引用本文: | 潘诗洋,任纯吉,王君,赵鑫,辛远杰,王增丽,崔冬.爪式氢气循环泵高密封型转子及瞬态流动特性[J].哈尔滨工业大学学报,2023,55(12):76.DOI:10.11918/202212058 |
| PAN Shiyang,REN Chunji,WANG JUN,ZHAO XIN,XIN Yuanjie,WANG Zengli,CUI Dong.Transient flow characteristics of a claw hydrogen circulating pump with high sealing rotors[J].Journal of Harbin Institute of Technology,2023,55(12):76.DOI:10.11918/202212058 |
|
|
|
本文已被:浏览 790次 下载 1192次 |
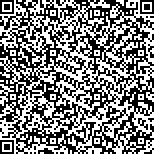 码上扫一扫! |
|
爪式氢气循环泵高密封型转子及瞬态流动特性 |
潘诗洋1,任纯吉1,王君1,赵鑫1,辛远杰1,王增丽1,崔冬2
|
(1.中国石油大学(华东) 新能源学院,山东 青岛 266580; 2.压缩机技术国家重点实验室(合肥通用机械研究院有限公司),合肥 230031)
|
|
摘要: |
爪式压缩机具有结构紧凑、干式无油和可靠性高等显著优点,是最具潜力的氢气循环泵泵型。传统爪式氢气循环泵转子间采用点与点的啮合方式,导致氢气在此处产生严重的泄漏,降低泵的容积效率,制约爪式氢气循环泵的发展。为减小爪式转子间的气体泄漏、提高泵的容积效率,本研究采用圆弧、高次曲线及其共轭曲线代替传统爪式转子的节圆型线,提出一种爪式转子间的新型曲折型啮合结构,进而构建一种新型高密封型齿轮爪式转子,有效解决了爪式转子间的气体泄漏问题。同时,建立新型齿轮爪式转子的几何模型,推导其截面型线方程。在工作过程中,对具有复杂几何边界的爪式氢气循环泵的内部气体的非定常流动进行数值模拟,对比分析了传统泵和新型泵工作腔内部的压力分布和瞬态流动特征;搭建了爪式氢气循环泵性能实验平台,验证了数值模拟结果的准确性。结果表明,相比于传统爪式转子,在压缩和排气过程中新型齿轮爪式转子间气体泄漏速度减小了31.42%和33.09%,容积效率提高了10.92%。 |
关键词: 氢气循环泵 齿轮爪式转子 几何性能 工作过程 间隙泄漏 数值模拟 |
DOI:10.11918/202212058 |
分类号:TH45 |
文献标识码:A |
基金项目:国家自然科学基金(52176029);青岛市科技惠民示范专项(23-2-8-cspz-6-nsh);压缩机技术国家重点实验室(压缩机技术安徽省实验室)开放基金(SKL-YSJ202006) |
|
Transient flow characteristics of a claw hydrogen circulating pump with high sealing rotors |
PAN Shiyang1,REN Chunji1,WANG JUN1,ZHAO XIN1,XIN Yuanjie1,WANG Zengli1,CUI Dong 2
|
(1.College of New Energy, China University of Petroleum (East China), Qingdao 266580,Shandong, China; 2.State Key Laboratory of Compressor Technology (Hefei General Machinery Research Institute Company Limited), Hefei 230031, China)
|
Abstract: |
The claw compressor is the most promising hydrogen circulating pump type due to its remarkable advantages of compact structure, dry oil-free and high reliability. However, conventional claw hydrogen circulating pumps suffer from severe gas leakage between two claw rotors due to point to point meshing, resulting in reduced volumetric efficiency of the pump and limiting the development of the hydrogen circulation pump. In order to minimize gas leakage between two claw rotors and improve the volumetric efficiency of pumps, this study proposed a novel twisting meshing structure adopting the circular arcs, high-order curves and their conjugate curves to instead of pitch circular arcs of conventional claw rotors. This leads to the development of a novel gear-claw rotor, effectively solving the issue of gas leakage between two claw rotors. Simultaneously, a geometric model of the novel gear-claw rotor was established, and the equations of rotor profiles were deduced. The transient flow of the internal gas in the hydrogen circulating pump with complex geometric boundaries was simulated in the working process. A comparative analysis was conducted between the pressure distributions and transient flow characteristics inside the working chamber of the conventional pump and the proposed gear-claw pumps. Additionally, a performance test bench for the claw hydrogen circulating pump was built to validate the accuracy of the numerical simulation results. The results indicated that compared with conventional claw rotors, the gas leakage velocity between the gear-claw rotors was reduced by 31.42% and 33.09% during the compression and discharge process, respectively, and its volumetric efficiency was increased by 10.92%. |
Key words: hydrogen circulating pump gear-claw rotor geometric performance working process gas leakage numerical simulation |
|
|
|
|