引用本文: | 詹瑒,李奔奔,杨亚强,崔璟.FRP轴心受压构件弯曲屈曲临界力计算方法[J].哈尔滨工业大学学报,2023,55(9):111.DOI:10.11918/202109010 |
| ZHAN Yang,LI Benben,YANG Yaqiang,CUI Jing.Calculation method of critical load for flexural buckling of axially loaded FRP members[J].Journal of Harbin Institute of Technology,2023,55(9):111.DOI:10.11918/202109010 |
|
|
|
本文已被:浏览 783次 下载 1100次 |
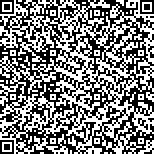 码上扫一扫! |
|
FRP轴心受压构件弯曲屈曲临界力计算方法 |
詹瑒1,李奔奔2,杨亚强3,崔璟4
|
(1.南京工程学院 建筑工程学院,南京 211167;2.南京工业大学 土木工程学院,南京 211816; 3.江苏科技大学 土木工程与建筑学院,江苏 镇江 212003;4.河南工业大学 土木工程学院,郑州 450001)[HJ0.7mm][HJ0.8mm]
|
|
摘要: |
为分析纤维增强复合材料(简称FRP)轴心受压构件弯曲屈曲临界力,建立了包含176根FRP轴压构件弯曲屈曲试验数据的数据库,总结并评价了目前用于预测FRP轴压构件弯曲屈曲临界力的5种计算模型(欧拉公式、Engesser修正公式、Haringx修正公式、Strongwell公司建议公式及Fiberline公司建议公式)。随后基于FRP构件初始弯曲实测值,提出FRP轴压构件整体稳定系数表达式,并建立考虑初始弯曲影响的FRP轴压构件弯曲屈曲临界力的理论计算模型;同时基于该数据库,通过回归分析建立FRP轴压构件弯曲屈曲临界力经验模型,并采用数据库及数值计算分别验证了上述两种新模型的准确性。最后,对两种新模型预测精度进行分析,结果表明:基于本文试验数据库(截面宽度在25.4~254 mm,高度在25.4~254 mm,有效长度在203~6 300 mm的构件),Strongwell公司建议公式误差最大,欧拉公式、Engesser和Haringx修正公式高估了FRP轴压构件弯曲屈曲临界力,Fiberline公司建议公式低估了弯曲屈曲临界力;本文提出的理论模型及经验模型在预测试验数据库涵盖的截面尺寸及有效长度的FRP轴压构件时,其预测精度均高于既有5种计算模型。推荐新模型应用于工字形、L形、方形及圆形截面的FRP轴心受压构件,可准确预测上述参数范围内的FRP轴心受压构件的弯曲屈曲临界力。 |
关键词: FRP构件 弯曲屈曲临界力 计算方法 数值计算 预测精度 |
DOI:10.11918/202109010 |
分类号:TU323.1 |
文献标识码:A |
基金项目:江苏省自然科学基金青年基金(BK20210550);江苏省高等学校自然科学研究面上项目(20KJB560003); 南京工程学院引进人才科研启动基金(YKJ201925) |
|
Calculation method of critical load for flexural buckling of axially loaded FRP members |
ZHAN Yang1,LI Benben2,YANG Yaqiang3,CUI Jing4
|
(1.School of Civil Engineering and Architecture, Nanjing Institute of Technology, Nanjing 211167, China; 2.College of Civil Engineering, Nanjing Tech University, Nanjing 211816, China; 3.School of Civil Engineering and Architecture, Jiangsu University of Science and Technology, Zhenjiang 212003, Jiangsu, China; 4.College of Civil Engineering, Henan University of Technology, Zhengzhou 450001, China)[HJ0.7mm]
|
Abstract: |
The critical loads for flexural buckling of axially loaded fiber reinforced polymer (FRP) members were investigated. A test database containing data of axial compression tests of 176 FRP members that failed in the flexural buckling mode was established. Five existing models proposed by Euler, Engesser, Haringx, Strongwell company, and Fiberline company for predicting flexural buckling loads were summarized and evaluated. An equation to determine the stability factor for global buckling of FRP members under axial compression was developed based on the observed initial crookedness of FRP members. Then, a theoretical model of flexural buckling loads of FRP members was proposed considering the influence of initial crookedness of FRP members. On the basis of the proposed database, an empirical model of flexural buckling loads of FRP members was derived through regression analysis. The two models were verified by the test database and numerical simulations. Finally, the performance of the two proposed models was analyzed. Results show that by using the proposed test database (section width of members is between 25.4 mm and 254 mm, section height is between 25.4 mm and 254 mm, and effective length is between 203 mm and 6 300 mm), the error of the model proposed by Strongwell company was the highest, and models proposed by Euler, Engesser, and Haringx overestimated the flexural buckling loads of FRP members, while that proposed by Fiberline company underestimated the flexural buckling load. The proposed theoretical model and empirical model both obtained more accurate results than the comparison models in predicting axially loaded FRP members within the range of section dimension and effective length covered by the test database. The proposed models were applicable to axially loaded FRP members with I-shaped, L-shaped, square, and circular sections, and could accurately predict the flexural buckling loads of axially compressed FRP members within the above parameter range. |
Key words: FRP members flexural buckling loads calculation methods numerical calculation prediction accuracy |
|
|
|
|