引用本文: | 杨新文,张英杰,刘姝彤,王小华.高速铁路SKL15扣件弹条断裂原因分析[J].哈尔滨工业大学学报,2023,55(3):10.DOI:10.11918/202111092 |
| YANG Xinwen,ZHANG Yingjie,LIU Shutong,WANG Xiaohua.Analysis on fracture causes of SKL15 fastener clips in high-speed railway[J].Journal of Harbin Institute of Technology,2023,55(3):10.DOI:10.11918/202111092 |
|
|
|
本文已被:浏览 3434次 下载 3558次 |
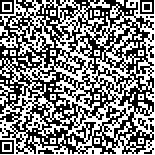 码上扫一扫! |
|
高速铁路SKL15扣件弹条断裂原因分析 |
杨新文1,2,张英杰1,2,刘姝彤1,2,王小华3
|
(1. 上海市轨道交通结构耐久与系统安全重点实验室(同济大学),上海 201804; 2.道路与交通工程教育部重点实验室(同济大学),上海 201804;3.中国铁路上海局集团有限公司合肥工务段,合肥 230031)
|
|
摘要: |
为了分析高速铁路运营线路扣件弹条断裂原因,以SKL15型弹条为研究对象,采用现场测试与仿真分析相结合的方法进行研究。首先,现场调查线路的波磨情况与弹条的振动响应特性;其次,建立扣件系统有限元模型,分析弹条在自由状态和安装状态下的模态特征,并进行基于模态叠加法的谐响应分析,通过对比现场测试结果和仿真结果,证明模型的可靠性;最后,结合测试结果和线路运营情况,分析造成弹条断裂的原因并提出整治措施。结果表明:造成弹条断裂的主要原因是列车以120 km/h的时速通过显著波长为50~60 mm的波磨区段时所激发的载荷频率与安装状态下的弹条模态频率(550~650 Hz)十分接近,从而引起弹条强烈的共振作用,导致弹条跟端应力显著增大,最终引发疲劳损伤。针对这一原因,提出了如钢轨打磨、列车调速、弹条结构优化等一系列解决方法。 |
关键词: 高速铁路 弹条断裂 波磨 频响分析 模态分析 共振 |
DOI:10.11918/202111092 |
分类号:U213.5;U238 |
文献标识码:A |
基金项目:国家自然科学基金(6,4) |
|
Analysis on fracture causes of SKL15 fastener clips in high-speed railway |
YANG Xinwen1,2,ZHANG Yingjie1,2,LIU Shutong1,2,WANG Xiaohua3
|
(1.Shanghai Key Laboratory of Rail Infrastructure Durability and System Safety (Tongji University), Shanghai 201804, China; 2.Key Laboratory of Road and Traffic Engineering of Ministry of Education (Tongji University), Shanghai 201804, China; 3. Hefei Track Maintenance Division, China Railway Shanghai Bureau Group Co., Ltd., Hefei 230031, China)
|
Abstract: |
To analyze the reasons for the fracture of fastener clips in high-speed railway operating lines, SKL15 clips were studied as the object using a method of combining field test and simulation analysis. First, an on-site investigation of rail corrugation and vibration response characteristics of clips was performed. Then, a finite element model of the fastening system was established. The modal characteristics of the clips in their free and assembly states were analyzed, and a harmonic response analysis was carried out based on the modal superposition method. The reliability of the model was proved by comparing the field test results with the simulation results. Finally, in combination with the test results and the railway operation situation, the fracture causes of the fastener clips were analyzed, and remedial measures were put forward. Results showed that the main reason for the fracture of clips was that the load frequency excited when the train passed through the corrugation section with a significant wavelength of 50-60 mm at a speed of 120 km/h was very close to the modal frequency (550–650 Hz) of the clips in the assembly state, which caused the clips to have a strong resonance effect and resulted in the significant increase in the stress at the heel end of the clips, and eventually, fatigue damage. As a result, some solutions were put forward, such as rail grinding, train speed adjustment, and clip structural optimization. |
Key words: high-speed railway fastener clip fracture corrugation frequency response analysis modal analysis resonance |
|
|
|
|