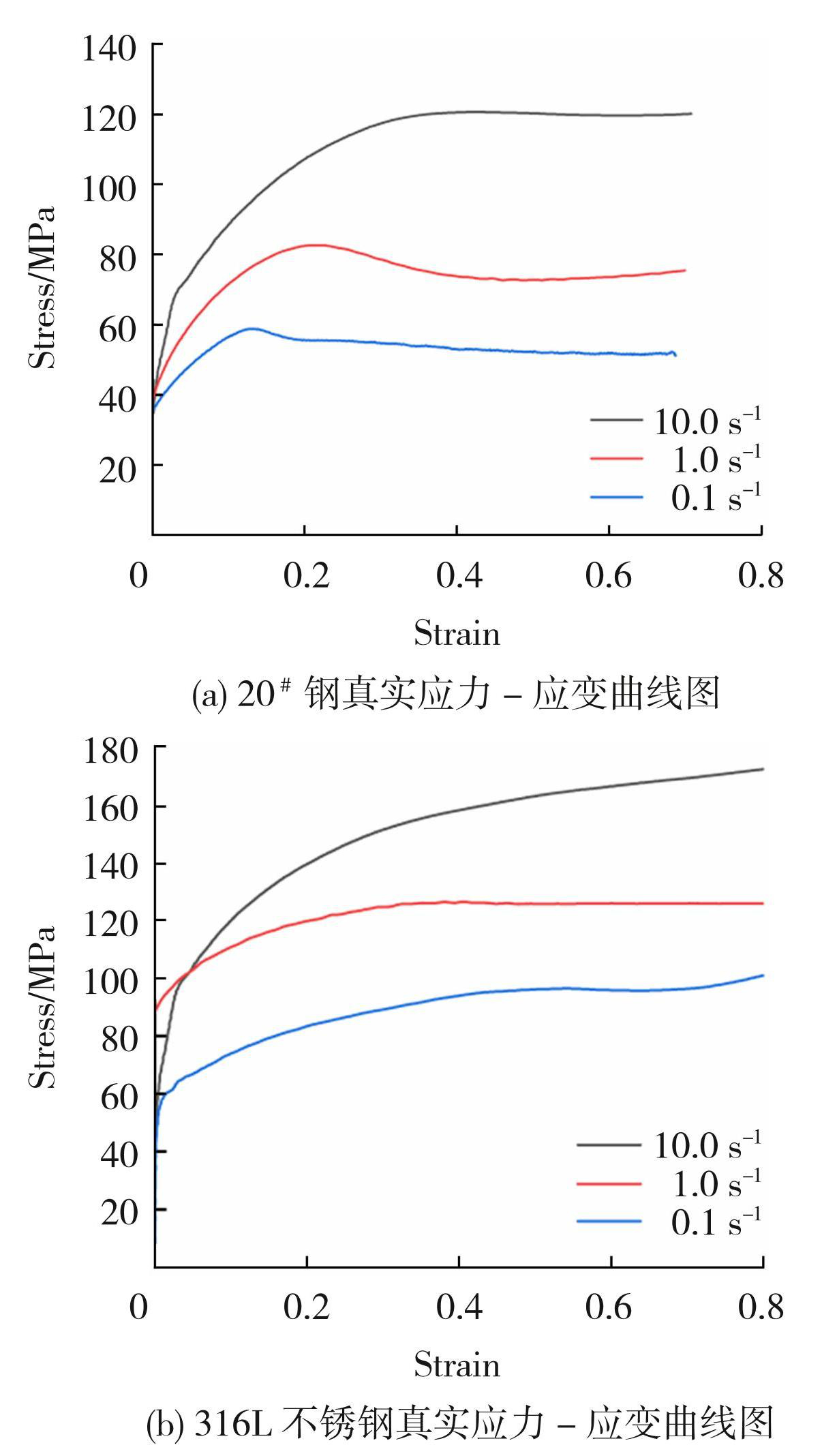
图420#和316L不锈钢材料真实应力-应变曲线
Fig.4Real stress-strain curve of 20# and 316L stainless steel : (a) 20# steel; (b) 316L stainless steel
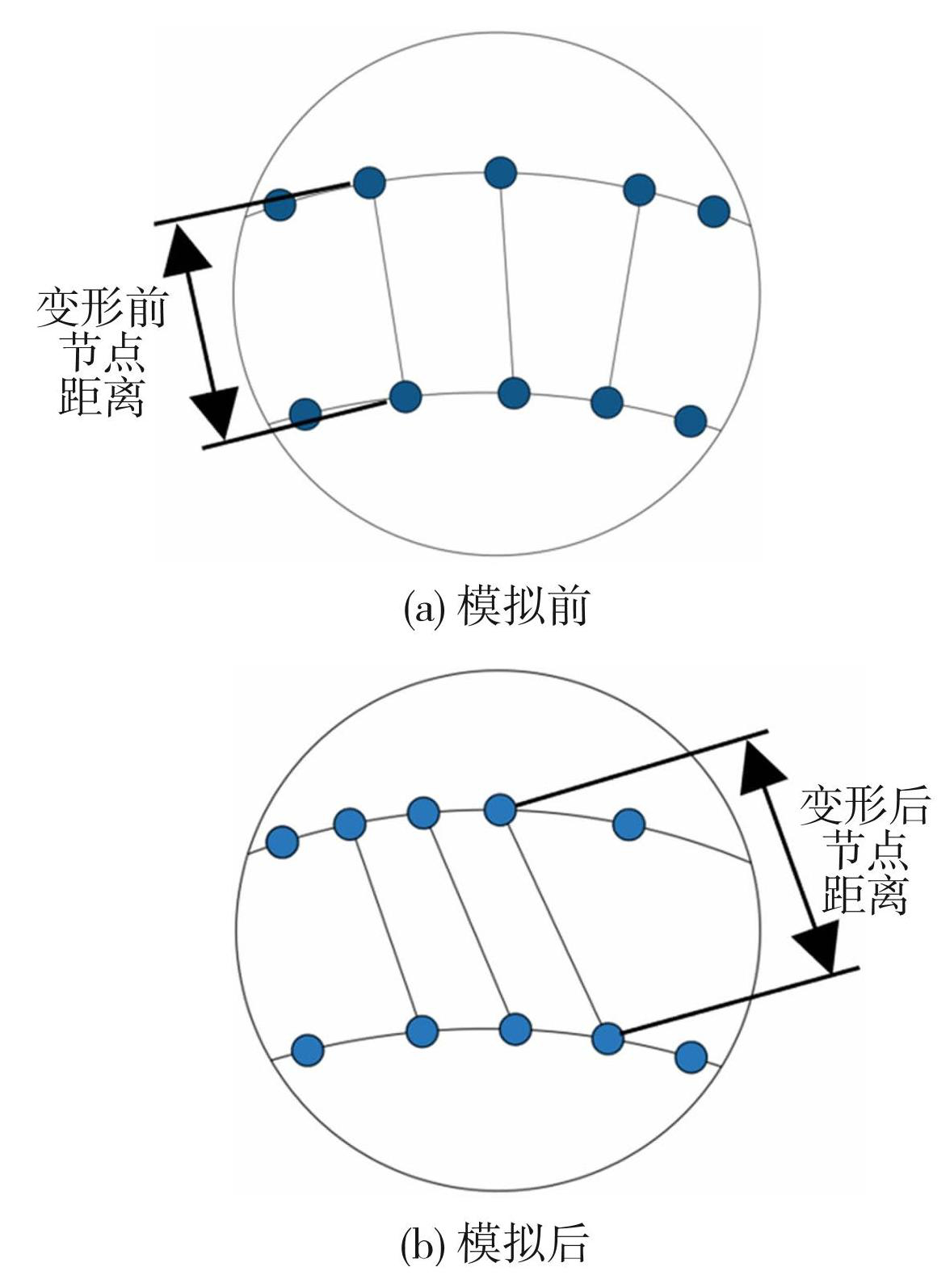
图5模拟前后壁厚节点位置变化
Fig.5Changes in the position of wall thickness nodes before and after simulation: (a) before simulation; (b) after simulation
由于复合管为轴对称图形,故提取其0°~90°范围内各机架出口截面节点,如图6所示,可以看到,内外层壁厚分布均匀,求得的双金属复合管内层不锈钢的平均壁厚为3.11 mm。
