引用本文: | 方应冉,李兴高,刘泓志,杨益,郭易东.滚刀滑移状态下的受力与磨损仿真分析[J].哈尔滨工业大学学报,2024,56(5):93.DOI:10.11918/202204028 |
| FANG Yingran,LI Xinggao,LIU Hongzhi,YANG Yi,GUO Yidong.Simulation analysis of force and wear of disc cutters under sliding states[J].Journal of Harbin Institute of Technology,2024,56(5):93.DOI:10.11918/202204028 |
|
|
|
本文已被:浏览 2046次 下载 2434次 |
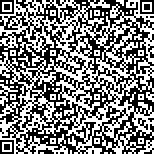 码上扫一扫! |
|
滚刀滑移状态下的受力与磨损仿真分析 |
方应冉1,2,李兴高1,2,刘泓志3,杨益1,2,郭易东1,2
|
(1.城市地下工程教育部重点实验室(北京交通大学),北京 100044;2.北京交通大学 土木建筑工程学院, 北京 100044;3.中交隧道工程局有限公司,北京 100088)
|
|
摘要: |
为探究滚刀滑移状态下破岩的受力与磨损的变化规律,基于离散单元法,建立了同时考虑滚刀自转和绕刀盘公转的滚动圆周切割模型。定义了一个滑移率参数η用于描述滚刀的滑移状态,对不同滑移率工况下滚刀破岩受力和磨损进行了对比分析,并结合工程实例对数值仿真结论进行了验证,结果表明:数值仿真中垂直力FV和滚动力FR在CSM模型计算值附近波动,两者较为吻合,表明了本文模型的合理性。数值仿真结果表明,随着滑移率η的增大,垂直力FV呈轻微减小趋势,滚动力FR明显变大,从滚动破岩到滑动破岩,垂直力FV降幅为23.6%,滚动力FR增幅达83.7%,滑动破岩将导致滚刀偏磨。工程实测数据表明,刀盘上大量滚刀处于正常磨损状态时,主要表现为推力增大。大量滚刀处于偏磨状态时,主要表现为扭矩增大,其中偏磨滚刀占比19.05%和28.57%时,扭矩增幅分别为55.85%和261.51%。滚刀正常磨损和偏磨均大量存在时,表现为扭矩推力同步增大,其中偏磨滚刀占比21.43%时,扭矩增幅为80.89%。数值仿真和实测数据表现出较高的一致性。综合4次开仓换刀结果,可将刀盘扭矩增幅超过50%作为判定大量滚刀发生偏磨的重要依据。 |
关键词: 全断面岩石掘进机(TBM) 离散单元法 运动状态 滑移率 滚刀偏磨 |
DOI:10.11918/202204028 |
分类号:TU452 |
文献标识码:A |
基金项目:国家重点基础研究发展计划(2015CB057800) |
|
Simulation analysis of force and wear of disc cutters under sliding states |
FANG Yingran1,2,LI Xinggao1,2,LIU Hongzhi3,YANG Yi1,2,GUO Yidong1,2
|
(1.Key Laboratory of Urban Underground Engineering of Ministry of Education(Beijing Jiaotong University), Beijing 100044, China; 2.School of Civil Engineering, Beijing Jiaotong University, Beijing 100044, China; 3.CCCC Tunnel Engineering Bureau Co., Ltd, Beijing 100088, China)
|
Abstract: |
In order to investigate the changes in rock cutting force and wear of disc cutters under sliding states, a rolling circumferential cutting model considering both the rotation of hob and the revolution of disc cutters is established based on the discrete element method. A slip ratio parameter η is defined to describe the sliding state of disc cutters. The force and wear of disc cutters are compared and analyzed under different slip rates η, and the numerical simulation conclusion is verified with an engineering example. The results show that the vertical force FV and rolling force FR in the numerical simulation fluctuate near the calculated value of CSM model, which are in good agreement, indicating the rationality of the model in this paper. The numerical simulation results show that with the increase of slip ratio η, the vertical force FV decreases slightly and the rolling force FR increases significantly. From cutting rock in rolling state to cutting rock in sliding state, the vertical force FV decreases by 23.6% and the rolling force FR increases by 83.7%, indicating that cutting rock under sliding state will lead to flat wear of disc cutters. The engineering data show that the increase of thrust is the main manifestation of a large number of disc cutters in the normal wear. When a large number of cutters are in flat wear, the main mainfestation is the increase of torque. Specifically, when the proportion of flat wear cutters is 19.05% and 28.57%, the increase of torque is 55.85% and 261.51% respectively. When there are a large number of normal wear and eccentric wear of cutters, the torque and thrust increase synchronously. The torque increases by 80.89% when the flat wear of cutters accounts for 21.43%. The numerical simulation and measured data show a high level of consistency. Based on the results of four opening, the increase of cutterhead torque by more than 50% can be used as an important basis for determining the flat wear of a large number of cutters. |
Key words: tunnel boring machine(TBM) discrete element method motion state slip ratio flat wear of disc cutters |
|
|
|
|