引用本文: | 李占金,郝家旺,甘德清,刘志义.冲击载荷下磁铁矿石破碎的能量耗散特性[J].哈尔滨工业大学学报,2020,52(4):150.DOI:10.11918/201808039 |
| LI Zhanjin,HAO Jiawang,GAN Deqing,LIU Zhiyi.Energy dissipation characteristic of magnetite ore crushing under impact load[J].Journal of Harbin Institute of Technology,2020,52(4):150.DOI:10.11918/201808039 |
|
|
|
本文已被:浏览 1493次 下载 865次 |
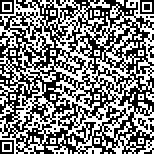 码上扫一扫! |
|
冲击载荷下磁铁矿石破碎的能量耗散特性 |
李占金1,郝家旺1,2,甘德清1,刘志义1
|
(1.华北理工大学 矿业工程学院,河北 唐山 063200; 2.北京科技大学 土木与资源工程学院,北京 100083)
|
|
摘要: |
针对金属矿山企业破碎磁铁矿石时,存在着耗能巨大且能量利用率较低的工程问题. 利用分离式Hopkinson压杆装置和高速摄影技术,首先,研究了磁铁矿石在冲击载荷下的能量运移转化规律及其机理;其次,采用标准方孔砂石筛与GZS-1高频振筛仪,分析了不同耗散能下磁铁矿石破碎块度的分布规律、平均块度的变化情况、以及矿石冲击破碎模式的转变过程;然后,分析了随应变率提高,矿石能量耗散率与破碎程度的相关性问题;最后,结合影响矿石块度分布的基本因素,推导出了磁铁矿石平均块度的预测模型表达式. 结果表明:随入射能提高,矿石波阻抗的降低,改变了矿石与压杆间的透射系数与反射系数,影响着各能量在入射能中的占比分布,即能量耗散率和能量反射率增大,而能量透射率却减小;耗散能越高,磁铁矿石的破碎程度越重,当耗散能由14.79 J提高到121.18 J时,矿石破碎块度的主要分布区域由粗粒端(26.5 mm,37.5 mm)向细粒端(4 mm,16 mm)移动;耗散能与平均块度(ds)呈减对数关系,ds降低了56.04%;ds存在着一个临界值,当ds大于该值时,矿石能量耗散率和破碎程度呈正相关;反之,两者呈负相关;在该值处,磁铁矿石可实现最优破碎. 研究成果对于磁铁矿石破碎工序中的能耗控制具有一定参考价值. |
关键词: 磁铁矿石 冲击载荷 能量耗散 块度分布 最优破碎 |
DOI:10.11918/201808039 |
分类号:TU45 |
文献标识码:A |
基金项目:国家自然科学基金(51374087);河北省自然科学基金(E2015209176) |
|
Energy dissipation characteristic of magnetite ore crushing under impact load |
LI Zhanjin1,HAO Jiawang1,2,GAN Deqing1,LIU Zhiyi1
|
(1.College of Mining Engineering, North China University of Science and Technology, Tangshan 063200, Hebei, China; 2.School of Civil and Resource Engineering, University of Science and Technology Beijing, Beijing 100083, China)
|
Abstract: |
In view of crushing magnetite ore in metal mining enterprises, engineering problems exist such as huge energy consumption and low energy utilization ratio. Split Hopkinson pressure bar device and high-speed photography technology were utilized in this study. First, the pattern and mechanism of energy migration and transformation of magnetite ore under impact load were studied. Second, the standard square hole sand and stone sieve and the GZS-1 high frequency vibrating sieve were adopted to investigate the fragmentation distribution of magnetite ore, the variation of the average particle size, and the transformation process of ore impact crushing mode under different dissipation energy. Then, the correlation problem between ore energy dissipation rate and crushing degree was analyzed with the increase of strain rate. Finally, combining with the basic factors that affect ore fragmentation distribution, the prediction model expression of the average particle size of magnetite ore was derived. The research shows that with the increase of incident energy, the decrease of ore wave impedance changed the transmission coefficient and the reflection coefficient between ore and pressure bar, and affected the distribution of each energy in incident energy. It means that the energy dissipation rate and the energy reflectance increased, but the energy transmittance decreased. The higher the dissipated energy was, the severer the degree of ore broken was. When ore dissipated energy is increased from 14.79 J to 121.18 J, the main distribution region of ore fragment size moved from the coarse-grained end (26.5 mm, 37.5 mm) to the fine-grained end (4 mm, 16 mm). There was a subtractive logarithmic relation between dissipated energy and average particle size (ds), and ds reduced by nearly 56.04 %. There was a critical value in ds. When ds was greater than this value, there was a positive correlation between energy dissipatation rate and crushing degree. Conversely, there was a negative correlation between them. At this value, the magnetite ore could be broken optimally. The results have certain reference value for the control of energy consumption in the crushing process of magnetite ore. |
Key words: magnetite ore impact load energy dissipation fragment distribution optimal crushing |
|
|
|
|