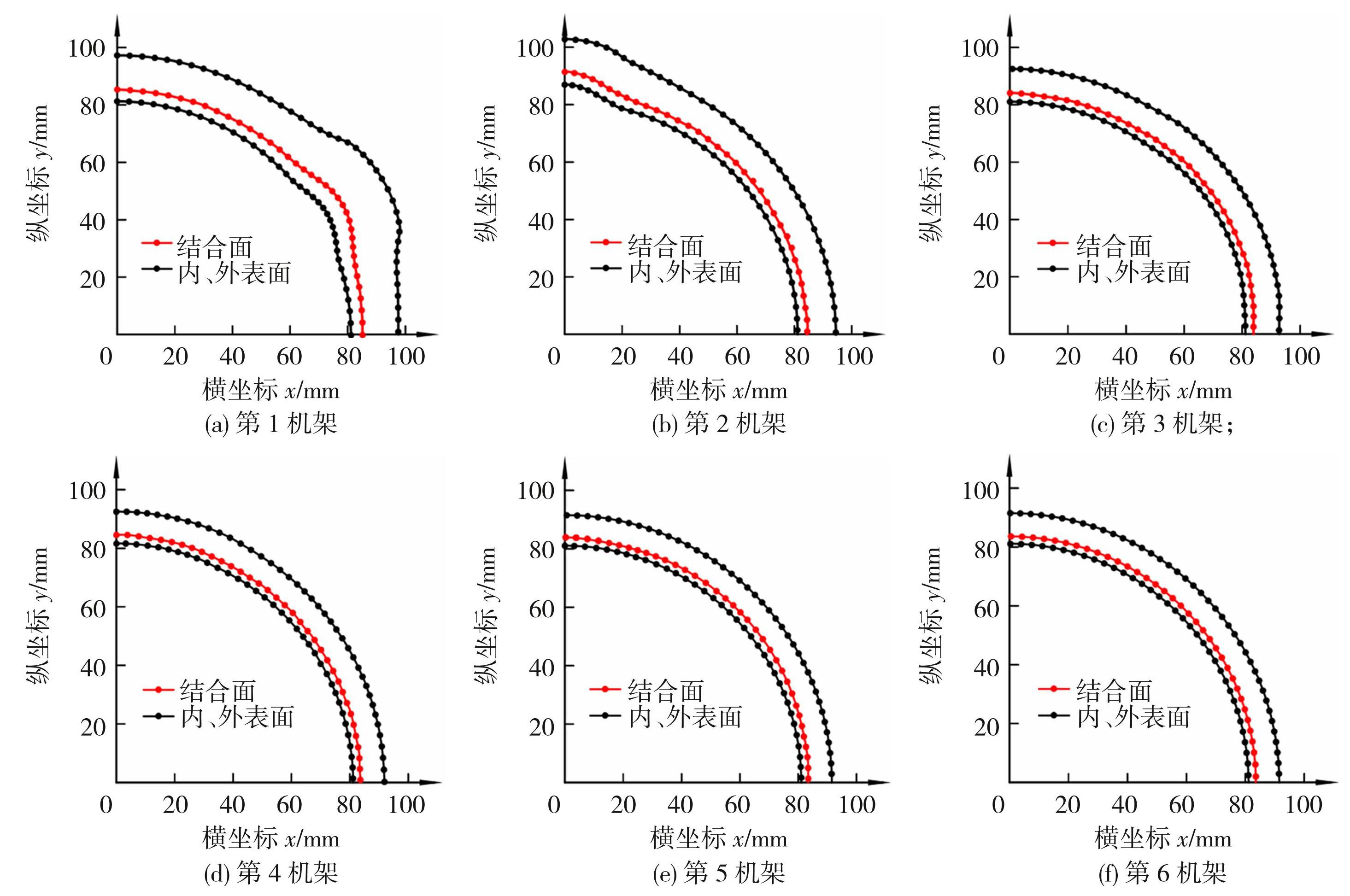
图60°~90°范围内各机架出口截面壁厚示意图
Fig.6Wall thickness of outlet section of each stand in the range of 0°~90°: (a) first rack; (b) second rack; (c) third rack; (d) fourth rack; (e) fifth rack; (f) sixth rack
2.4 复合管终轧应力分布
由于复合管轧制内外层金属的材料不同,因此与单种金属轧制的受力情况也不同。
图7所示为复合管在轧制结束后的内外管应力分布图,可以看出,复合管在轧制结束后内管、外管的应力分布比较均匀,内管所受平均应力要比外管大,内外管的最大应力出现在管头、管尾区域,可能是由于复合管在轧制过程中,这两部分的不均匀变形现象较为严重,其余部分应力基本保持均匀。
