引用本文: | 王云飞,肖洪,杨广,蒋华毅,刘荣强,丁江民,郭宏伟.平行连杆式变形翼结构设计及分布式驱动配置[J].哈尔滨工业大学学报,2022,54(1):65.DOI:10.11918/202011032 |
| WANG Yunfei,XIAO Hong,YANG Guang,JIANG Huayi,LIU Rongqiang,DING Jiangmin,GUO Hongwei.Structure design and distributed actuators configuration of a parallel linkage morphing wing[J].Journal of Harbin Institute of Technology,2022,54(1):65.DOI:10.11918/202011032 |
|
|
|
本文已被:浏览 1279次 下载 996次 |
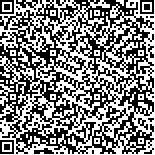 码上扫一扫! |
|
平行连杆式变形翼结构设计及分布式驱动配置 |
王云飞1,肖洪2,杨广2,蒋华毅1,刘荣强2,丁江民1,郭宏伟,2
|
(1.大连交通大学 机械工程学院,大连 116028; 2.机器人技术与系统国家重点试验室(哈尔滨工业大学),哈尔滨 150001)
|
|
摘要: |
为提高飞机飞行效率和多任务适应能力,设计一种兼顾高低速工况的变形翼骨架,并研究变形翼内部分布式驱动器的位置优化和数量布置问题。基于翼肋摆动变形方式,设计变弦长、变后掠、变面积、变展弦比的平行连杆式变形翼机构,以单元尺寸为参数,对翼肋摆动程度与展弦比进行分析,得到机翼参数变化曲线;以包含机翼骨架、驱动器和柔性蒙皮的单元为研究对象,通过实验法测定柔性蒙皮的等效弹簧刚度,并基于虚功原理,采用准静态力学分析方法,得到单元的力学模型,以单元变形量为目标优化函数,通过matlab优化工具箱fmincon函数求解,得到最优驱动器位置和蒙皮初始状态,并进行实验验证;采用Ansys软件模拟多个单元机构运动与弹性变形的耦合作用,得到多种驱动器布局下机构的最终平衡状态;设计了变形翼详细结构,完成了样机加工装配。结果表明:机翼平衡时的变形量与驱动器布局和结构刚度有关,当机翼结构刚度增强时,分布式驱动与单个驱动所做的变形量均收敛在理想值。采用分布式驱动会最大化变形量,更适合低刚度结构机翼,设计的变形翼样机可以实现连续变形。 |
关键词: 变形翼 平行连杆 顺气流优势 分布式驱动 优化布置 |
DOI:10.11918/202011032 |
分类号:V11 |
文献标识码:A |
基金项目:博士后基金(2020M681087) |
|
Structure design and distributed actuators configuration of a parallel linkage morphing wing |
WANG Yunfei1,XIAO Hong2,YANG Guang2,JIANG Huayi1,LIU Rongqiang2,DING Jiangmin1,GUO Hongwei2
|
(1. School of Mechanical Engineering, Dalian Jiaotong University, Dalian 116028, Liaoning, China; 2. State Key Laboratory of Robotics and System(Harbin Institute of Technology), Harbin 150001, China)
|
Abstract: |
To improve the flight efficiency and multi-mission adaptability of aircraft, a morphing wing framework for both high and low speed conditions is designed, and the position optimization and quantity arrangement of distributed drivers inside the morphing wing are studied. Firstly, based on a wing rib swing mechanism, a parallel linkage morphing wing mechanism with variable chord length, variable sweep, variable area, and variable aspect ratio was designed. Taking element size as the parameter, the aspect ratio and degree of wing rib swing were analyzed to obtain the variation curve of wing parameters. Then, a structure unit that contains the wing skeleton, actuator and flexible skin was chosen as the research object. Equivalent spring stiffness of the flexible skin was measured by an experimental method. Based on the principle of virtual work, a quasi-static mechanical analysis method was adopted to obtain the mechanical model of structure unit. Taking the deformation of the unit as the objective optimization function, the optimal driver position and initial state of the skin were obtained by the Matlab optimization toolbox fmincon function, and the experimental verification was carried out. Lastly, Ansys was used to simulate the coupling effect of multi-unit mechanism motion and elastic deformation, and the final equilibrium state of the mechanism under the layout of multiple drivers was obtained. The detailed structure of the morphing wing is designed and the prototype is fabricated and assembled. The results show that the balanced deformation of wing is related to the driver layout and structural stiffness. When the structural stiffness of the mechanism is enhanced, the deformation caused by distributed actuator and single actuator converges to the ideal value. The distributed drive will maximize the deformation, which is more suitable for the wing with low stiffness structure. Prototype of morphing wing can realize continuous deformation. |
Key words: morphing wing parallel linkage downstream advantage distributed actuators optimal placement |
|
|
|
|