引用本文: | 李立涛,高谦,杨志强,陈得信.矿用充填胶凝材料激发剂配比智能优化决策[J].哈尔滨工业大学学报,2019,51(10):137.DOI:10.11918/j.issn.0367-6234.201806028 |
| LI Litao,GAO Qian,YANG Zhiqiang,CHEN Dexin.Intelligent optimization for the activator proportion of filling cementitions material[J].Journal of Harbin Institute of Technology,2019,51(10):137.DOI:10.11918/j.issn.0367-6234.201806028 |
|
|
|
本文已被:浏览 1415次 下载 825次 |
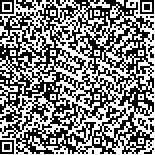 码上扫一扫! |
|
矿用充填胶凝材料激发剂配比智能优化决策 |
李立涛1,2,高谦1,2,杨志强1,2,3,陈得信3
|
(1.北京科技大学 土木与资源工程学院,北京 100083; 2.金属矿山高效开采与安全教育部重点实验室(北京科技大学),北京 100083; 3.镍钴资源综合利用国家重点实验室(金川集团有限公司), 甘肃 金昌 737100)
|
|
摘要: |
针对矿用充填胶凝材料不同配比的激发剂化学复合作用所引起充填胶结体单轴抗压强度复杂非线性变化问题,提出一种充填胶凝材料激发剂配比智能优化决策方法. 首先, 开展均匀设计试验获取不同激发剂配比充填胶结体抗压强度数值;其次,采用动态自适应交换变异概率及适应度竞争交换方式的改进遗传树表征激发剂与充填胶结体抗压强度之间的非线性复杂关系,运算至49代时即满足终止法则,收敛速度较快,函数精度高;最后,确定约束条件,建立激发剂配比优化模型,采用遗传算法的全局快速寻优技术,获得满足充填体强度要求的激发剂优化配比. 结果表明: 采用该智能优化方法研究铁矿新型充填胶凝材料激发剂配比,优化结果显示, 满足该矿山充填体强度的胶凝材料优化配比为生石灰2.91%、石膏17.39%、矿渣粉79.7%; 在该优化配比周围开展验证试验,试验结果显示为生石灰3%、石膏17%、矿渣粉80%时、充填体7、28d抗压强度均达到最大,与激发剂配比智能优化方法获得的胶凝材料配比相吻合.相比42.5水泥,用该智能优化方法获得的激发剂配比制备全尾砂充填胶凝材料,可降低材料成本22%. |
关键词: 均匀设计 激发剂配比 改进遗传树 遗传算法 智能优化 |
DOI:10.11918/j.issn.0367-6234.201806028 |
分类号:TD853 |
文献标识码:A |
基金项目:国家重点研发计划(2017YFC0602903) |
|
Intelligent optimization for the activator proportion of filling cementitions material |
LI Litao1,2,GAO Qian1,2,YANG Zhiqiang1,2,3,CHEN Dexin3
|
(1.School of Civil and Resource Engineering, University of Science and Technology Beijing, Beijing 100083, China; 2.Key Laboratory High-Efficient Mining and Safety of Metal Mines (University of Science and Technology Beijing), Ministry of Education, Beijing 100083, China; 3.State Key Laboratory of Nickel and Cobalt Resources Comprehensive Utilization (Jinchuan Group Co. LTD), Jinchang 737100, Gansu China)
|
Abstract: |
In view of the complex nonlinear change of the compressive strength of filling cementation body caused by the chemical compound effect of different proportioning of activator in filling cementitious materials, an intelligent optimization for the mixture ratio of filling cementitious material was proposed. First, uniform design tests were carried out to obtain the compressive strength values of different activator proportions of backfill bodies. Then, improved genetic tree about dynamic adaptive exchange mutation probability and fitness competition exchange mode was used to characterize the high-precision nonlinear complex relationship between the activator material and the compressive strength of the backfill. When computing to the 49th generation, it satisfy the termination rule of the algorithm. The convergence speed was fast and the function precision was high. Finally, the constraint condition was determined and the optimization model of the proportion of activator was established. The global optimization technology of genetic algorithm was used to get the optimal ratio of the activator material to meet the strength requirements of backfill. The intelligent optimization method was utilized to study the ratio of activator for the new filling cementitious material in iron mine. The optimization show that the optimum proportion for the strength of the mine backfill was 2.91% lime, 17.39% gypsum, and 79.7% slag powder. Verification test was carried out around the optimum proportion, and results show that the compressive strength of the filling body at 7 d and 28 d reach the maximum when lime was 3%, gypsum was 17%, and slag powder was 80%, which was in accordance with the test results. Compared with 42.5 cement, the whole tailings filling cementing material could be prepared by the activator proportion prepared by the intelligent optimization method, and the cost of cementing material could be reduced by 22%. |
Key words: uniform design activator proportion improved genetic tree genetic algorithm intelligent optimization |
|
|
|
|