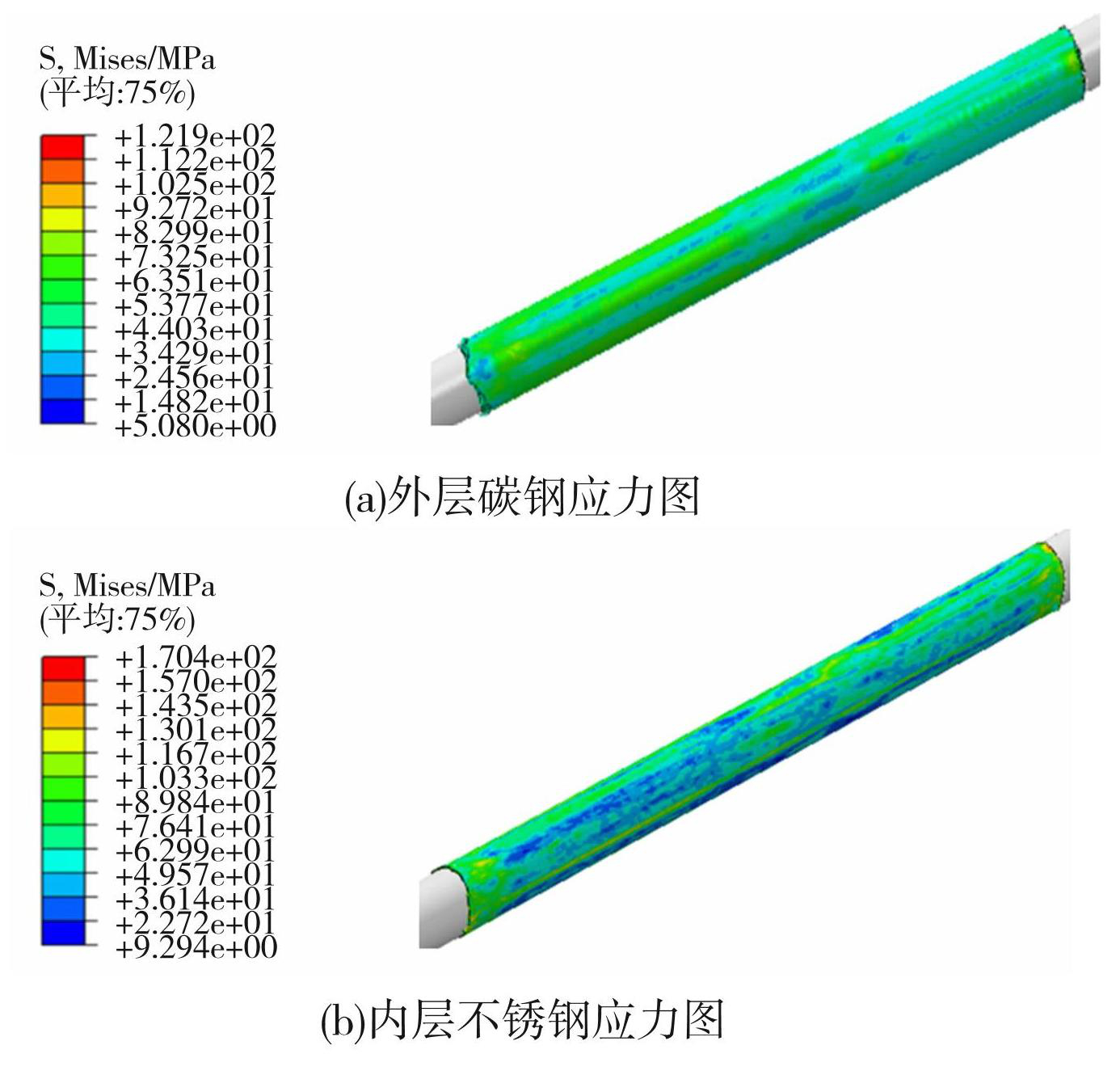
图7内外层荒管应力分布
Fig.7Stress distribution of rolled tube billet after rolling: (a) stress diagram of outer carbon steel; (b) stress diagram of inner stainless steel
3 实验验证
3.1 轧制实验过程
为了验证有限元分析的结果,在某厂的生产设备上进行了轧制实验,图8所示是Y型三辊六机架机组轧管实验现场。轧得的荒管冷却切断后形貌如图9所示,可以看到内外表面平整,且内表面比外表面光洁,从端口可见内层奥氏体不锈钢光滑发亮,外层碳钢氧化明显。
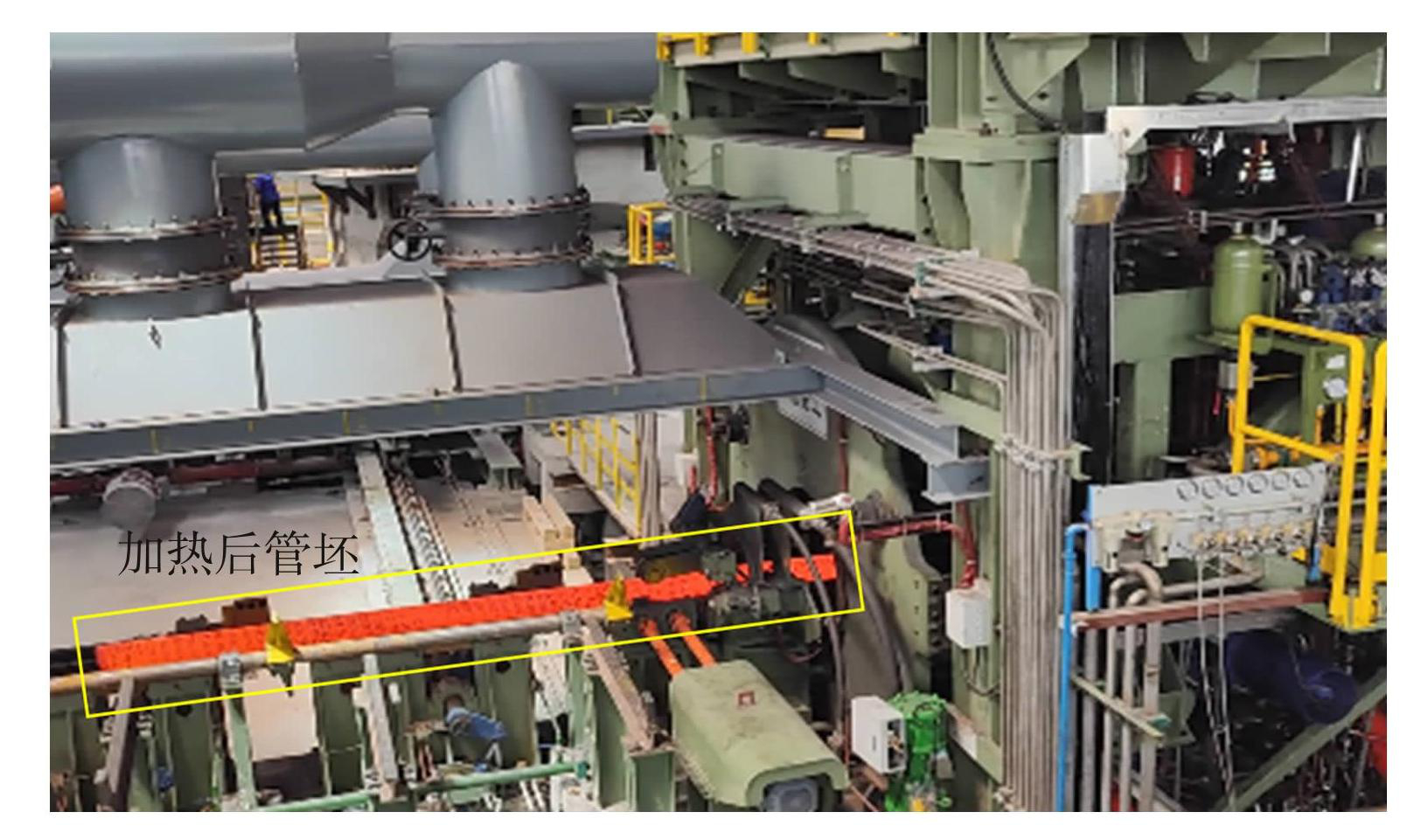
图8Y型三辊六机架轧管实验现场
