引用本文: | 李永亮,王敬,梁强.响应面分析法优化不锈钢激光切割工艺参数[J].材料科学与工艺,2020,28(4):65-72.DOI:10.11951/j.issn.1005-0299.20180403. |
| LI Yongliang,WANG Jing,LIANG Qiang.Optimization of laser cutting process parameters for stainless steel using response surface method[J].Materials Science and Technology,2020,28(4):65-72.DOI:10.11951/j.issn.1005-0299.20180403. |
|
|
|
本文已被:浏览 658次 下载 524次 |
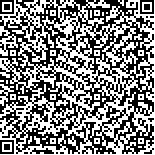 码上扫一扫! |
|
响应面分析法优化不锈钢激光切割工艺参数 |
李永亮1,2,3,王敬1,3,梁强1,3
|
(1.重庆工商大学 机械工程学院,重庆 400069;2.重庆工商大学 工程训练中心,重庆 400069;3.制造装备机构设计与控制重庆市重点实验室(重庆工商大学),重庆 400069)
|
|
摘要: |
为了获得良好的不锈钢激光切割质量,确定合理的切割工艺参数,本文以3 mm厚304不锈钢为研究对象,采用响应面法进行试验方案的设计和分析,利用超景深显微镜进行了试样表面切缝宽度、表面纹理最大峰值、挂渣量的测量,利用最小二乘法进行数据处理,研究了激光功率(X1)、切割速度(X2)、离焦量(X3)以及辅助气体压力(X4)对不锈钢切割表面切缝宽度、表面纹理最大峰值、挂渣量的影响规律,并基于响应面法得到了3个响应目标的预测函数.实验结果表明:X2=2.48 m/min,X3=-1.05 mm,X4=1 MPa时,随着激光功率的增加,切缝宽度不断增大;X1=300 W, X4=1.2 MPa时,随着切割速度的加快切缝宽度逐渐减小,随着离焦量的增大切缝宽度先减小后增大;X1=300 W,X3=0 mm,X4=1.40 MPa时表面纹理的最大波峰值RZ随着激光功率、离焦量以及切割速度的增大先减小后增大。以切缝宽度最窄、表面纹理最大峰值最小、挂渣量最少为响应目标确定了3 mm厚304不锈钢激光切割的最佳工艺参数为X1=365.86 W,X2=2.75 m/min,X3=0 mm,X4=1.4 MPa。试验验证发现:切缝宽度、表面纹理最大峰值、挂渣量的预测误差应分别控制在8.4%~12.7%、21%~24.9%、16.7%~19.5%。 |
关键词: 激光切割 响应面法 不锈钢 切缝宽度 表面纹理 刮渣量 预测模型 |
DOI:10.11951/j.issn.1005-0299.20180403 |
分类号:TG156 |
文献标识码:A |
基金项目:重庆市基础科学与前沿技术研究专项基金资助项目(cstc2017jcyjAX0175);制造装备机构设计与控制重庆市重点实验室平台开放项目(KFJJ2017053);重庆市创新技术创新与应用发展重点项目(CTBU-KFJJ2019078). |
|
Optimization of laser cutting process parameters for stainless steel using response surface method |
LI Yongliang1,2,3, WANG Jing1,3, LIANG Qiang1,3
|
(1.College of Mechanical Engineering, Chongqing Technology and Business University, Chongqing 400069,China; 2.Engineering Training Center, Chongqing Technology and Business University, Chongqing 400069,China; 3.Design and Control Key Laboratory of Manufacturing Equipment Mechanism of Chongqing(Chongqing Technology and Business University), Chongqing 400069,China)
|
Abstract: |
To obtain high quality laser cutting stainless steel and ascertain reasonable cutting process parameters, the response surface method was applied to design and analyze an experimental project, which took 3 mm thickness stainless steel 304 as the research object. On the basis of determining the measurement method, the kerf width, the maximum peak of surface texture, and the slag thickness on the sample surface were measured by using the super depth-of-field microscope. Unreasonable data were eliminated by Grabbs outlier test method, and the data were processed by the least square method. Effects of laser power, cutting speed, focus positions, and pressure of assisting gas on the kerf width, the maximum peak of surface texture, and the slag thickness were investigated. Based on the method of response surface, the response function of the kerf width, the maximum peak of surface texture, and the slag thickness was obtained. Results indicated that when X2=2.48 m/min, X3=-1.05 mm,X4=1 MPa, the width of the slit increased with the increase of the laser power. When X1=300 W,X4=1.2 MPa, the width of the slit gradually decreased, and then increased with the increase of defocusing. When X1=300 W,X3=0 mm,X4=1.40 MPa, the maximum wave peak of the surface texture decreased first and then increased with the increase of the laser power, the defocusing amount, and the cutting speed. By using the minimum kerf width, the minimum peak value of the surface texture, and the minimum slag thickness, the optimum technic parameter of 3 mm thickness laser cutting stainless steel 304 was determined to be,X1=365.86 W,X2=2.75 m/min,X3=0 mm,X4=1.4 MPa.The test results showed that the prediction errors of slit width, maximum peak value of surface texture and slag amount were controlled between 8.4%~12.7%, 21%~24.9% and 16.7%~19.5%. |
Key words: laser cutting response surface method stainless steel kerf width surface texture slag thickness prediction model |
|
|
|
|