Fig.8Y-type three-roll six-stand unit
由图9可清晰地看到断面壁厚情况,在其圆周上选取8个点进行壁厚尺寸测量,测得不锈钢平均壁厚约为3 mm,与模拟结果比较接近,误差范围小于10%,满足产品标准。
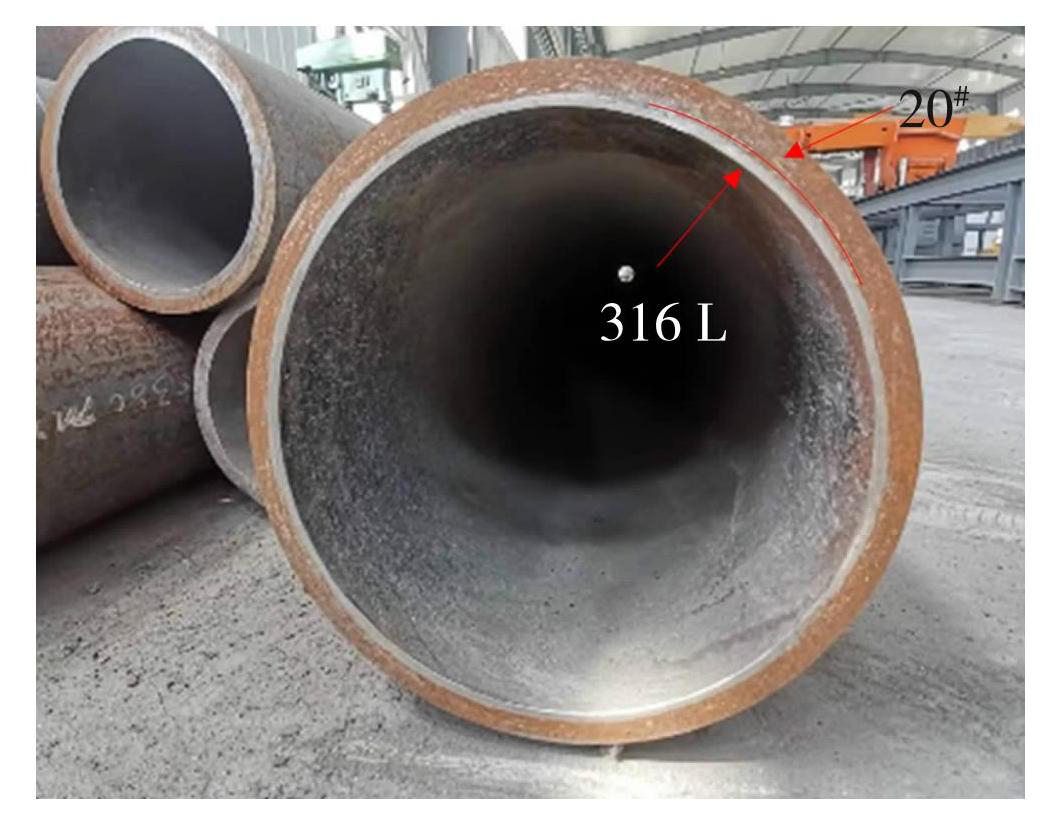
图9轧后荒管
Fig.9Bimetallic pipe of after rolling
3.2 拉剪实验
对于双金属复合管,结合强度是评价其轧制质量的一个重要指标[17-19],此处结合强度是指复合管内层金属和外层金属的结合面所能承受的最大剪切应力。本文通过实验方法测量拉剪强度,根据国标GB/T6396—2008,在复合管轧制方向用线切割的方式切样,其拉剪试样如图10所示。
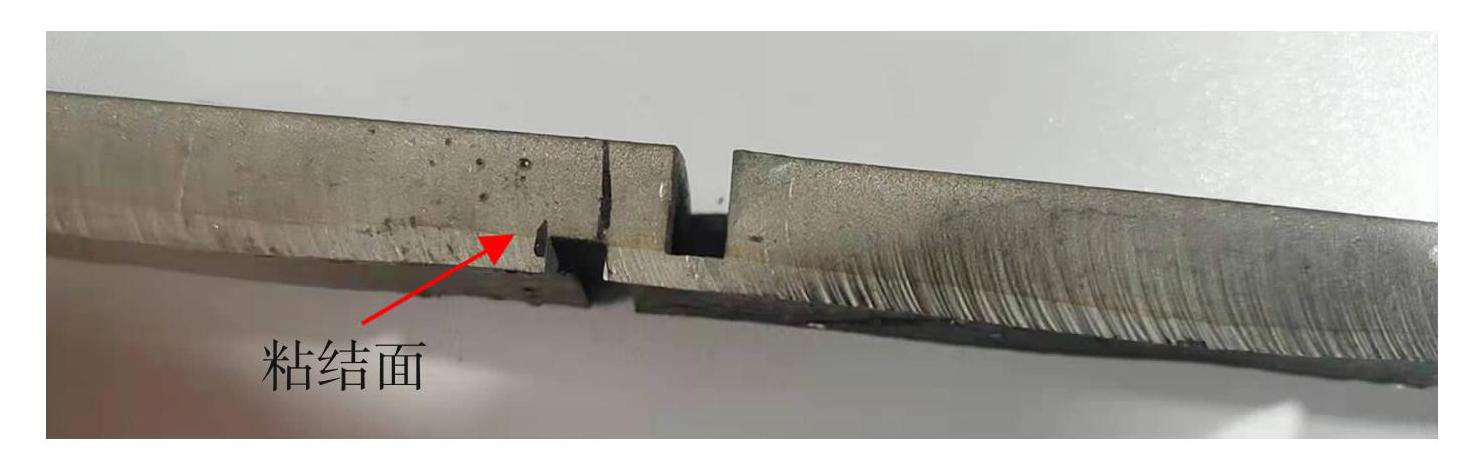
图10拉剪试样
Fig.10Tensile shear specimen
图11为双金属复合管抗剪切强度-位移曲线,可以看出复合管的抗剪切强度随着试样拉剪位移的增加在逐渐增大,拉断时最大剪应力强度约为445 MPa,结合面的强度可以充分满足其机械性能的要求。图11中可以看出轧制后双金属复合管的抗剪切强度远远超出国标GB/T6396—2008中所要求的210 MPa。
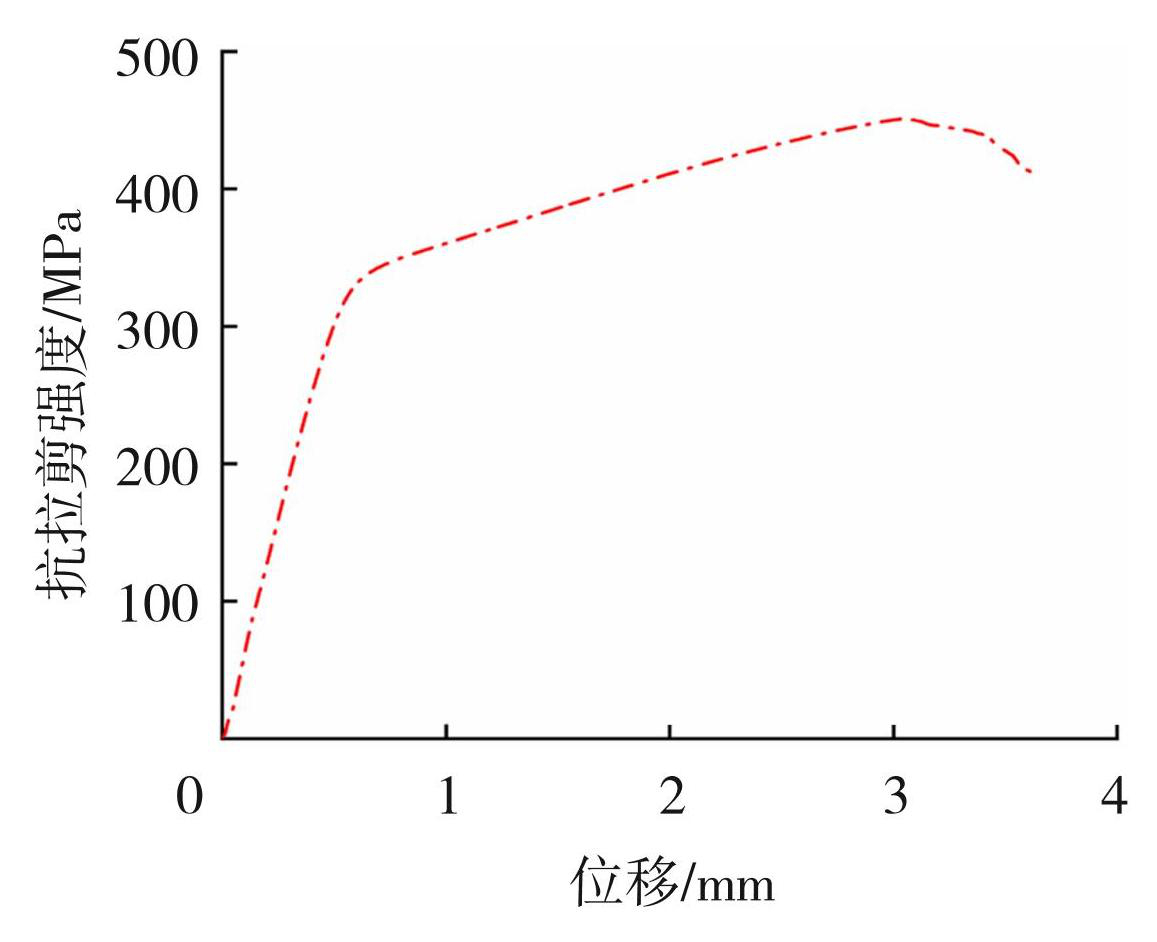
图11双金属复合管抗剪切强度-位移曲线
Fig.11Shear strength-displacement curve of bimetallic composite pipe
3.3 夹持力实验
按照国标GB/T31940—2015流体输送用双金属复合耐腐蚀钢管要求,对双金属复合管切样检测,试样如图12(a)所示,检测设备为AUM/60W(LX05)微机控制液压万能试验机进行检测。试样尺寸: 测试长度×复层厚度=72.4 mm×3.25 mm,最大压力>600.25 kN,变形高度不超过10%。夹持力测试结果表明,在最大压力下基层复层无变形、无破损现象,满足工业用管要求。
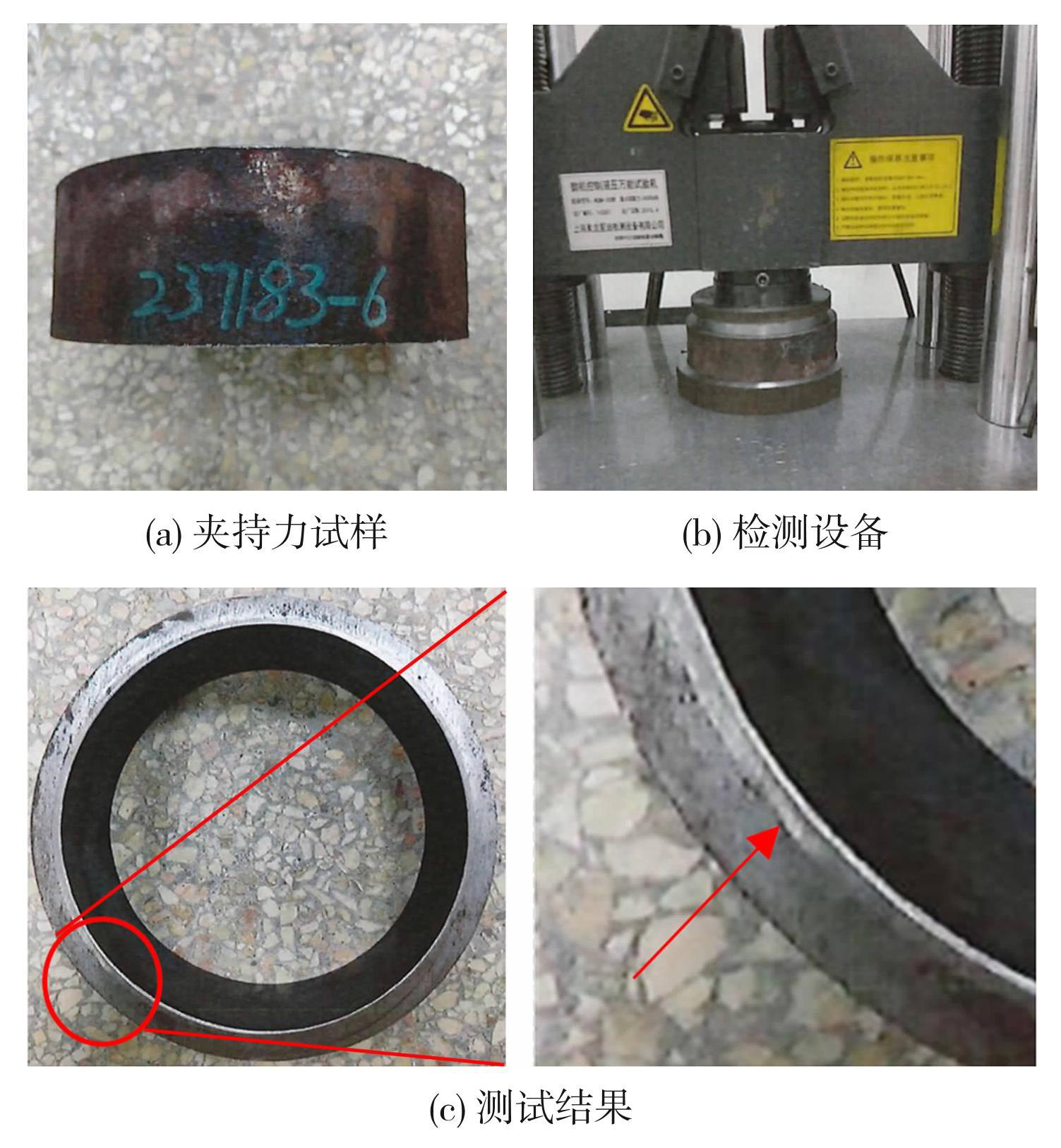
图12夹持力测试过程
Fig.12Clamping force testing process: (a) clamping force specimen; (b) testing equipment; (c) test results
3.4 微观组织测试
图13为双金属复合管轧制后复合区域的显微组织形貌,上半部分为20#钢,下半部分为316L不锈钢。
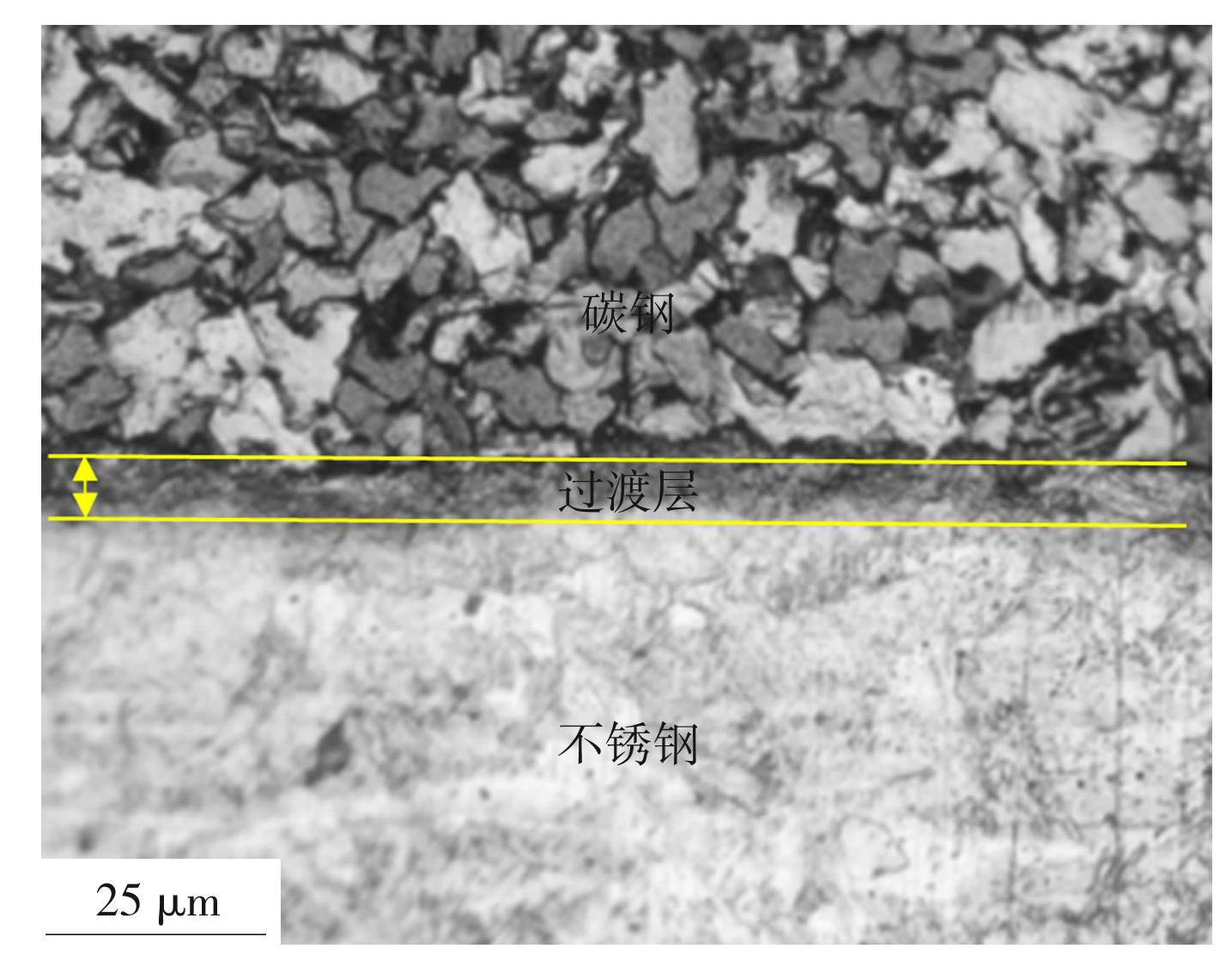
图13轧后双层金属的微观组织
Fig.13Microstructure of bimetals after rolling
从图13可以看出,两层金属之间的复合界面清晰可见,界面结合良好,根据显微组织的不同,可以将双金属复合管结合区分成3部分,上部区域为碳钢侧的显微组织,由铁素体和珠光体组成,此区域为碳钢原有的显微组织;中间区域为结合部分,此处的碳元素含量降低;下部区域为不锈钢侧的显微组织,由奥氏体晶粒组成,其中碳钢和中间层之间以及不锈钢与中间层之间有明显的过渡层形成。
3.5 晶间腐蚀
为了检验加工工艺的合理性,采用GB/T4334—2020晶间腐蚀实验方法对工件取样检测。在两层金属结合面处切取两个试样进行间腐蚀实验,测试溶液为铜-硫酸铜-16%硫酸溶液(微沸)650℃保温2 h,而后空冷。对腐蚀后的试样进行显微观察,组织形貌放大10倍后如图14所示,未发现晶间腐蚀裂纹,符合国标要求。
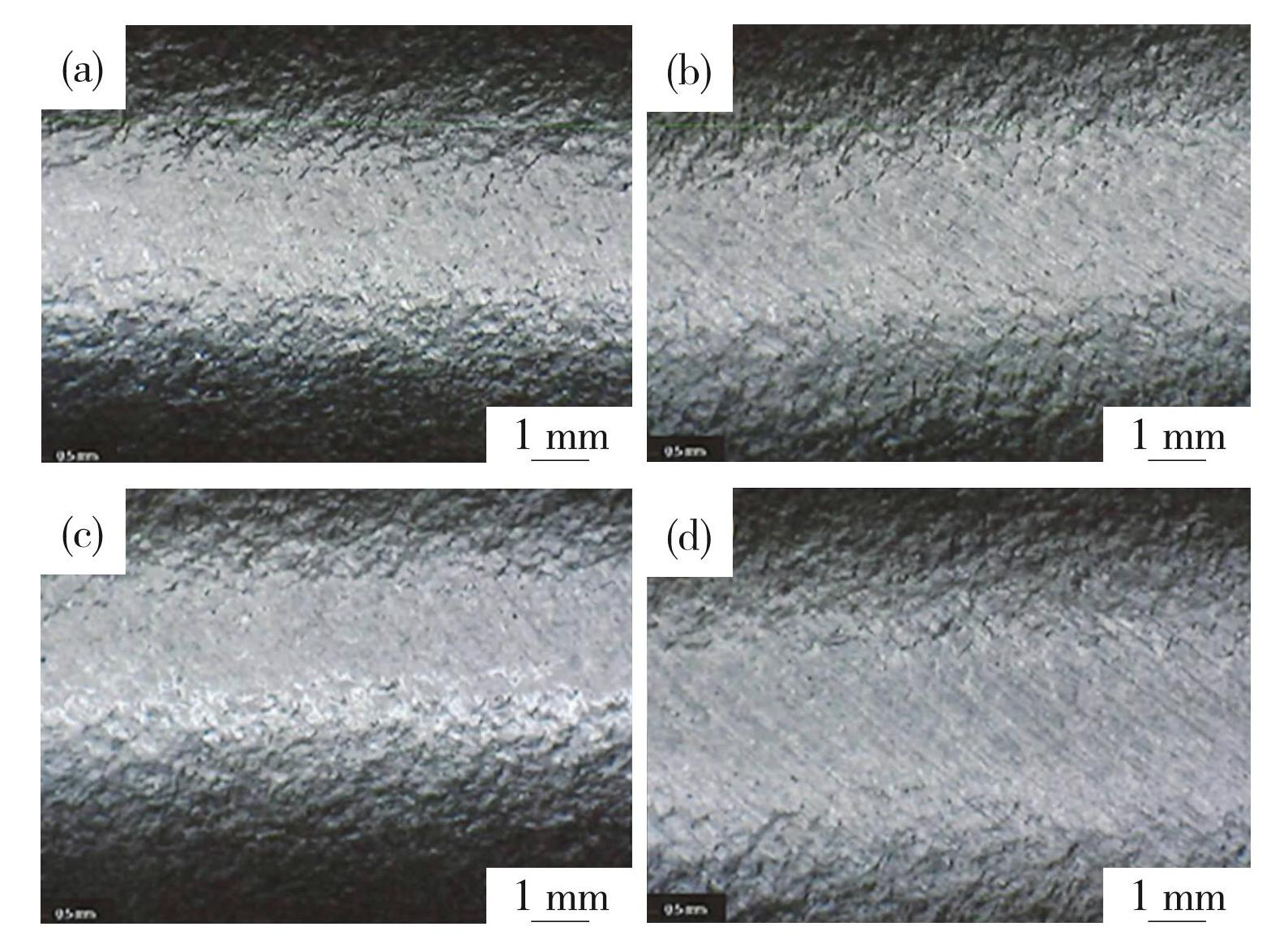
图14样品组织形貌图:(a)样品1外侧;(b)样品1内侧;(c)样品2外侧;(d)样品2内侧
Fig.14Morphology of the sample: (a) outer side of sample1; (b) inner side of sample1; (c) outer side of sample 2; (d) inside sample 2
4 结论
1) 首先给出减径率分配的计算方法以及芯棒直径等参数的确定方法,在此基础上给出了孔型参数的设计方法、轧辊速度的分配以及芯棒速度的确定思路。
2) 对六机架复合管热连轧进行有限元模拟,获得终轧机架中复合管的横截面形状圆整、壁厚精度高。复合管内管、外管的应力分布均匀,内管所受等效应力比外管大。
3) 对实验获得的复合管进行拉剪实验,剪切强度达到445 MPa,满足使用要求。并采用万能试验机对复合管进行夹持实验,在最大压力下双层金属结合面无变形、破损现象。
4) 对轧制试样界面结合处进行了晶间腐蚀实验和微观组织观察,可见界面结合良好,且在界面处有明显的过渡层,未发现晶间腐蚀裂纹。